состав и пропорции, как изготовить с помощью формы в домашних условиях, видео
Когда речь заходит о надёжных, экономичных и недорогих строительных материалах, одними из первых вспоминаются арболитовые блоки. Из них получаются тёплые и удобные дома. Они изготавливаются из доступного дешёвого сырья. К тому же арболитовые блоки можно сделать своими руками, не переплачивая за готовые изделия промышленного производства.
Свойства и область применения арболитовых блоков
Арболитовые блоки — стеновой материал группы лёгких бетонов, применяемый в малоэтажном (до 3-х этажей) строительстве. Их стандартный размер 200х300х500 мм. Большинство производителей предлагаю более широкую линейку типоразмеров. Из арболитовых блоков строят жилые дома, малоэтажные коммерческие здания, технические строения, хозяйственные постройки.
Из арболитовых блоков строят жилые дома, коммерческие и технические здания, хозяйственные постройки
У арболита, как строительного материала, огромное количество преимуществ:
- Низкая теплопроводность;
- Минимальная звукопроницаемость;
- Высокая паропроницаемость;
- Биологическая стойкость;
- Пожаробезопасность;
- Малый вес;
- Удобный формат;
- Экологичность;
- Экономность и лёгкость монтажа;
- Долговечность;
- Низкая стоимость.
Малый вес и удобный формат арболитовых блоков позволяют экономить время и трудозатраты строителей
При грамотном изготовлении и применении арболитовых блоков вы добьётесь экономии сразу по нескольким статьям расходов: облегчённый фундамент, отсутствие дополнительной теплоизоляции, сокращение затрат на отопление, минимум отходов при строительстве.
К недостаткам стройматериала стоит отнести:
- Необходимость в оштукатуривании стен, защите от воды.
- Необходимость в использовании специальных кладочных составов – «тёплых» перлитовых растворов.
- Возможность использования только «дышащих» отделочных материалов.
- Расход времени на изготовление достаточного количества изделий.
- Риск повреждения некачественных блоков грызунами.
Стены из арболитовых блоков следует оштукатуривать, чтобы защитить от воды
Защитить постройку от нападений мышей и крыс можно заливкой высокого фундамента (0,5 м над уровнем грунта) либо армированием штукатурки металлической сеткой.
Из чего изготавливается арболит
Для производства арболитовых блоков вам понадобятся следующие составляющие:
- древесная щепа;
- химические добавки;
- цемент;
- вода.
Требования к размеру древесной щепы по ГОСТу — длина до 25 мм, ширина 5–10 мм, толщина 3–5 мм
Вы можете взять щепу другого размера, стружку, опилки. Но помните, что слишком крупная фракция снижает прочностные характеристики блока, а мелкая повышает его теплопроводность.
Опыт показывает, что наиболее прочный арболитовый блок получается из наполнителя удлинённой игольчатой формы.
Обычно сырьём служит чистая древесина сосны и ели, иногда лиственные породы. Щепа составляет 80–90% от общего объёма, поэтому материал часто называют древобетоном.
Арболитовый блок на 80–90% состоит из древесины, поэтому его легко распилить бензопилой
Древесина хорошо высушена — влажность не более 23%. Допускается включение коры и обзола до 10%. Нежелательно включение листьев, хвои, соломы.
В подборе наполнителя исходите из назначения будущей постройки. Если вы намерены строить жилой дом, качество сырья имеет первостепенное значение. Стеновой материал для хозяйственных построек можно сделать из третьесортного сырья, с включением любых растительных отходов. Их нужно будет лишь измельчить и хорошо высушить.
Химическая добавка необходима для минерализации щепы — нейтрализации сахаров и смол, содержащихся в древесных волокнах. Эти природные вещества препятствуют адгезии цементного раствора с древесиной и ухудшают его связывание. Для минерализации используются:
- сернокислый натрий (жидкое стекло).
- сернокислый алюминий.
- хлористый алюминий.
- хлористый кальций.
Химические добавки можно применять по отдельности либо парно в сочетании 1:1.
Дополнительно улучшить адгезию стружки и щепы можно 15%-ным известковым молоком перед их сушкой.
Сырьё залить раствором из расчёта 200 л раствора на 1 м³. Выдерживать в течение 4 дней, перемешивая массу 3–4 раза в день. Затем наполнитель разложить на открытом воздухе и периодически перемешивать. Процесс сушки занимает 3–4 месяца.
Цемент следует брать только марки М500, в крайнем случае – М400. Он обладает максимальными связующими свойствами, гидрофобностью, прочностью.
Расчёт расхода сырья
Необходимое количество арболита рассчитайте исходя из общей площади несущих стен за вычетом площади проёмов.
- Если вы намерены изготавливать стандартные блоки 20х30х50 см, значит, один блок в плоскости стены занимает 0,20 х 0,50 = 0,1 м².
- Разделив общую площадь стен в м² на 0,1 м², вы получите количество арболитовых блоков в штуках.
- Количество готового стенового материала измеряется в кубических метрах. Объём одного блока составляет 0,03 м³.
- 1 м³ арболита состоит из 33 блоков.
Для изготовления 1 м³ арболита потребуется:
- 250–300 кг портландцемента.
- 250–300 кг сухого наполнителя.
- 400 л воды.
- 8–10 кг химических добавок.
Оборудование и инструменты
В продаже имеются станки для изготовления арболитовых блоков на дому. Они облегчают и ускоряют трудоёмкую работу, но стоят дорого. Если вам необходим стеновой материал только для своего жилища, и вас не пугает длительность процесса, вы можете обойтись без дорогостоящего оборудования.
Вам понадобятся:
- бетономешалка принудительного действия;
- совковая лопата;
- формы для блоков;
- полиэтиленовая плёнка;
- деревянные поддоны;
- молоток;
- брусок-трамбовка.
Сушить арболитовые блоки следует 30 дней в тёплом, защищённом от осадков и ветра месте
Для изготовления арболита используется бетономешалка принудительного действия
Форму изготавливают из стального листа или деревянной опалубки. Металлическая форма состоит из двух частей. Короб изготавливается из стали сечением 1,0–1,5 мм. Его размер 30 х 50 см, высота 30 см. Крышка изготавливается из стали сечением 3,0 мм размером 33 х 53 см. На внутренних стенках короба на высоте 20,5 см от низа нанесите хорошо видимые метки. Ещё лучше по линии метки наварить крючки высотой около 5 мм, которые зафиксируют крышку на заданной толщине блока.
Форма для арболитовых блоков изготавливается из стали сечением 1,0–1,5 мм
Деревянную опалубку можно изготовить из обрезной доски: короб с размером по внутренним стенкам 31 х 51 см и пресс-крышку 33 х 53 см. Высота короба — 30 см. Внутренние стенки короба и низ крышки следует оклеить линолеумом, чтобы бетонная масса не налипала на их поверхности.
Инструкция по самостоятельному изготовлению
Подготовка сырья
- Просейте щепу через мелкое сито, чтобы удалить пыль, песок, мелкие включения.
- Засыпьте в бетономешалку 6 вёдер наполнителя. Запустите барабан.
- Растворите 300–400 мл химической добавки в 1 ведре воды.
- Медленно заливайте воду во вращающийся барабан.
Подождите несколько минут, пока щепа равномерно смочится раствором.
- Небольшими порциями добавляйте 1 ведро сухого цемента М500 в барабан. Доведите смесь до гомогенного состояния.
Формовка
- Готовую смесь высыпьте в корыто или поддон, откуда будет удобно набирать её лопатой.
- Застелите плёнкой поддон, на котором вы будете формовать блоки.
- Установите форму в углу поддона.
- Лопатой наполните форму до краёв, утрамбуйте массу бруском. Её усадка составит около 30%. Если необходимо, досыпьте бетон.
- Уложите крышку в форму, равномерно простукивайте её молотком, пока она не опустится до внутренних отметок высоты блока.
- Осторожно, сохраняя вертикальное положение, снимите короб с блока.
Если предварительно положите на середину крышки груз весом 2–3 кг, предохраните сырой блок от повреждения неожиданно приподнявшейся крышкой.
- Снимите крышку.
- Поместите короб формы в 15–20 см от готового изделия и приступайте к формовке следующего.
Чтобы получить максимально качественные блоки, распалубку следует делать не ранее, чем через 24 часа после формовки изделия. За это время прочность блока достигнет 30%. В этом случае лучше изготовить несколько десятков деревянных опалубок, которые можно снимать и использовать каждые 2–3 дня. 100%-ной прочности блоки достигнут спустя 30 дней хранения в тёплом, защищённом от осадков и ветра месте.
Видео: арболитовый блок своими руками
Для изготовления арболитовых блоков не нужны специальные знания и профильные навыки. И если вас не беспокоят затраты времени, необходимого для создания штучных изделий, изготовленный вами стеновой материал не уступит блокам, сошедшим с конвейера.
технология, станок для блоков, оборудование
Производство арболита — особенная технология изготовления стройматериала, который по своим свойствам приближен к натуральной древесине. Деревобетон отличается низким уровнем теплопроводности и достаточно доступной стоимостью. Блоки из арболита обладают рядом положительных качеств, главное из которых – это пригодность к возведению стен любых зданий. Особенности производства были популярны еще во времена Советского Союза, потом схему изготовления заменили другие технологии. Популярность этих плит возвращается на современный строительный рынок.
Оборудование для производства арболита позволяет изготовить доступный и практичный строительный материал, который отвечает требованиям ГОСТ 54854-2011. Легкие бетоны на органических наполнителях растительного происхождения имеют множество достоинств:
- стойкость к биологическим воздействиям;
- материал обладает паропроницаемостью;
- хорошая звукоизоляция;
- блоки из арболита устойчивы к огню;
- простота монтажа и легкая обработка поверхности.
Состав
Компонентная составляющая арболита – это важный этап технологии производства, который нуждается во внимательном соотношении всех компонентов. При изготовлении древоблоков важно чтобы качество приобретаемых материалов было высоким. Любой бетон включает в себя вяжущие элементы, песок, наполнитель (может быть легким либо тяжелым).
Важно! При замесе щепы ее следует смочить таким образом, чтобы не выделялась лишняя влага, а сам слой игольчатой структуры был покрыт цементным составом. При процессе трамбовки цемент послужит связующим звеном, наружные поры у блоков закроются, таким образом, изделие станет не продуваемым.
Размеры щепы влияют на количество цемента, который будет использоваться при приготовлении одного кубометра арболита. Когда щепа изготовлена из сухого дерева, получается мелкая фракция. Игольчатая структура для скрепления между собой требует большего количества цемента. Необходимый объем материалов для изготовления одного кубометра арболита:
- 8-10 кг химических препаратов;
- 250 кг цемента;
- примерно 200-250 кг щепы.
В щепу добавляют такие материалы:
- гашеную известь;
- раствор жидкого стекла;
- портландцемент;
- хлористый калий;
- алюминиевую и сернокислую кальциевую смесь.
Технология
Изготовление блоков из арболита организовывают как в домашних условиях, так и налаживают масштабное производство, как прибыльный бизнес. Для этого учитывают все аспекты и стадии изготовления, руководствуются нормативными документами.
Технологию производства арболита по ГОСТУ необходимо начать с подготовки нужных ингредиентов, из которых 85 % составляет деревянные компоненты. Применяется древесная щепа, опилки, стружка. Наиболее подходящие породы древесины: сосна, пихта, ель, тополь, осина, береза. Допускается присутствие коры, листьев и хвои – не больше 5 % от общего объема. Заготовки пропускаются через станок для щепы и измельчаются. Рекомендуемый размер частичек 5х25 мм. Разнофракционный состав будет обеспечивать нужную плотность арболита.
Производство плит из арболита крупных габаритов требует дополнительное армирование изделия.
В форму, заполненную на половину, следует поместить арматурный каркас из арматуры и далее заполнить деревобетонным составом.
Технология подготовки древесного сырья в домашних условиях производится различными методами – сооружение щепореза своими руками либо заключение договора с лесопилкой о поставке отходов деревообработки.
В промышленном производстве в сырье добавляют химические реагенты – хлористый кальций, сернокислый алюминий, жидкое стекло. При домашнем изготовлении рекомендуется выдерживать щепу три месяца на улице при этом опилки следует периодически перемешивать. Чтобы ускорить процесс в насыпь добавляют окись кальция – на один кубометр идет 200 литров 1.5 % раствора.
В роли вяжущего элемента подойдет портландцемент 400 – 600 марки. Смесь состоит на 10-15 % из цемента и не более 1% пластификаторов и деминерализаторов. Перед смешиванием составляющих частей, древесный компонент заливают 10 % раствором извести, потребуется выдержать 3 часа. На промышленных предприятиях такая методика вымачивания в технической емкости занимает до 3 дней.
Все компоненты смешиваются в бетономешалке. В итоге получится однородная масса без комков. Состав воды-щепы-цемента равен 4:3:3. Смесь должна быть немного рассыпчатой по консистенции и при сжатии держать форму.
Процесс получения древоблоков
На стадии формовки используются лотки, которые придают изделиям стандартные размеры. Если требуется сделать блоки нестандартных габаритов, в формы вставляются пластины, которые увеличивают размер и массу изделия. Плита может быть треугольной или трапециевидной.
Для ускорения затвердевания в раствор добавляют сухую хлористо-кальциевую смесь. Заливание раствора делают слоями в три этапа в заранее обработанные формы известью. Далее смесь потребуется утрамбовать.
Верхнюю поверхность блоков рекомендуется выровнять шпателем или правилом. После залить штукатурной смесью, примерно на 20 мм.
Когда образовалась у стройматериала форма, его уплотняют при помощи деревянного приспособления обитого металлической рамой. Наиболее прочным и надежным является стройматериал, который выстоял и затвердел на протяжении 10 суток при температуре +150 градусов Цельсия. Чтобы блоки не пересыхали, их периодически поливают водой.
Оборудование
Нужные агрегаты по изготовлению арболита продаются в сборе и включают в себя все циклы обработки и приготовления. Передовые технологии позволяют делать различные объемы стройматериала с разными размерами. Для сооружения станка своими руками, понадобятся такие агрегаты:
- щепорез, который также можно сконструировать своими руками;
- бетонорастворомешалка либо смесительный аппарат;
- пресс-формы;
- вибростанок.
Производить арболит можно самостоятельно организовав выпуск блоков, и при этом минимизировать затраты на нужную технику. Станок для дробления щепы также изготавливается своими руками при помощи использования подручных устройств. Для экономии средств вибросито заменяют на ручной метод просеивания.
Агрегат для изготовления рабочего раствора рекомендуется заменить автобетономешалкой. Ручной способ замешивания в методике недопустим, так как имеется риск образования в растворе комков и сгустков.
Формы требуемой величины делают из обычных деревянных ящиков. Дно и бока рекомендуется, заслать линолеумом либо пленкой из полиэтилена, это позволит составу не влипать в стенки.
Когда формы будут залиты по технологии, смесь уплотняют. Для этого понадобится молоток для простукивания стенок в емкости и дрель, которой делают вибропресс. Также используют самостоятельно сделанный вибростол. Этот аппарат уменьшит время изготовления и повысит производительность.
Если условия для сушки материала не подходят, рекомендуется воспользоваться сушильной камерой. Такой метод сушки увеличит затраты на производство и сделает прочность блоков выше.
Станок для блоков арболита своими руками чертеж
- Вибропресс с механизмом фиксации формы.
- Форма с функцией самозапечатывания.
- Подъемно-поворотный бункер с механической подвеской.
- Лебедка для управления бункером.
- Смеситель.
- Лебедка для подъема дозаторов с подвеской.
- Тележка с дозатором для щепы.
- Дозатор для цемента на тележке.
- Емкость для приготовления древесного консерванта.
- Платформа наклонная.
- Поддон.
- Рокла.
- Металлическая конструкция.
Производство своими руками
Технология самостоятельного изготовления арболита не сложная при наличии необходимого инструмента и устройств. Если соблюдать все правила и критерии изготовления, правильно рассчитать компоненты продукт будет иметь высокое качество и прочность.
Материалы и приспособления:
- Специальная емкость для компонентов.
- Вибрирующий стол.
- Поверхность с ударно встряхивающими функциями.
- Металлические поддоны.
- Для того чтобы получить качественный раствор необходима автобетономешалка. Если смешивать собственноручно, то для получения раствора нужной консистенции понадобится много времени и сил.
- Специальные пластиковые формы необходимых размеров. Арболитовые блоки имеют прямоугольную форму, стандартные размеры – 500х189х300 мм и 500х188х200 мм.
- Специальный станок профессионально измельчит щепу.
- При помощи пресса получается высокая плотность материала. При процессе трамбовки из материала по максимуму убирается воздух.
- Камера для сушки блоков из арболита превращает структуру в твердый однокомпонентный материал.
- Лопаты для того чтобы загрузить смесь в формы.
- Армирующая сетка применяется для скрепления древоблоков.
При наличии таких приспособлений в среднем производится за месяц от 400 до 500 кубометров строительной смеси. Рекомендуемая минимальная величина производственного помещения 500 м2. Расходы электроэнергии составят 15-45 кВт?ч. При подготовительных работах органические компоненты заливают жидким цементом до образования однородной массы. Соблюдая пропорции и расчеты, получившаяся смесь должна быть сыпучей.
Бункеры и формы имеют стандартный размер 20х40х60 см их можно сварить или сделать наборными из раскроенных листов металла. Рекомендуется блоки при изготовлении располагать вертикально, это упростит трамбовку при малой площади пресса.
Отзывы и рекомендации специалистов при самостоятельном производстве блоков
Эксперты и частные строители, практикующие изготовление арболитовых блоков оставляют отзывы, в которых советуют следовать правилам, помогающим достичь высокого качества продукции.
- В технологии производства рекомендуется применять не только щепу больших размеров, но и применять опилки и деревянную стружку.
- Консистенцию древесины обрабатывают таким образом, чтобы из нее удалился сахар. Методика позволит предотвратить дальнейшее вспучивание готового материала, что категорически недопустимо в постройке домов.
- В процессе изготовления раствор нужно тщательно перемешать и проследить, чтобы все части были в цементном растворе. Этот момент важен для качественного и прочного скрепления древесных и прочих материалов в блоках.
- При изготовлении важно добавлять алюминий, гашеную известь и прочие компоненты.
Например, добавленное в состав жидкое стекло не будет позволять впитывать влагу готовому стройматериалу, а гашеная известь обладает антисептическими свойствами.
- Хлористый калий не позволит образоваться в структуре микроорганизмам и прочим веществам, влияющим неблагоприятно на материал.
- При смешивании компонентов рекомендуется следить за пропорциональностью, чтобы приготовленная смесь соответствовала требованиям производства блоков из арболита.
Производственная линия ВПЛ — Арболит для производства блоков с доставкой по России
Производственная линия ВПЛ-Арболит – малогабаритная установка, позволяющая производить арболитовые блоки (ГОСТ 19222-84) методом вибро-прессования, с последующей выдержкой в металлических формах. Данная установка используется в коммерческом производстве строительных материалов.
Комплектация линии ВПЛ-Арболит:
- Измельчитель древесины ИД600 М
- Растворосмеситель одновальный САБ-400
- Подъемно-поворотный бункер с механизмом подъема, лебедкой и металлоконструкцией ППБ-300.
- Вибропресс Универсальный
- Формы для производства стеновых блоков — 100 шт.
Принцип работы ВПЛ-Арболит:
В бетоносмеситель загружаются компоненты для приготовления арболитовой смеси. Далее готовый раствор выгружается из растворосмесителя в подъемно-поворотный бункер. Бункер устанавливается над формами, после чего работники заполняют формы арболитовой массой при включенном вибраторе. После наполнения форм, они устанавливаются в положение «закрытия» на вибропрессе. Оператор с помощью пульта управления, опускает прижимную платформу до характерного щелчка, который свидетельствует, что форма закрыта. Платформа возвращается в исходное положение, оператор меняет закрытые формы на пустые. Далее процесс повторяется.
Меры предосторожности:
- Оборудование должно быть установлено на ровной, прочной, хорошо освещенной площади.
- Подключение к электросети и заземление обязан производить аттестованный электрик.
- Работники должны быть проинформированы и обучены работе на установке.
- Перед началом работы, обязательно производить осмотр всех частей линии.
- После рабочей смены, оборудование необходимо обесточить и очистить от следов раствора.
Преимущества линии ВПЛ-Арболит:
- Невысокая стоимость оборудования
- Быстрая установка с минимальными затратами на подготовку производства
- Для работы достаточно трех человек
- Не требуется высокой квалификации сотрудников
- Высокое качество выпускаемой продукции
- Минимальный срок окупаемости линии
Приобретение производственной линии ВПЛ-Арболит откроет для вашего бизнеса новую перспективную возможность привлечения денежных потоков. Арболит – уникальный материал, спрос на который возрастает с каждым месяцем, благодаря наличию особого набора качеств. Арболитовые блоки являются успешной комбинацией древесины и бетона, получившей лучшие свойства от каждого из материалов:
- Он также легок и практичен, как древесина, ввиду чего позволяет значительно сократить стоимость доставки к месту строительства и сроки возведения зданий.
- Обладает отличными гигиеническими свойствами – не накапливает влагу и безупречно сохраняет тепло, не подвержен поражению грибком и обеспечивает хороший воздухообмен в помещении.
- От бетонных блоков арболит унаследовал безупречную форму, позволяющую создавать качественную кладку, без щелей и мостиков холода, прочность и долговечность построек.
Приобретение производственной линии ВПЛ-Арболит сейчас позволит вам быстро получить вход в зону покупательского спроса и прочно удержать позиции своей компании на рынке.
оборудование, технология, пропорции и формы
Рейтинг материала
16 out of 5
Практичность16 out of 5
Внешний вид20 out of 5
Простота изготовления20 out of 5
Трудоемкость при использовании20 out of 5
ЭкологичностьИтоговая оценка
Арболитовые блоки относятся к легким стеновым строительным материалам. Они изготавливаются из опилок, древесины, цемента, воды и других составляющих.
В качестве основной составляющей используется древесная щепа, которая представляет собой рубленую древесину. У таких блоков больше граница прочности, чем у пеноблоков и газоблоков. Важными характеристиками материала являются: высокая устойчивость к трещинам и ударопрочность.
Технология производства
Первоначальным этапом производства арболита является тщательная подготовка всех необходимых компонентов, затем следует приготовление основы, ее отлив в формы для дальнейшего получения блоков.
Подготовка основы
Наполнитель для блоков включает в себя стружки и опилки в пропорции 1:2 или 1:1. они должны быть хорошо просушены, для этого их выдерживают 3-4 месяца на открытом воздухе, периодически переворачивая и обрабатывая раствором извести.
В последнем случае на 1 куб. метр сырья необходимо около 200 л раствора извести 15%. В нем будут находиться древесные компоненты в течение 4 дней, которые требуется перемешивать 2-4 раза в день.
На данном этапе главная цель – это убрать сахар, содержащийся в опилках. Он может стать причиной их дальнейшего гниения.
Щепу можно купить готовую, а можно сделать самим, соорудив щепорез. Что это такое и как он работает, расскажет видео:
Необходимые компоненты
После того как опилки подготовлены, к ним присоединяют следующие добавки:
- Гашеная известь;
- Сернокислый кальций и алюминий;
- Портландцемент 400 марки;
- Растворимое жидкое стекло;
- Хлористый кальций.
Как правило, доля этих компонентов в арболитовой смеси не превышает 4% от массы цемента. Они придают конечному продукту устойчивость к гниению, обеспечивают высокую огнеупорность и пластичность.
Технология изготовления
Арболитовые блоки имеют оптимальные параметры 25 см*25 см*50 см. они удобны не только в процессе изготовления, но и при укладке. Процесс отливки заключается в следующем: блоки заполняются арболитовой смесью из трех слоев. После каждого подхода следует тщательное уплотнение деревянным молотком, обшитым жестью.
Лишняя масса ударяется при помощи линейки, а форма выдерживается сутки с температурой воздуха от +18оС. По истечению времени блоки извлекаются из форм путем небольшого постукивания и выкладываются на ровное основание для полного затвердения на 2 дня и просушивания на срок от 10 дней.
На фото — процесс выемки арболитового блока из станка после формовки:
Оборудование
Чтобы производить арболитовые блоки может потребоваться различное оборудование в зависимости от объема производства и используемого сырья. Процесс изготовления данного строительного материала и его конечный результат должны отвечать ряду критериям: ГОСТ 19222-84 и СН 549-82.
Чаще всего для производства арболита используются остатки деревьев хвойных пород. Их измельчение производится на рубильной машине (РРМ-5, ДУ-2 и прочие). Более тщательный процесс дробления производится на дробилках (ДМ-1) или молотковых мельницах. На вибростолах из измельченной древесной смеси отделяются кусочки земли и коры.
Саму арболитовую смесь рекомендуется приготавливать на лопастных растворосмесителях или смесителях принудительного цикличного действия. Перевозить готовую смесь к специальным формам можно с помощью кюбелей или бетонораздатчиков. А сам подъем транспортера не должен превышать 15о вверх и 10о вниз при скорости движения до 1 м/с. Падение смеси осуществлять на высоте не более одного метра.
Уплотнение конструкций можно произвести как ручными трамбовками, так и вибропрессом (Рифей и прочие). Если изготовить блоки из арболита необходимо в небольших объемах, то можно воспользоваться специальным мини-станком. Если речь идет о промышленных масштабах, то используют целые линии по производству арболитовых блоков, которые включают в себя станки для изготовления блоков, прессы и смесители.
Так выглядит линия по производству арболитовых блоковЛучший процесс затвердения достигается путем использования тепловых камер с ТЭНом, ИК-излучением и т.
Формы для блоков
Формы для производства арболитовых блоков могут быть следующих размеров: 20 см*20 см*50 см или 30 см*20 см*50 см. для строительства конструкций из арболитовых блоков формы могут выпускаться и других размеров (для перекрытий, вентиляционных систем и т. д.).
Формы для блоков можно купить, а также можно изготовить своими руками. Для этого понадобятся доски толщиной 2 см, которые сбиваются в необходимую по размерам форму. Внутренняя часть обшивается фанерой и сверху пленкой или линолеумом.
Схема по изготовлению формы для арболитовых блоков
Как сделать арболитовые блоки своими руками
Список оборудования:
- Разъемная форма и вставки для нее;
- Падающий и вибростол;
- Установка для подъема формы;
- Ударно-встряхивающий стол;
- Лоток для смеси;
- Поддон для формы из металла.
Имея все необходимое оборудование для производства блоков, можно получать 300-400 м3 стройматериала в месяц. При этом площадь для установки всего оборудования потребуется около 500 кв. м и затраты на электроэнергию 10-40 кВт/ч.
Изготовление больших блоков требует их дополнительного армирования. Когда форма заполнена на половину арболитовой смесью, сверху заливается слой бетона с арматурой, после этого продолжается заполнение арболитом.
При самостоятельном изготовлении блоков из арболита органические вещества необходимо залить водой, после чего – цементом до однородного состояния. Для этого потребуется 3 части цемента, 3 части опилок или древесной стружки и 4 части воды. Получившаяся смесь должна быть сыпучей и в тоже время удерживать форму при сжатии в руке.
Перед заливкой внутренняя часть формы смазывается известковым молочком. После этого можно выкладывать подготовленную смесь слоями с тщательной утрамбовкой. Поверхность блока выравнивается шпателем и заполняется штукатурным раствором на высоту 2 см.
Видео о том, как осуществляется производство арболитовые блоки своими руками:
youtube.com/embed/Q-PLQ4Y4SYk?rel=0″ frameborder=»0″ allowfullscreen=»»/>
Рекомендации
- Уплотнить смесь можно при помощи дерева, обитого железом.
- Наибольшей прочностью обладают блоки, которые находились под пленкой во влажном состоянии около 10 дней. При этом температура воздуха не должна быть ниже 15 градусов.
- Предотвратить пересыхание блоков можно, периодически поливая их водой.
Достаточно просто самостоятельно изготовить данный строительный материал. Если соблюдать все технологии, то конечный продукт будет прост в применении, обладать высокой прочностью, пожаробезопасностью и длительным сроком эксплуатации.
Понравилась статья? Поделитесь с друзьями в социальных сетях:Вконтакте
Одноклассники
Google+
И подписывайтесь на обновления сайта в Контакте, Одноклассниках, Facebook, Google Plus или Twitter.
Станки для производства арболитовых блоков, арболита в Златоусте
Он прошёл проверку временем и сибирскими морозами, прошёл испытания и был стандартизован ещё в СССР в 60-х годах.
Сегодня арболит удовлетворяет всем требованиям современного человека, решившего построить дом. Вы можете купить станки для производства арболита в Златоусте у нас.
Арболит – строительный материал,
изготовленный из смеси трёх компонентов:
древесная щепа | |||
минеральная добавка | |||
цемент марки 500 |
100% ЭКОЛОГИЧЕСКАЯ БЕЗОПАСНОСТЬ И БИОСТОЙКОСТЬ |
Арболитовый блок является экологически безопасным строительным материалом на основе натуральной щепы хвойных и лиственных пород дерева, безвреден для человека и окружающей среды, не подвержен гниению, обладает хорошей воздухопроницаемостью (в доме из арболита не бывает сырости).
ПЛАСТИЧНОСТЬ |
В случае возникновения предельных нагрузок арболитовый блок не ломается, а лишь обратимо деформируется с возможностью восстановления первоначальной формы.
Кроме того, он не требует чрезмерно бережного обращения при транспортировке.
НИЗКАЯ ТЕПЛОПРОВОДНОСТЬ |
Арболит является одним из самых тёплых строительных материалов. Стена, построенная из арболитовых блоков толщиной всего 30 см, по показателям теплопроводности равна стене из кирпича толщиной в 1 метр и не требует дополнительного утепления!
ТОЧНОСТЬ ГЕОМЕТРИИ И ПРОСТОТА ОБРАБОТКИ |
В арболит можно легко вбивать гвозди, ввинчивать шурупы и вешать крючки, как на обычную деревянную стену. Он свободно поддаётся сверлению, рубке и распилу. При этом получается точная и аккуратно подогнанная по размерам форма блока.
ВЫСОКАЯ ПРОЧНОСТЬ |
Арболитовый блок характеризуются высокой прочностью и может использоваться в строительстве даже трёхэтажных домов с железобетонными плитами перекрытий.
ЗВУКОИЗОЛЯЦИЯ |
Коэффициент звукопоглощения арболитового блока при частотах 125-2000 Гц составляет 0,17-0,60, в то время как у кирпича при 1000 Гц он не превышает 0,04, а у древесины – 0,06-0,10.
ПОЖАРНАЯ БЕЗОПАСНОСТЬ |
Арболит относится к трудногорючим (группа Г1 по ГОСТ 12. 1.044-89), трудновоспламеняемым (группа В1 по ГОСТ 30402-96), малодымообразующим (группа Д1 по ГОСТ 12.1.044-89) материалам.
НИЗКАЯ СТОИМОСТЬ И СЖАТЫЕ СРОКИ |
1 кубический метр блоков из арболита в 3 раза легче кирпича и в 1,5 раза легче керамзитобетона, что позволяет использовать мелкозаглубленный ленточный фундамент шириной всего 30 см, что значительно экономит деньги будущего владельца дома.
Стены из арболитового блока возводятся в кратчайшие сроки, а отделка возможна сразу после строительства.
Вибропресс «Скала-Арболит» | Строй Маш Киров
Гидравлический вибропресс «Скал-Арболит» это технологичный высокпроизводительный станок для производства арболитовых блоков, также при необходимости на нём можно производить другие любые строительные блоки (шлакоблоки, керамзитоблоки и т.д. и т.п.).
Гидравлический вибропресс для производства арболитовых блоков
Надёжный и производительный вибпропресс «Скала-Арболит» оборудование для арболита, которое позволит выпускать качественные, геометрически точные, в большом количестве с малыми затратами на производство арболитовые блоки любого доступного размера.
Технические характеристики вибропресса «Скала-Арболит»: | |||||||||
---|---|---|---|---|---|---|---|---|---|
«Скала-Арболит 1» | «Скала-Арболит 2» | «Скала-Арболит 3» | |||||||
Производительность до: | цикл | в час | в смену | цикл | в час | в смену | цикл | в час | в смену |
— блок 390х190х190, шт. м.куб. | 3 0,04 | 180 2,4 | 1440 19,2 | 4 0,06 | 240 3,4 | 1920 27 | 6 0,08 | 480 5,1 | 3840 40,5 |
— блок 400х300х200, шт. м.куб. | 2 0,05 | 180 2,9 | 960 23 | 3 0,07 | 180 4,2 | 1440 33,6 | 4 0,1 | 240 5,8 | 1920 46,4 |
— блок 500х300х200, шт. м.куб. | 1 0,03 | 60 1,8 | 480 14,4 | 2 0,06 | 120 3,6 | 960 28,8 | 3 0,09 | 180 5,4 | 1440 43,2 |
Формовочная площадь, мм | 650х450 | 850х450 | 1050х620 | ||||||
Высота формуемого изделия, мм | 150-200 | 150-200 | 150-200 | ||||||
Размер тех.![]() | 800х500х30 | 1000х500х30 | 1200х620х40 | ||||||
Размер тех. поддона доска, мм | 800х500х50 | 1000х500х50 | 1200х620х50 | ||||||
Время цикла, минут | до 1 | до 1 | до 1 | ||||||
Усилие прессования, кг | 8000 | 8000 | 8000 | ||||||
Напряжение питания | 380 | 380 | 380 | ||||||
Мощность виброплощадки, кВт | 2х0,5 | 2х0,5 | 2х0,5 | ||||||
Мощность гидростанции, кВт | 4 | 4 | 4 | ||||||
Рабочая площадь, кв.м. | 10-15 | 15-20 | 20-25 | ||||||
Количество рабочих, чел | 1-2 | 1-2 | 1-2 | ||||||
Габаритные размеры, мм | 1350х1070х2000 | 1550х1070х2000 | 1750х1170х2000 | ||||||
Размер гидростанции, мм | 800х300х1270 | 800х300х1270 | 800х300х1270 | ||||||
Общий вес оборудования, кг | 750 | 950 | 1150 | ||||||
Стоимость (без оснастки), | 212 600 | 226 600 | 251 350 |
Комплектация вибропресса «Скала-Арболит»:
- Массивная конструкция гидравлического станка для арболита с гидроцилиндрами и виброплощадкой – 1 штука.
- Оснастка (матрица + пуансон) — в комплект не входит.
- Гидравлическая станция с пультом управления — 1 штука.
- Комплект шлангов и соединительных элементов – 1 комплект.
- Поддон (образец) – 1 штука.
- Паспорт (инструкция по эксплуатации) – 1 штука.
Конкурентные преимущества вибропресса «Скала-Арболит»:
- Отличная геометрия матрицы для блока до +/- 1 мм!
- Отличное качество выпускаемого блока!
- Высокая производительность до 45 кубов смену!
- Множество размеров выпускаемой продукции, более 10 размеров блоков!
- Высокое качество оборудования по выгодной цене, срок службы станка 5-7 лет!
Принцип работы вибропресса «Скала-Арболит»:
- В гидравлический станок для арболитового блока производится загрузка инертных, химии и вяжущего (цемент) в пропорциях, согласно рекомендаций по смесям, в бетоносмеситель принудительного типа.
- При достижении однородности смеси, с помощью ленточного транспортёра, смесь перегружается в бункер-накопитель вибропресса для арболитовых блоков.
- На бункере-накопителе открывается челюстной затвор ручкой, смесь отгружается в нужном объёме в матрицу.
- Смесь в матрице разравнивается, ручным приспособлением.
- На формовочной площадке станка для арболита, включается вибратор на несколько секунд, смесь в форме уплотняется. После предварительного уплотнения добавляется немного смеси, и она окончательно выравнивается по краю формы.
- Выровняв поверхность смеси в форме и нажав на рычаг гидрораспределителя, пуансон опускается в матрицу и сдавливает смесь, при включённом вибраторе, выдавливая остатки воздуха пуансон прессует смесь в форме до нужной плотности и высоты блока, цикл вибропрессования занимает до 10 секунд.
- Закончив процесс вибропрессования, выключается вибратор, после его остановки, с помощью перемещение нужного рычага, поднимается матрица и пуансон над отформованными блоками.
- Готовые блоки с поддоном перемещаются к месту сушки (сушку можно осуществлять естественным способом или пропариванием), а на виброплощадку вибропресса для арболитовых блоков подаётся новый поддон.
Цикл формовки повторяется вновь.
Оборудование для механизации производства арболитовых блоков на вибропрессе «Скала-Арболит»
Оборудование для вибропресса «Скала-Арболит» предназначено для механизации производственного процесса при изготовлении арболитовых блоков. Оборудование для изготовления арболита имеет следующее характеристики и параметры:
Бункер-накопитель вибропресса для арболита, накапливает смесь, имеет челюстной затвор для дозации бетонной смеси.
Модуль загрузки смеси станка для арболита, предназначен для автоматизированной загрузки матрицы вибропресса, управляется с пульта управления, снижет уровень ручного труда и позволяет механизировать производство.
Модуль подачи поддонов, подаёт поддон на формовочную площадку вибропресса для арболита.
Накопитель со стеллажом, позволяет принимать поддоны с формовочной площадки вибропресса для арболитовых блоков, накапливать их вряд, а потом снимать стеллаж и перемещать его к месту сушки, стеллажи можно устанавливать друг на друга.
Модуль подачи и укладки поддонов со стеллажом, позволяет подавать и снимать поддоны с формовочной площадки вибропресса для арболитовых блоков и укладывать их на стелаж, для последующей транспортировки к месту сушки.
Ленточный конвейер для загрузки бункера-накопителя бетонной смесью из бетоносмесителя.
Бетоносмеситель принудительного типа СБР без скипа загрузка компонентов осуществляется в чашу смесителя вручную, для облегчения загрузки компонентов чашу бетоносмесителя можно использовать скиповый подъёмник для бетономешалки СБР.
Щепорез (шеподробилка, рубительная машина) для измельчения деревянных заготовок в щепу нужного размера, применяется при производстве арболитовых блоков.
Стоимость дополнительного оборудования для вибропресса «Скала»: | |
---|---|
Наименование | Стоимость, |
Бункер-накопитель для вибропресса | от 24 200 |
Выкатная телега для технологического поддона | от 28 200 |
Накопитель со стеллажом | от 27 000 |
Модуль подачи поддонов (рассчитан на 12 поддонов) | от 87 000 |
Модуль штабелирования поддонов с готовыми изделиями | от 180 000 |
Модуль подачи и укладки поддонов | от 220 000 |
Ленточный транспортёр ЛК-400-3300 | 116 600 |
Ленточный транспортёр ЛК-400-5300 | 166 600 |
Принудительный бетоносмеситель СБР (без скипа) | от 71 500 |
Скиповый подъёмник для бетоносмесителя СБР | от 60 000 |
Эстакада под бетоносмеситель СБР со скипом | от 40 000 |
Система «Скип-Дозатор» | от 60 000 |
Щепорез (дробилка для дерева) | от 77 000 |
Комплекс для производства арболита
Изготавливаем высокорентабельное оборудование для переработки древесных отходов.
Оборудование предназначено для изготовления арболитовых блоков на основе отходов лесоперерабатывающей промышленности (опилок или щепы), вяжущего компонента портландцемента.
Технология производства позволяет получать высококачественный строительный материал арболит, не имеющий аналогов по совокупности свойств на рынке строительных материалов. Получаемый материал арболит соответствует всем требованиям ГОСТов. Арболит экологичен и прост в применении.
Данная технология позволяет производить арболит, полностью соответствующий ГОСТу. Конечная продукция — геометрически точные арболитовые блоки, которые успешно применяются при строительстве всех видов общественных, промышленных зданий и жилых домов.
Для производства арболитовых блоков требуются следующие компоненты:
- опилки, щепа и другие отходы лесной и деревообрабатывающей промышленности
- вяжущий компонент — цемент
- вода
- сернокислый алюминий
Оборудование позволяет расширить возможности бизнеса в строительной отрасли, открыть свое дело со стабильным ежемесячным доходом.
Оборудование для производства арболита решает проблемы, связанные с утилизацией и переработкой древесных отходов. С его помощью отходы лесопереработки используются вторично, на предприятии создается непрерывный производственный цикл по переработке древесины.
Видео оборудования для производства арболита
;
Производство арболита — уникального строительного материала — еще один способ переработки отходов деревообрабатывающих и лесозаготовительных предприятий. Сочетание дерева и бетона открывает новые свойства привычных материалов, позволяет приобрести им положительные качества, устраняя присущие изначально недостатки. Арболит прочен как бетон, при этом легок и экологичен как дерево. Легко пилится обычной ножовкой и при этом способен выдержать падение с высоты 10 метров, не горит, не гниет, имеет прекрасные тепло- и звукоизоляционные свойства.
Относящийся к классу ячеистых бетонов арболит, согласно ГОСТ 19222-84, используется как для малоэтажного строительства, так и для утепления строительных конструкций. Материал может успешно применяться для строительства жилых домов и производственных сооружений до трех этажей в любых климатических условиях.
Комплекс для производства арболита позволяет наладить выпуск строительных блоков различного назначения и размеров — от стандартных кирпичей, до крупных армированных конструкций с фактурным слоем. Плотность выпускаемого материала варьируется от 400 кг/м3 для теплоизоляционных марок арболита, до 900 кг/м3 для конструкционных.
4 различных формы бетона и их использование в образовании Америки
Опалубка используется для изготовления форм из определенных материалов, на которые заливается бетон. Существует ряд различных типов бетонных опалубок, используемых в строительстве, и метод выбора обычно зависит от технических характеристик проекта.
Опалубка используется строителями и подрядчиками в качестве инструмента для быстрого завершения проектов, предлагая надежный способ отлить и построить жизненно важные компоненты конструкции, такие как крыша и полы.
Обычно после заливки бетон оставляют для затвердевания в конструкции, после чего снимают опалубку. Однако с появлением методов несъемной опалубки ее часто оставляют как часть конструкции.
Формы для бетонных плит
Деревянные опалубки — самые основные и самые старые из бетонных опалубочных плит, которые до сих пор широко используются при возведении небольших конструкций.
Деревянные формы состоят из деревянных досок, обычно фанеры, которые могут быть прикручены или прибиты вместе к дополнительным кольям, которые обычно изготавливаются из дерева и стали.При использовании деревянной опалубки стойки забиваются в подготовленное основание, а формующие плиты устанавливаются на надлежащий уровень или наклон с помощью выравнивающих устройств.
Нивелиры включают ручные нивелиры, лазерные нивелиры и струнные линии. Кроме того, для защиты участков, где одна доска стыкуется с другой, подрядчики используют дополнительные доски.
Плиты с более тонким поперечным сечением используются, когда возникает необходимость в скругленных краях, поворотах или даже произвольной форме. Бетон часто может прилипать к дереву, и чтобы решить эту проблему, деревянные доски регулярно покрывают низкосортным маслом или специальным антиадгезионным средством.
Предотвращение прилипания бетона к дереву имеет решающее значение по двум причинам. Это не только сохраняет опалубку в чистоте, но также позволяет подрядчикам использовать их несколько раз, прежде чем они будут выброшены.
Опалубка бетонных стен
Готовые формы для бетонных стен используются для заливки стен или более крупных конструкций, например, при строительстве опор или фундаментов зданий. Готовые стеновые системы обычно изготавливаются из искусственной древесины и укрепляются металлическим каркасом или состоят из полностью металлического корпуса.
Эти системы, иногда называемые системами формирования групп, предназначены для крепления и формирования единой конструкции с помощью системы защелок или штифтов. Кроме того, предварительно изготовленные стеновые системы также используют стяжку при удерживании арматурных стержней на месте внутри стеновой опалубки и для крепления одной секции к другой при заливке стен.
Готовые формы для стен доступны в широком диапазоне форм и размеров, и большинство производителей готовы изготавливать нестандартные размеры для конкретных проектов.
Изолированные бетонные формы (ICF)
Изолированная бетонная опалубка состоит из полого блока из изоляционных материалов, которые подходят друг к другу и заполняются бетоном, а затем армированы сталью.
СистемыICF построены с использованием фундаментной плиты, и система остается на месте, чтобы стать фундаментом и системой наружных стен. После размещения блока изоляционных материалов сеть из армированных металлом стержней помещается внутри конструкции блочной стены, и, наконец, в конструкцию блочной стены заливается смешанный с водой бетон или бетон «высокой осадки».
ICF чрезвычайно энергоэффективны, а сэндвич из пенобетона очень прочен, что делает его пригодным для использования в качестве стен, крыш и даже полов!
Опалубки из пенобетона и декоративные
Бетон превратился из строительного компонента в использование внутри дома, в декоративных бетонных столешницах и других декоративных сборных железобетонных изделиях. Рост популярности таких изделий привел к появлению новых инновационных методов формования бетона.
Эти нетрадиционные и нетрадиционные методы формования бетона обычно используются для создания отрицательных пространств или перевернутых форм, когда бетонная деталь обычно переливается вверх дном для достижения желаемого причудливого эффекта или текстурной отделки.
Декоративная пена для бетона обычно изготавливается из таких материалов, как меламин, ламинированная плита, акриловое стекло или крепится винтами к большой доске. Внутри форм часто используются особые вставки, которые создают декоративную окантовку или художественный рельеф.
Произошел резкий рост использования декоративных облицовок из-за роста числа муниципалитетов и штатов, стремящихся добавить к своим конкретным строительным проектам. Внутренняя часть формовочной системы крепится пластиковыми листами с рельефом из плитки, камня или художественного орнамента, что приводит к тому, что бетон принимает форму конструкции и, в конечном итоге, декоративную бетонную поверхность.
Типы бетонных форм | Networx
Бетонные формы похожи на чашу, удерживающую бетонный «суп» в зоне проекта — только суп весит тысячи фунтов, поэтому ему нужна серьезная чаша из толстого металла, дерева или пенопласта. Наиболее распространенными типами бетонных опалубок для жилых проектов являются опалубки из деревянных перекрытий, металлические конструкции для стен и фундамента, а также новые, более энергоэффективные изоляционные бетонные опалубки.Узнайте подробности о каждом типе.
Изготовление деревянных форм для перекрытияСтандартные бетонные террасы, тротуары или другие объекты просто имеют квадратную деревянную раму, которую можно удерживать в бетоне. Каркас, обычно брус 2х4, должен быть квадратным и ровным с внутренними размерами, равными размеру плиты.
После определения местоположения пиломатериалов забейте деревянные колья с внешней стороны каркаса. Столбы обычно также делаются из досок 2х4 и должны быть не менее одного фута в длину. Обрежьте один конец досок до острого края и вбейте их в земляное полотно примерно через каждые три фута, убедившись, что они поддерживают углы формы.
Прикрепите опалубочные доски к стойкам тяжелыми винтами, затем скрутите углы. Наконец, смажьте внутренние края досок растительным маслом или специальным маслом для форм, чтобы бетон не прилипал к доскам.
Существует несколько простых вариантов деревянной формы, в том числе фанерный каркас для бетонных ступенек или других более высоких проектов и изогнутые полосы ДВП, прикрепленные к внутренним углам каркаса для создания кривых.
Промышленные формыБетонные стены обычно заливают в промышленные формы. Формы обычно представляют собой искусственную деревянную поверхность между металлическим каркасом или цельные металлические листы на металлическом каркасе. Детали соединяются штифтами в защелках и имеют стержни, удерживающие листы друг от друга на одинаковой ширине.
Они должны быть выровнены и выровнены, с распорками, чтобы они оставались в вертикальном положении при заполнении бетоном. Как и плиты, металл или дерево необходимо покрыть формовочным маслом.После застывания бетона каждую форму снимают, а концы стержней отламывают.
Для экономных строителей изоляционные бетонные опалубки (ICF) заменяют съемные деревянные и металлические опалубки для стен. ICF изготовлены из жесткого пенопласта и остаются на месте после заливки и отверждения бетона. Легкие формы добавляют энергосберегающую изоляцию с обеих сторон стены со значениями изоляции от R-17 до R-26.Большинство стен с деревянным каркасом имеют изоляцию от R-13 до R-19.
ICF бывают самых разных форм и конфигураций, но стандартную конструкцию ICF сравнивают с блокированными игрушечными строительными блоками. Как и другие формы стен, у них есть металлические стержни, удерживающие стену на соответствующей ширине.
Вы хотите, чтобы бетон был укладкой профессионально? Найдите надежного подрядчика по бетону в вашем районе.
Стив Грэм пишет для networx. com.
Обновлено 27 марта 2018 г.
3 совета по получению наилучших результатов от бетонных форм — Accu-Krete
Бетон остается одним из самых популярных строительных материалов для жилых проектов, таких как новые внутренние дворики, подъездные пути или тротуары. Такая популярность может быть связана с невероятной прочностью бетона. Тем не менее, чтобы получить бетон, который прослужит так долго, как должен, каждый этап укладки должен быть выполнен правильно.
Один из самых важных этапов укладки бетона — это установка форм, которые придадут плите ее форму.Если вы хотите узнать больше о том, в чем разница между хорошей и плохой формой работы, читайте дальше. В этой статье будут описаны три важных фактора, которые подрядчик должен учитывать при установке бетонных форм.
1. Размеры деревянных досок Деревянные доски всегда использовались для изготовления бетонных опалубок. Однако подойдут не любые доски. Подрядчик должен тщательно учитывать размеры используемой древесины, иначе результаты могут не оправдать ожиданий. Если бетон вытечет из форм, это создаст огромный беспорядок, а также потенциально повлияет на прочность полученной плиты.
Что касается толщины, то для большинства конкретных проектов будет достаточно 2 дюймов. В конце концов, основные доски будут усилены серией столбов по внешней стороне. С другой стороны, длина доски должна быть адаптирована к размерам проекта, когда это возможно.
Многие подрядчики используют плиты, длина которых превышает длину плиты на несколько дюймов.Эта лишняя длина облегчает прикрепление перпендикулярных досок. Затем при желании выступающие края можно обрезать. Если размеры плиты превышают доступную длину доски, то несколько досок можно соединить вместе по длине с помощью зажимов.
Наконец, подрядчик должен учитывать высоту доски. В большинстве проектов используется один из двух распространенных размеров досок: 2 на 6 дюймов или 2 на 12 дюймов. Для большинства плит толщиной до 5 дюймов должно хватить 2 на 6 досок.
Однако, если подрядчик намеревается установить плиту с утолщенными краями, то потребуется 2 на 12 досок для размещения сверхглубокого бетона. Такие утолщенные края обеспечивают большую устойчивость, образуя защитную стену вокруг бетонного основания.
Сами по себе опалубочные плиты не смогли бы выдержать огромный вес влажного бетона. Чтобы они не гнулись, не сгибались и даже не разрушались, по периметру необходимо установить деревянные колья. Эти стойки укрепляют доски, придавая им устойчивость, необходимую для сохранения правильной формы после заливки бетона на место.
Подрядчик должен следить за соблюдением надлежащих расстояний между кольями. Столбы не должны находиться на расстоянии более 3 футов друг от друга. В случае особенно глубоких или больших плит подрядчики могут разместить стойки еще ближе друг к другу для дополнительной устойчивости.
3. Добавление ставок Даже с правильно расположенными ставками все может пойти не так. В зависимости от типа почвы колышек может просто не иметь устойчивости, чтобы выдерживать воздействие бетона на формы. Если кол выдвинется наружу хотя бы на дюйм или два, то формы будут выпирать, что приведет к деформации плиты.
Для обеспечения оптимальной устойчивости профессиональный подрядчик всегда прикрепляет стойки к опалубке. Саморезы служат для крепления гораздо лучше, чем гвозди. Если края бетонной плиты будут видны, важно, чтобы винт не проходил через форму полностью.
Высококачественная бетонная плита во многом обязана своей формой и стабильностью своим формам. Опытные подрядчики знают это и всегда следят за тем, чтобы их формы соответствовали самым высоким стандартам.Для получения дополнительной информации о том, что нужно для установки плиты, которая прослужит много лет, свяжитесь с нашими специалистами по бетону в Accu-Krete.
Как предотвратить прилипание бетона к дереву | Руководства по дому
Майком Мэтьюзом Обновлено 14 декабря 2018 г.
Специалисты в области строительства обычно используют фанерные панели в качестве формующих форм при заливке бетона для фундамента нового дома. Если деревянные формы были обработаны антиадгезивом, вы легко сможете их вытащить после высыхания бетона.При установке нового тротуара или патио мастер может залить бетон между формами 2 на 4, но для достижения наилучших результатов предварительно обработайте древесину так же, как это делают профессионалы.
Разделительные агенты на масляной основе
Когда-то профессионалы в области строительства создавали свои собственные разделительные агенты на масляной основе, используя такие материалы, как дизельное топливо, топочный мазут и минеральное масло, чтобы бетон не прилипал к дереву. Сегодняшние домостроители часто выбирают стойкую к прилипанию фанеру или панели OSB, предварительно обработанные на лесопилке запатентованными химическими смесями, которые могут включать парафин, минеральное масло и льняное масло.Некоторые подрядчики по бетону продлевают срок службы фанеры, устойчивой к прилипанию, с помощью нового покрытия из коммерческого антиадгезива или льняного масла, разбавленного растворителем.
Барьерные агенты на водной основе
Разделительные агенты на водной основе также могут препятствовать прилипанию бетона к древесным формам и, в отличие от формул на масляной основе, они делают это, не выделяя в воздух высокие уровни летучих органических соединений. Химические вещества, выделяющие ЛОС, строго регулируются в некоторых регионах, поскольку они способствуют образованию атмосферного смога.Коммерческие разделительные агенты на водной основе производятся из материалов растительного происхождения и с меньшей вероятностью обесцвечивают поверхность бетона. Обычные растительные масла могут служить той же цели, если наносятся в два или три последовательных слоя.
Реактивные разделительные агенты
Химически активные разделительные агенты вступают в реакцию со щелочностью бетона, предотвращая прилипание бетона к деревянным формам и формам. Коммерческие продукты этого типа состоят из жирной кислоты и мыльного поверхностно-активного вещества, которые химически реагируют с бетоном, помогая создать чистую, неокрашенную бетонную поверхность с гладкими краями. В то же время они создают свою собственную тонкую химическую мембрану, которая блокирует проникновение бетона в поры древесины.
Решения «Сделай сам»
Множество обычных бытовых товаров помогут предотвратить прилипание бетона к дереву. В большинстве случаев вы можете предотвратить прилипание бетона к форме, нанеся на дерево карнаубский воск, но только если температура превышает 50 градусов по Фаренгейту. В качестве другого домашнего решения нанесите на древесину два-три слоя домашнего минерального масла — первые слои служат в качестве герметика для древесины, а последний слой — в качестве смазки, но перед заливкой бетона сотрите излишки масла.
Бетонные формы — типы и выбор бетонных форм
🕑 Время чтения: 1 минута
Бетонные формы можно определить как твердый барьер, который помогает удерживать жидкий бетон на месте до тех пор, пока он не затвердеет и не приобретет определенную форму. Бетон принимает форму формы или формы, в которой он содержится.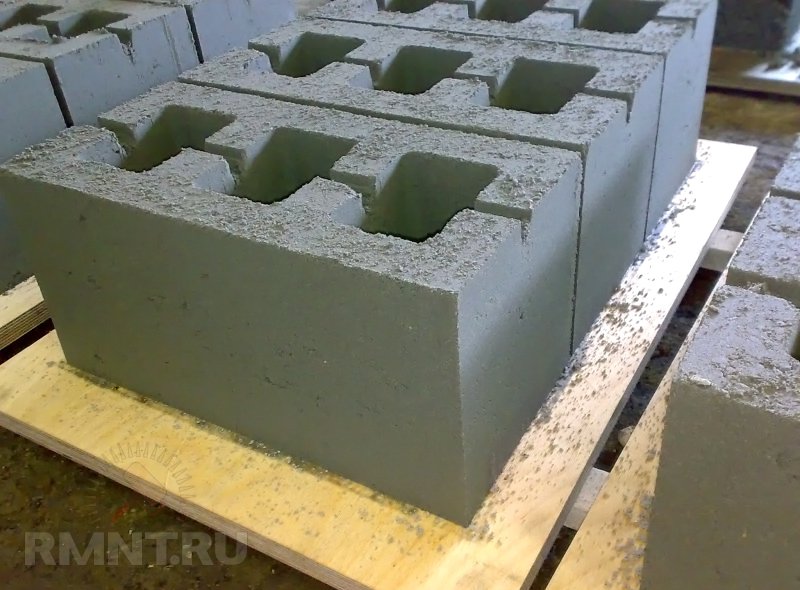
- Деревянные формы
- Изолированные бетонные опалубки
- Формы для пенобетона
- Формы бетонных стен
- Стальные формы
Рис.1. Опалубки деревянные бетонные; Изображение предоставлено: http://gatesconcreteforms.com
Рис.2. Изолированные бетонные опалубки (ICF)
Форма и бетон укладываются как бутерброд.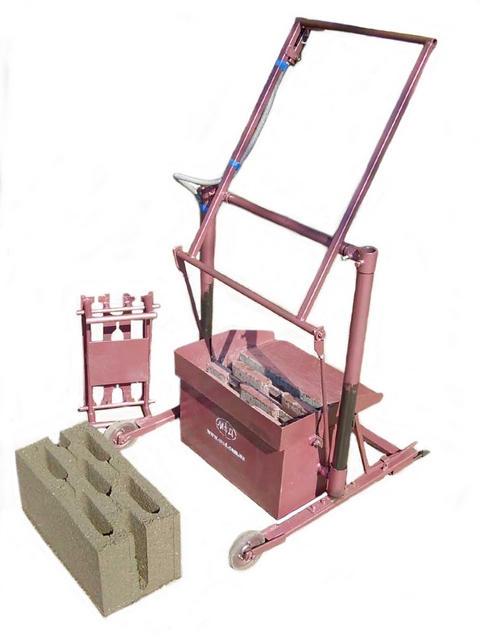
Рис. 3. Опалубки бетонных стен; Изображение предоставлено: igknighttec.com
Рис.4. Опалубки стальные бетонные; Изображение предоставлено: www.whartonhardware.com
Стальные опалубки не впитывают влагу из уложенного бетона, что снижает количество ошибок, наблюдаемых после снятия опалубки.Выбор бетонных форм
Принятие решения о выборе конкретных форм зависит от того, «где» и «как» используется система. Конкретная форма, выбранная для проекта, зависит от:- Размер заливки
- Давление на форму
- Масса бланка
- Тип уплотнения
- Количество оставшегося бетона
- Выбранные бетонные формы могут находиться в собственности или в аренде.
Стоимость владения и долгосрочного использования необходимо проанализировать перед покупкой. Если форму лучше взять напрокат, то выбирается тип формы, доступный и экономичный.
- Опыт работы с определенным типом формы влияет на выбор формы. Никаких производственных потерь не ожидается, если будет выбрана система форм, более знакомая рабочим. Без надлежащего обучения новой системе форм потери ожидаются.
- С точки зрения эстетики стальные формы обеспечивают чистую отделку с меньшим количеством отверстий для жучков на бетонной поверхности по сравнению с деревянными формами.
- С точки зрения допусков стальные формы являются лучшим выбором по сравнению с другими типами. Стальные формы обладают внутренней жесткостью и не впитывают влагу.
- Для конструкций с небольшой высотой лучше всего подходят деревянные формы. Для высоких форм высотой 20 футов стальные формы с дополнительными распорками и опорами являются лучшим выбором по сравнению с деревянными формами.
- Для заливки бетона с прямым, криволинейным или несколькими смещениями, а также с крутыми поворотами стальная форма является эффективным выбором. Если цена невысока, можно использовать тонкие деревянные формы.
Доска из формованного бетона | Жизнь архитектора
Подняв руки, кто не любит плиточный бетон? Кто-нибудь? Если ты хочешь быть моим другом, тебе лучше не поднимать руку.
Так что же такое «бетон из плит» и как сделать так, чтобы он выглядел наилучшим образом? Тебе повезло, потому что у меня есть ответы на эти вопросы.
Рисунок выше взят из одного из моих проектов и представляет собой крупный план текстуры, которую вы получаете с плиточным бетоном.Он выглядит действительно, действительно потрясающе (, если я сам так говорю… хотя на самом деле это не я построил).
«Бетон на плитах» — это название процесса формирования рисунка бетона, который оставляет изображение текстуры древесины на готовой поверхности бетона. Это метод строительства, который в наши дни используется все чаще, потому что бетон чрезвычайно хорошо подходит в качестве готового материала в современном дизайне, и, запечатлевая фактуру древесины на поверхности, он визуально смягчает и согревает несколько более прохладный вид бетона, оставаясь при этом. позволяя бетону выразить технику строительства.
Но как добиться такой отделки в ваших проектах? На самом деле довольно просто, просто спросите об этом, большинство конкретных подрядчиков, которых стоит нанять на работу, должны знать, о чем вы просите. Если это не так или если вы хотите, чтобы ваша доска из бетона выглядела так же хорошо, как на изображении выше, я расскажу вам, как мы это делаем.
Бесплатно!
Когда бетонные стены устанавливаются ( или заливаются, отливаются или устанавливаются… независимо от ), на месте сооружается опалубка, которая удерживает влажный бетон на месте до тех пор, пока он не затвердеет.Как правило, опалубка строится из листов фанеры, к которым прилегает влажный бетон, а затвердевающий (высыхающий) бетон принимает характер поверхности фанеры… мне кажется довольно простым. Когда вам нужен бетон из плит, вы берете ту же самую фанерную опалубку и добавляете дополнительный слой дерева на внутренние поверхности, чтобы влажный бетон приобрел этот новый узор. На картинке выше вы можете видеть, как бетонщики добавляют этот слой дерева к одной стороне опалубки.
Если вам нужен действительно красивый бетон, сделанный из досок, вы должны сделать это на ступеньку выше * БАМ! ( удар вашей опалубки с разворота!) Чтобы получить хорошее представление о процессе, который я использую, вам нужно кое-что узнать о том, как растут деревья.
Готовы?
Большинство из нас знает, что если вы посчитаете кольца дерева, вы можете определить, сколько лет дереву… или, по крайней мере, сколько ему было лет в то время, когда его срубили. Может быть, вы никогда особо не задумывались об этом, НО знаете ли вы, что темные кольца — это зимний рост, а более светлые кольца — летний рост? Поскольку в зимние месяцы деревья обычно растут медленнее, древесные клетки более плотные и кажутся более темными, чем более быстрорастущие, более свободно расположенные летние годичные кольца. Разница между этими кольцами заключается в узоре, который вы видите на формованном бетоне.
Но подождите … станет еще лучше!
Чтобы действительно подчеркнуть эти узоры — это то, что мы делаем. Мы берем 2 сосны еловой пихты (толщиной 1 1/2 дюйма) и разрезаем ее посередине, так что теперь у нас есть две части 3/4 дюйма. Этот процесс помогает устранить следы инструментов в процессе изготовления, а также все вмятины и вмятины, которые могут появиться на досках только в процессе обработки.Потом …. мы производим пескоструйную обработку поверхности.
Что?!?
Вы меня правильно услышали (прочитали). Мы обрабатываем пескоструйную обработку только что разрезанной еловой пихты. Вот что делает парень в зеленом костюме HazMat на фотографиях выше и ниже.
А зачем мы это делаем?
Пескоструйной обработкой поверхности мы подчеркиваем разницу между быстрорастущей (мягкой) летней древесиной и медленнорастущей (твердой) зимой.
Пескоструйная обработка удаляет мягкие части древесины быстрее, чем твердые, поэтому при пескоструйной обработке поверхность рисунок древесины становится более выраженным, а не таким тонким и неравномерным, как если бы мы просто выложили нашу опалубку досками из кедра 3/4 дюйма. Кроме того, горизонтальная линия, которую вы видите на изображении выше, показывает место соединения плит еловой сосны и ели, и бетон немного просачивается в щель.
Горизонтальный узор из расположения досок был оставлен более выраженным на картинке выше — это было в проекте, над которым я работал, и который был завершен несколько лет назад.
Итак, сколько вы можете ожидать от этой милой мелочи, чтобы добавить к вашему проекту? (Вы сидите?) Если вы живете в районе Северного Техаса, вам нужно будет дополнительно внести в бюджет 20 долларов за квадратный фут в дополнение к стоимости бетонной стены, чтобы покрыть расходы на получение древесины, разрезать его пополам, обработать поверхность пескоструйным аппаратом, а затем покрыть внутренние поверхности фанерной опалубки.
Нет сомнений в том, что вы могли бы выполнить эту деталь с меньшими затратами — вы могли бы просто выровнять опалубку с досками забора … но это не будет выглядеть так хорошо, как изображения, которые вы видите выше. Это не для каждого проекта или бюджета, и за последние 6 лет я использовал это лечение только дважды. Но если вы рассудительно подходите к дизайну и тщательно обдумываете, как использовать это средство для достижения максимального эффекта, я думаю, что почти в любом проекте найдется место для этой детали.
Ура и счастливой пескоструйной обработки!
Профиль стажёра-архитектора — Часть перваяЕще лучше из «Жизни архитектора»
повторно использовать древесину из бетонной формы?
повторно использовать древесину из бетонной формы? — Обмен стеками товаров для домаСеть обмена стеков
Сеть Stack Exchange состоит из 177 сообществ вопросов и ответов, включая Stack Overflow, крупнейшее и пользующееся наибольшим доверием онлайн-сообщество, где разработчики могут учиться, делиться своими знаниями и строить свою карьеру.
- 0
- +0
- Авторизоваться Зарегистрироваться
Home Improvement Stack Exchange — это сайт вопросов и ответов для подрядчиков и серьезных домашних мастеров.Регистрация займет всего минуту.
Зарегистрируйтесь, чтобы присоединиться к этому сообществуКто угодно может задать вопрос
Кто угодно может ответить
Лучшие ответы голосуются и поднимаются наверх
Спросил
Просмотрено 7к раз
Я стараюсь не тратить впустую материалы везде, где это возможно, и методы «один раз использовать, а затем выбросить» особенно утомительны. Итак, какие у вас есть предложения по повторному использованию пиломатериалов, используемых для изготовления бетонных форм?
Создан 29 июл.
Мэтт Уилки46722 золотых знака66 серебряных знаков1616 бронзовых знаков
Если вы снова воспользуетесь им для формы, не проблема.. . в противном случае остатки бетона на дереве повредят ваши электроинструменты.
Создан 29 июл.
Toosheltooshel1,935 33 золотых знака1313 серебряных знаков1919 бронзовых знаков
По совету друга, который раньше преподавал столярное дело, мы покрасили доски легким слоем масла перед тем, как строить формы. Когда мы разбивали формы, налипшего бетона было мало, примерно 10% покрытия. Я позволил доскам полностью высохнуть, затем встряхнул их молотком, позаботившись еще о% 5 или около того. После этого ленточная шлифовальная машина с крупнозернистой бумагой удалила остатки бетона и масляные пятна.
Конечный результат — доски, которые, хотя и не так хороши, как новые, подходят для большинства применений (могут быть не окрашены) и безопасны для электроинструментов. Мы используем их для балок нашего настила.
Создан 04 авг.
Мэтт Уилки46722 золотых знака66 серебряных знаков1616 бронзовых знаков
Любой, кто когда-либо наблюдал за возведением бетонного небоскреба в Нью-Йорке, знает, что деревянные формы можно использовать снова и снова.Обычно у них есть два полных набора форм, один из которых используется для бетонной конструкции на этажах с нечетными номерами, а другой — для этажей с четными номерами. Пока бетон застывает, скажем, на полу 17, они снимают формы с этажа 16 и поднимают их, чтобы использовать пол 18.
Создан 08 авг.
Джоэл Спольски ♦ Джоэл Спольски1,9959 золотых знаков1919 серебряных знаков2828 бронзовых знаков
Я бы сохранил его для повторного использования в качестве формы, или для крепления, или для другого одноразового использования.
Создан 29 июля ’10 в 20: 422010-07-29 20:42
афория2,13022 золотых знака1717 серебряных знаков1818 бронзовых знаков
В зависимости от того, как вы его установите, вы можете построить раму на внутри фанерных форм так, чтобы распорка находилась заподлицо с бетоном.Это позволяет оставить их на месте и использовать вместо полос обшивки для крепления изоляции, сайдинга и т. Д. Или вы можете установить их так, чтобы они не были заподлицо, чтобы вы могли использовать пространство для дополнительной изоляции. Эти методы имеют дополнительное преимущество, так как не требуют сверления отверстий или использования бетонных гвоздей и т. Д., Которые ослабляют структуру. После того, как вы удалите фанеру снаружи, вы можете удалить большую часть бетона с помощью большой лопаты и повторно использовать их для настила пола или крыши.
Создан 10 мар.
Повторное использование для форм. Пиломатериалы в любом случае дешевы, так что купите себе новый кусок, если вы снова хотите использовать тот же самый сорт дерева.
Создан 05 авг.
Инженер2021Инженер20213,1691010 золотых знаков2525 серебряных знаков4343 бронзовых знака
Не тот ответ, который вы ищете? Посмотрите другие вопросы с метками бетон, дерево или задайте свой вопрос.
Обмен стеклами товаров для дома лучше всего работает с включенным JavaScriptВаша конфиденциальность
Нажимая «Принять все файлы cookie», вы соглашаетесь, что Stack Exchange может хранить файлы cookie на вашем устройстве и раскрывать информацию в соответствии с нашей Политикой в отношении файлов cookie.