Металлы — Википедия
О соответствующем направлении рок-музыки см. Метал.Мета́ллы (от лат. metallum — шахта, рудник) — группа элементов в виде простых веществ, обладающих характерными металлическими свойствами, такими, как высокие тепло- и электропроводность, положительный температурный коэффициент сопротивления, высокая пластичность, ковкость и металлический блеск.
Из 118 химических элементов, открытых на 2019 год, к металлам часто относят (единого общепринятого определения нет, например, полуметаллы и полупроводники не всегда относят к металлам):
6 элементов в группе щелочных металлов: Li, Na, K, Rb, Cs, Fr;
4 в группе щёлочноземельных металлов: Ca, Sr, Ba, Ra; к щёлочноземельным также иногда относят Mg, и Be;
38 в группе переходных металлов:
— Sc, Ti, V, Cr, Mn, Fe, Co, Ni, Cu, Zn;
— Y, Zr, Nb, Mo, Tc, Ru, Rh, Pd, Ag, Cd;
— Hf, Ta, W, Re, Os, Ir, Pt, Au, Hg;
— Rf, Db, Sg, Bh, Hs, Mt, Ds, Rg, Cn;
7 в группе лёгких металлов: Al, Ga, In, Sn, Tl, Pb, Bi;
7 в группе полуметаллов[1]: B, Si, Ge, As, Sb, Te, Po;
14 в группе лантаноиды + лантан (La):
Ce, Pr, Nd, Pm, Sm, Eu, Gd, Tb, Dy, Ho, Er, Tm, Yb, Lu;
14 в группе актиноиды (физические свойства изучены не у всех элементов) + актиний (Ac):
Th, Pa, U, Np, Pu, Am, Cm, Bk, Cf, Es, Fm, Md, No, Lr.
Также металлическими свойствами может обладать водород[2][3].
Таким образом, к металлам могут относится более 90 элементов из всех открытых.
В астрофизике термин «металл» может иметь другое значение и обозначать все химические элементы тяжелее гелия (см. Металличность).
Кроме того, в физике металлам, как проводникам, противопоставляется полупроводники и диэлектрики (см. также
Некоторые группы/семейства металлов[править | править код]
- Щелочные:
- Щёлочноземельные:
- Другие (которые зачастую не совсем правильно относят к щёлочноземельным):
- Переходные:
- Постпереходные:
- Тугоплавкие
- Металлы платиновой группы
- Цветные
- Благородные
- Монетные
Аморфные металлы[править | править код]
Слово «металл» заимствовано из немецкого языка. Отмечается в «Травнике» Николая Любчанина, написанном в 1534 году: «…злато и серебро всех металей одолеваетъ». Окончательно усвоено в Петровскую эпоху. Первоначально имело общее значение «минерал, руда, металл»; разграничение этих понятий произошло в эпоху М. В. Ломоносова
Металлом называется светлое тело, которое ковать можно. Таких тел находим только шесть: золото, серебро, медь, олово, железо и свинец. Разделяются на высокие и простые металлы; которое разнство в том состоит, что высоких одним огнём без помощи других материй в пепел сожечь не можно, а напротив того простые через едину онаго силу в пепел обращаются. … За полуметаллы почитаются мышьяк, сурьма, висмут, цинк и ртуть.М. В. Ломоносов |
Немецкое слово «metall» заимствовано из латинского языка, где «metallum
Бо́льшая часть металлов присутствует в природе в виде руд и соединений. Они образуют оксиды, сульфиды, карбонаты и другие химические соединения. Для получения чистых металлов и дальнейшего их применения необходимо выделить их из руд и провести очистку. При необходимости проводят легирование и другую обработку металлов. Изучением этого занимается наука металлургия. Металлургия различает руды чёрных металлов (на основе железа) и цветных (в их состав не входит железо, всего около 70 химических элементов). Золото, серебро и платина относятся также к драгоценным (благородным) металлам
Известно, что организм человека на 3 % состоит из металлов[7]. Больше всего в организме кальция (в костях) и натрия, выступающего в роли электролита в межклеточной жидкости и цитоплазме. Магний накапливается в мышцах и нервной системе, медь — в печени, железо — в крови.
Подготовка руды
Металлы извлекают из земли в процессе добычи полезных ископаемых. Добытые руды служат относительно богатым источником необходимых элементов. Для выяснения нахождения руд в земной коре используются специальные поисковые методы, включающие разведку и исследование рудных месторождений. Месторождения руд разрабатываются открытым или карьерным способом и подземным или шахтным способом. Иногда применяется комбинированный (открыто-подземный) способ разработки рудных месторождений.
После извлечения руд они, как правило, подвергаются обогащению. При этом из исходного минерального сырья выделяют один или несколько полезных компонентов — рудный концентрат(ы), промпродукты и отвальные хвосты. В процессах обогащения используют отличия минералов полезного компонента и пустой породы в плотности, магнитной восприимчивости, смачиваемости, электропроводности, крупности, форме зёрен, химических свойствах и др.
Работа с рудой
Из добытой и обогащённой руды металлы извлекаются, как правило, с помощью химического или электролитического восстановления. В пирометаллургии для преобразования руды в металлическое сырьё используются высокие температуры, в гидрометаллургии применяют для тех же целей водную химию. Используемые методы зависят от вида металла и типа загрязнения.
Когда металлическая руда является ионным соединением металла и неметалла, для извлечения чистого металла она обычно подвергается выплавлению — нагреву с восстановителем. Многие распространённые металлы, такие как железо, медь, олово, плавят с использованием углерода в качестве восстановителя. Некоторые металлы, такие как алюминий и натрий, не имеют ни одного экономически оправданного восстановителя и извлекаются с применением электролиза.
Сульфидные руды не улучшаются непосредственно до получения чистого металла, но обжигаются на воздухе, с целью преобразования их в окислы.
Твёрдость[править | править код]
Все металлы (кроме ртути и, условно, франция) при нормальных условиях находятся в твёрдом состоянии, однако обладают различной твёрдостью. Ниже в таблице приводится твёрдость некоторых металлов по шкале Мооса.
Температура плавления[править | править код]
Температуры плавления чистых металлов лежат в диапазоне от −39 °C (ртуть) до 3410 °C (вольфрам). Температура плавления большинства металлов (за исключением щелочных) высока, однако некоторые металлы, например, олово и свинец, могут расплавиться на обычной электрической или газовой плите.
Плотность[править | править код]
В зависимости от плотности, металлы делят на лёгкие (плотность 0,53 ÷ 5 г/см³) и тяжёлые (5 ÷ 22,5 г/см³). Самым лёгким металлом является литий (плотность 0,53 г/см³). Самый тяжёлый металл в настоящее время назвать невозможно, так как плотности осмия и иридия — двух самых тяжёлых металлов — почти равны (около 22,6 г/см³ — ровно в два раза выше плотности свинца), а вычислить их точную плотность крайне сложно: для этого нужно полностью очистить металлы, ведь любые примеси снижают их плотность.
Пластичность[править | править код]
Большинство металлов пластичны, то есть металлическую проволоку можно согнуть, и она не сломается. Это происходит из-за смещения слоёв атомов металлов без разрыва связи между ними. Самыми пластичными являются золото, серебро и медь. Из золота можно изготовить фольгу толщиной 0,003 мм, которую используют для золочения изделий. Однако не все металлы пластичны. Проволока из цинка или олова хрустит при сгибании; марганец и висмут при деформации вообще почти не сгибаются, а сразу ломаются. Пластичность зависит и от чистоты металла; так, очень чистый хром весьма пластичен, но, загрязнённый даже незначительными примесями, становится хрупким и более твёрдым. Некоторые металлы, такие, как золото, серебро, свинец, алюминий, осмий, могут срастаться между собой, но на это могут уйти десятки лет.
Электропроводность[править | править код]
Все металлы хорошо проводят электрический ток; это обусловлено наличием в их кристаллических решётках подвижных электронов, перемещающихся под действием электрического поля. Серебро, медь и алюминий имеют наибольшую электропроводность; по этой причине последние два металла чаще всего используют в качестве материала для проводов. Очень высокую электропроводность имеет также натрий, в экспериментальной аппаратуре известны попытки применения натриевых токопроводов в форме тонкостенных труб из нержавеющей стали, заполненных натрием. Благодаря малому удельному весу натрия, при равном сопротивлении натриевые «провода» получаются значительно легче медных и даже несколько легче алюминиевых.
Теплопроводность[править | править код]
Высокая теплопроводность металлов также зависит от подвижности свободных электронов. Поэтому ряд теплопроводностей похож на ряд электропроводностей, и лучшим проводником тепла, как и электричества, является серебро. Натрий также находит применение как хороший проводник тепла; широко известно, например, применение натрия в клапанах автомобильных двигателей для улучшения их охлаждения.
Наименьшая теплопроводность — у висмута и ртути.
Цвет[править | править код]
Цвет у большинства металлов примерно одинаковый — светло-серый с голубоватым оттенком. Золото, медь и цезий соответственно жёлтого, красного и светло-жёлтого цвета.
Взаимодействие с простыми веществами[править | править код]
На внешнем электронном уровне у большинства металлов небольшое количество электронов (1-3), поэтому они в большинстве реакций выступают как восстановители (то есть «отдают» свои электроны).
Реакции с простыми веществами
- С кислородом реагируют все металлы, кроме золота и платиновых металлов. Реакция с серебром происходит при высоких температурах, но оксид серебра(II) практически не образуется, так как он термически неустойчив. В зависимости от металла на выходе могут оказаться оксиды, пероксиды, надпероксиды:
- 4Li+O2=2Li2O{\displaystyle {\mathsf {4Li+O_{2}=2Li_{2}O}}} оксид лития
- 2Na+O2=Na2O2{\displaystyle {\mathsf {2Na+O_{2}=Na_{2}O_{2}}}} пероксид натрия
- K+O2=KO2{\displaystyle {\mathsf {K+O_{2}=KO_{2}}}} надпероксид калия
Чтобы получить из пероксида оксид, пероксид восстанавливают металлом:
- Na2O2+2Na=2Na2O{\displaystyle {\mathsf {Na_{2}O_{2}+2Na=2Na_{2}O}}}
Со средними и малоактивными металлами реакция происходит при нагревании:
- 3Fe+2O2=Fe3O4{\displaystyle {\mathsf {3Fe+2O_{2}=Fe_{3}O_{4}}}}
- 2Hg+O2=2HgO{\displaystyle {\mathsf {2Hg+O_{2}=2HgO}}}
- 2Cu+O2=2CuO{\displaystyle {\mathsf {2Cu+O_{2}=2CuO}}}
- С азотом реагируют только самые активные металлы, при комнатной температуре взаимодействует только литий, образуя нитриды:
- 6Li+N2=2Li3N{\displaystyle {\mathsf {6Li+N_{2}=2Li_{3}N}}}
При нагревании:
- 2Al+N2=2AlN{\displaystyle {\mathsf {2Al+N_{2}=2AlN}}}
- 3Ca+N2=Ca3N2{\displaystyle {\mathsf {3Ca+N_{2}=Ca_{3}N_{2}}}}
- С серой реагируют все металлы, кроме золота и платины.
Железо взаимодействует с серой при нагревании, образуя сульфид:
- Fe+S=FeS{\displaystyle {\mathsf {Fe+S=FeS}}}
- С водородом реагируют только самые активные металлы, то есть металлы IA и IIA групп, кроме Be. Реакции осуществляются при нагревании, при этом образуются гидриды. В реакциях металл выступает как восстановитель, степень окисления водорода −1:
- 2Na+h3=2NaH{\displaystyle {\mathsf {2Na+H_{2}=2NaH}}}
- Mg+h3=Mgh3{\displaystyle {\mathsf {Mg+H_{2}=MgH_{2}}}}
- С углеродом реагируют только наиболее активные металлы. При этом образуются ацетилениды или метаниды. Ацетилениды при взаимодействии с водой дают ацетилен, метаниды — метан.
- 2Na+2C=Na2C2{\displaystyle {\mathsf {2Na+2C=Na_{2}C_{2}}}}
- Na2C2+2h3O=2NaOH+C2h3{\displaystyle {\mathsf {Na_{2}C_{2}+2H_{2}O=2NaOH+C_{2}H_{2}}}}
С кислотами металлы реагируют по-разному. Металлы, стоящие в электрохимическом ряду активности металлов (ЭРАМ) до водорода, взаимодействуют практически со всеми кислотами.
Взаимодействие неокисляющих кислот с металлами, стоящими в электрическом ряду активности металлов до водорода[править | править код]
Происходит реакция замещения, которая также является окислительно-восстановительной:
- Mg+2HCl=MgCl2+h3↑{\displaystyle {\mathsf {Mg+2HCl=MgCl_{2}+H_{2}\uparrow }}}
- 2Al+2h4PO4=2AlPO4+3h3↑{\displaystyle {\mathsf {2Al+2H_{3}PO_{4}=2AlPO_{4}+3H_{2}\uparrow }}}
Взаимодействие концентрированной серной кислоты H2SO4 с металлами[править | править код]
Окисляющие кислоты могут взаимодействовать и с металлами, стоящими в ЭРАМ после водорода:
- Cu+2h3SO4=CuSO4+SO2↑+2h3O{\displaystyle {\mathsf {Cu+2H_{2}SO_{4}=CuSO_{4}+SO_{2}\uparrow +2H_{2}O}}}
ru.wikipedia.org
Жесть — Википедия
Способ загиба жести Ножницы по металлу Жестяная кровля и водостокЖесть — холоднокатаная отожжённая листовая сталь толщиной 0,10—0,36 мм (по ГОСТ Р 52204-2004) с нанесёнными защитными покрытиями из олова или специальными покрытиями, напр. лаком, цинком, хромом и другими. Выпускается в листах размерами 512—1000 × 712—1200 мм или в рулонах шириной до 1 м, массой до 15 тонн.
Наибольшее распространение в мире имеет жесть, покрытая слоем олова (белая, или лужёная, жесть). По способу нанесения защитного слоя она подразделяется на горячелужёную жесть (со слоем оловянного покрытия толщиной 1,6-2,5 мкм) и жесть, лужёную методом электролитического осаждения (со слоем олова толщиной 0,34-1,56 мкм).
Жесть без защитного покрытия из олова называется нелужёной, или чёрной.
Первоначально процесс производства жести был достаточно трудоемким. Листы чёрной (нелуженой) жести размерами 1×1 м и толщиной около 2 мм изготавливались ручным способом, с помощью кузнечных молотов, после чего готовые листы подвергали травлению в бочках с молочной кислотой, которую получали в результате брожения ржаной муки. После травления листы чёрной жести сортировали и подвергали лужению в ёмкостях, для чего использовалось три ванны, в которые поочередно опускали рамы с готовыми листами жести (до 20 штук на раме), после чего вытаскивали их клещами и опускали в холодную воду для остывания. Между операциями лужения листы чёрной жести смазывали салом. В каждую ванну добавляли 600—700 килограммов жидкого олова с добавлением меди (в пропорции 1:70). Данная пропорция была необходима по причине того, что при большем добавлении меди поверхность жести становилась тусклой.
После завершения процесса лужения готовую жесть вручную полировали паклей и смесью из опилок, мела и отрубей до блеска, после чего листы жести отправлялись на упаковку и дальнейшую продажу.
Исторически наиболее известными центрами по производству луженой жести были немецкие города Вунзидель, Нюрнберг и Амберг, однако существует версия, в соответствии с которой первое промышленное производство белой жести было налажено в земле Пфальц, входившей в то время в состав Австрийской империи.
По мнению М. Р. Фасмера (Этимологический словарь русского языка. — М.: Прогресс М. Р. Фасмер 1964—1973) название заимствовано из тюркских языков или монгольского языка: ср. казах. ǯez «желтая медь, жесть», тат. ǯiz «желтая медь», чагат.. алт., тел. čas «жесть, бронза», кыпч. jäz «желтая медь», алт., тел., леб. jäs «медь», бар. jis (Радлов 3, 376, 528, 1909; 4, 85, 154), также монг. ǯes «медь, латунь», калм. zes — то же (Корш, Акад. Слов. 2, 403; ИОРЯС 8, 4, 34; Рамстедт, KWb. 473; Преобр. I, 231)[1]. В Казахстане имеется город с названием Жезказган (в советский период Джезказган), название которого происходит от слов Жез (медь) и казган (выкопано). В окрестностях города добывается медь, свинец, цинк и другие цветные металлы.
Первоначально производство жести было секретом (подобно производству фарфора), которым на протяжении около 300 лет владели лишь Австрия и Германия.
Однако в 1665 г. секрет изготовления белой жести был украден англичанами, которые постепенно стали перехватывать лидерство у немцев не только перенимая их опыт, но и создавая собственные технологии по производству.
В 1720 году в Уэльсе были построены несколько заводов по изготовлению жести, которые использовали для производства горячекатаные листы металла, а также усовершенствованные процессы травления и лужения, что позволило англичанам захватить рынок и занять место лидера по производству с центром в Уэльсе.
Жесть в качестве материала для консервных банок[править | править код]
Своему успешному продвижению в мире жесть обязана созданию консервной банки. После объявления Наполеоном I награды в 12000 франков за метод консервирования продуктов для французской армии, которую получил француз Николя Аппер, коммерсант из Манчестера Пьер Дюран в 1810 году впервые запатентовал идею использования жестяных банок для консервирования. Уже через два года, в Лондоне, двумя инженерами, Джоном Холлом и Брайаном Донкином (который также является изобретателем станка по производству бумаги), была открыта первая в мире фабрика по производству консервных банок, жесть для которых они покупали на заводе в графстве Вустершир.
Корпуса банок того времени изготавливались из прямоугольных листов жести, спаянных по шву, который находился на внутренней стороне банки. Дно банки также припаивалось к стенкам. Если в банке находился твердый продукт (например, мясо), то крышку припаивали после его загрузки в банку, если жидкость (например, сок), то банку спаивали полностью, оставляя лишь отверстие на верхней крышке, через которую заливали жидкость. Отверстие, по окончании процесса, также запаивали. Для открытия таких банок из жести того времени требовалась немалая сила и инструменты, в частности зубило. Кроме того, такие банки были дорогими, так как опытный рабочий мог изготовить не более 5-6 банок в час.
Однако данный факт не мог помешать распространению жести в качестве материала. В связи с быстрым развитием консервной промышленности (в частности в США, как основного производителя говядины того времени) во второй половине XIX века стремительно происходили изменения в конструкции и производстве банок. Этому способствовал запатентованный в 1856 году Генри Бессемером конвертер для передела жидкого чугуна в сталь продувкой воздухом без расхода горючего, что удешевило производство стали. Также немалую роль в расширении производства жести сыграл американский коммерсант Гейл Борден, открывший в 1858 году первый завод по производству сгущённого молока. В 1890 годах в Англии появляется первая, полностью автоматизированная система по производству банок из жести, которая изготавливала до 6000 банок в час, а также машины для механического лужения, что позволило уменьшить зависимость от ручного труда и удешевить производство банок, что способствовало увеличению производства жести в мире.
Жесть под гибочным прессомВ первой половине XX века была разработана система непрерывной прокатки стальной ленты. Кроме того, в 1915 году появились технологии электролитического лужения. В 1930 году в Германии было налажено промышленное производство белой жести способом электролитического лужения холоднокатаной стальной ленты. Также распространению способа электролитического лужения поспособствовала Вторая мировая война, вызвавшая перебои с поставками олова. В 1943 году в США также было налажено производство жести методом электролитического лужения и уже через пять лет половина всей белой жести, производившейся в США, изготавливалась этим способом. В последующие тридцать лет оборудование для горячего лужения жести практически повсеместно было вытеснено электролитическими линиями. В дальнейшем для производства жести были внедрены другие технические разработки, такие как непрерывный отжиг, двойная прокатка холоднокатаной стальной ленты и использование дифференциальных (разнотолщинных или разноматериальных) покрытий, что позволило к 1980 году производить более 13 000 000 тонн жести в 37 странах мира.
В настоящее время производство белой жести является одним из основных потребителей олова (до 30 % от общего употребления).
Современная технология производства белой жести[править | править код]
В России основным документом при производстве жести является ГОСТ Р 52204-2004 «Жесть холоднокатаная чёрная и белая». [1] Иногда можно встретить ссылки на старый советский ГОСТ 13345-85 «Жесть». [2]
В настоящее время технология производства белой жести включает в себя следующие процессы:
- выплавка стали заданного химического состава,
- горячая прокатка
- холодная прокатка
- отжиг (непрерывный или в колпаковых печах),
- правка
- нанесение оловянного или хромового покрытия,
- пассивация,
- промасливание,
- резка листов заданных размеров,
- упаковка готовой продукции.
Белая жесть — чёрная жесть с двухсторонним покрытием оловом, нанесенным методом горячего (жесть ГЖК) и электролитического (жесть ЭЖК) лужения. В зависимости от соотношения толщины покрытия по сторонам, данная жесть производится с одинаковой или дифференцированной толщиной покрытия.
Белая жесть представляет из себя тонкий, холоднокатанный низкоуглеродистый стальной лист или ленту, покрытую с обеих сторон чистым оловом. Таким образом, она объединяет в себе прочность и пластичность стали, а также коррозионную стойкость, способность к лужению и привлекательный вид олова.
Производство стальной основы и её последующее покрытие оловом являются независимыми друг от друга процессами, так что сталь с любым набором свойств теоретически сочетается с любым возможным покрытием оловом.
Состав стали, используемой для производства жести, строго контролируется. В зависимости от выбранной марки стали и способа обработки могут быть получены различные типы жести с различной пластичностью. В производстве чаще используется белая жесть с диапазоном толщин от 0,13 мм до 0,5 мм.
Жесть может быть покрыта слоем олова различной толщины, и даже каждая сторона жести может быть покрыта слоем олова различной толщины (дифференциальное покрытие) в зависимости от требований, предъявляемых к внутренней и наружной поверхности основной конечной продукции — жестяной банке. Разнообразную отделку поверхности жести производят для различных применений. Белая жесть подвергается специальному режиму пассивации для стабилизации поверхности и улучшения её адгезии к лакам. Она также покрывается очень тонким слоем масла, чтобы улучшить возможность её обработки. Это масло, безусловно, совместимо с пищевыми продуктами.
В процессе производства, в зависимости от качественных характеристик, белая жесть разделяется на марки:
- ЭЖК — жесть электролитического лужения консервная
- ЭЖР — жесть электролитического лужения разного назначения
- ЭЖОН — жесть электролитического лужения общего назначения
- ГЖК — жесть горячего лужения консервная
- ГЖР — жесть горячего лужения разного назначения.
Белая жесть выпускается в рулонах и листах в соответствии со стандартами ГОСТ 13345-85 (СССР), ГОСТ Р 52204-2004 (Россия) и EN 10202:2001 (Европейский Союз). [3]
Жесть консервная (пищевая) — жесть для производства тары под пищевые продукты и укупорочных изделий (крышки для закатывания, легковскрываемые крышки и пр.).
Консервная (пищевая) жесть производится из чёрной жести путём нанесения двухсторонних покрытий. При нанесении оловянного покрытия получается жесть ЭЖК или ГЖК (электролитическое или горячее лужение соответственно). При нанесении электролитического покрытия хрома или оксидов хрома получается жесть ECCS (по европейской классификации). Такая жесть требует обязательного высококачественного лакирования. В России хромированная лакированная жесть выпускается под маркой ХЛЖК.
Чёрная жесть — тонколистовая (0,1-0,5 мм) холоднокатаная сталь без защитного покрытия. Изготавливается из сталей марок 08кп, 08пс, 10кп,10пс с химическим составом по ГОСТ 1050. Используется в основном в электротехнической промышленности и машиностроении. Выпускается в рулонах и листах.
Жесть однократной прокатки — полоса из нелегированной малоуглеродистой стали, прокатанная способом холодной прокатки до требуемой толщины, отожженная и дрессированная, которая используется как самостоятельный материал или же для последующего нанесения защитного покрытия. Термин распространяется на чёрную и белую жесть в рулонах и листах.
Жесть двукратной прокатки. В настоящее время во всем мире большое количество консервной жести изготовляется способом двойной прокатки. Чем тоньше и прочней производится белая жесть, тем более эффективно осуществляется использование материала в производстве жестяных банок. После первой холодной прокатки и отжига, вместо дрессировки, стальной лист подвергается второй холодной прокатке с использованием смазки, при этом толщина уменьшается на 10-50 %. В процессе прокатки проявляется эффект упрочнения стального листа, при этом сохраняется значительная пластичность, достаточная для изготовления концов и корпусов банок. Окончательная минимальная толщина составляет 0,12 мм, обычный диапазон толщин 0,14 — 0,24 мм. В стали двойной прокатки отчетливо проявлется анизотропия механических свойств, поэтому при заказе и использовании такой жести всегда следует указывать и принимать в расчет направление прокатки.(Например, сворачивание бланков при изготовлении сварной банки должно осуществляться вдоль направления прокатки.
В России жесть двойной прокатки пока не производится, хотя опытные партии такой жести уже выпускались в 2009 году.
Лакированная жесть. Лакировка и литографирование белой жести осуществляется для защиты внутренней и наружной поверхности и улучшения внешнего вида консервной тары, что значительно повышает её конкурентоспособность. Наносят лаковые покрытия на автоматическом оборудовании. Метод нанесения покрытий на листы осуществляет посредством валков. Листы жести покрываются лаками и проходят через сушильные печи. Пары растворителей, выделяющиеся при отвердевании лаков, дожигаются при высокой температуре в специальных установках. Современные литографические машины позволяют окрашивать жесть в любые цвета. Печать на металлических листах (литографирование) осуществляется офсетным способом, используются краски, отвердевающие в сушильных печах при высокой температуре. Полноцветная печать фотографического качества с учетом нанесения покровных лаков требует до 9 листопрогонов. Существуют линии печати конвенциональными красками и в последнее время широкое распространение получили линии печати УФ-красками. Печать с помощью красок с отвердением под воздействием ультрафиолетового облучения имеет много преимуществ по сравнению с традиционным способом: экономия площади, экономия времени, экономия красок, более высокая скорость печати (до 10 000 листов в час).
У этой технологии есть также и негативные стороны: требования к условиям производства значительно выше (температура и влажность в помещении), краски стоят значительно дороже своих конвенциональных аналогов и срок их хранения короче, выбор поставщиков ультрафиолетовых красок значительно уже, адгезия к металлу хуже, что приводит к отслаиванию краски при сильной деформации жести в дальнейшем.
Лакированная жесть регулируется российским стандартом о технических требованиях к жести белой в листах, лакированной ОСТ 10 138-88
Характеристики и марки выпускаемой российской промышленностью жести[править | править код]
- Жесть ЭЖК — белая консервная жесть электролитического лужения (ГОСТ 13345-85,ГОСТ Р 52204-2004,СТП ЭПК-04-2010)
- Жесть ГЖК — белая консервная жесть горячего лужения (ГОСТ 13345-85,ГОСТ Р 52204-2004)
- Жесть ЭЖР — белая жесть электролитического лужения разного назначения (ГОСТ 13345-85)
- Жесть ЭЖК-Д — белая консервная жесть электролитического лужения с дифференцированным покрытием (ГОСТ 13345-85)
- Жесть ЭЖОН белая жесть электролитического лужения общего назначения (ТП 14-101-105; СТП ЭПК-01-2005)
Подразделения жести по степени твердости: А1, А2, В, С, D Подразделения жести по массе покрытия оловом:
- для белой жести горячего лужения: I и II классы,
- для белой жести электролитического лужения: с одинаковым покрытием I, II, и III классов, с дифференцированным покрытием ДI, ДII, ДIII.
Перспективно применение жести с безоловянным покрытием — электролитически хромированной с толщиной слоя металлического хрома 0,01—0,05 мкм, на который наносится слой эпоксифенольного лака толщиной 3—8 мкм.
По видам производства жесть может производиться в листах или рулонах.
Допустимые отклонения в производстве[править | править код]
Разнотолщинность в разных точках листа или полосы в рулоне на участке длиной 1 м для жести белой марки ЭЖК не должна превышать (ГОСТ Р 52204-2004): 0,01 мм — для жести толщиной от 0,14 до 0,28 мм включительно; 0,02 мм — для жести толщиной от 0,29 до 0,36 мм включительно. Для жести марки ЭЖР допускается увеличение нормы разнотолщинности на 0,01 мм по сравнению с жестью марки ЭЖК. Разнотолщинность в разных точках листа или полосы в рулоне на участке длиной 1 м для жести марки ЭЖК не должна превышать (ГОСТ 13345-85): 0,01 мм — для жести толщиной 0,18 мм; 0,02 мм — для жести толщиной от 0,20 до 0,32 мм включительно; 0,03 мм — для жести толщиной 0,36 мм.
- Консервные банки. Тара из жести имеет преимущество перед упаковкой из картона или пластика, а именно легкость процесса высокотемпературной стерилизации продукта. Однако, наряду с этим есть и недостаток — невозможность использования для разогрева в микроволновой печи.
- Тара для лакокрасочных материалов.
- Тара для нефтехимических продуктов.
- Хозяйственные изделия — ведра, банки, крышки, терки и пр.
- Аэрозольные баллоны с различным содержимым.
- Художественно оформленная тара из жести, применяемая для хранения пищевых или косметических продуктов.
- Информационные указатели, начиная от дверных табличек, и заканчивая дорожными знаками
- В строительстве — кровельные элементы, системы вентиляций, трубы, козырьки и пр.
- Несущие конструкции миниатюрных моделей транспортных средств и техники, в том числе радиоуправляемые.
- ↑ Этимологический словарь русского языка. — М.: Прогресс М. Р. Фасмер 1964—1973
ru.wikipedia.org
Что такое сталь?
Что такое сталь от чего зависят ее свойства?
Как известно, сталь представляет собой сплав, в основном состоящий из железа и углерода. Благодаря присутствию последнего, в отличие от чистого железа, сталь приобретает более высокие прочностные характеристики, при этом материал теряет пластичность (ковкость).
Свойства стали, как правило, зависят от ее химического состава, прежде всего углерода, содержание которого может варьироваться в зависимости от сорта стали от 0,2 до 2,14%. С увеличением доли углерода сталь становится более прочной, но и более хрупкой. Сплав железа с углеродом в количестве свыше 2,14% уже является чугуном.
Хотя углерод является основным связующим (легирующим) материалом в стали, для этой цели также могут быть использованы некоторые другие элементы, такие как вольфрам, хром, никель, марганец, титан молибден и другие.
Различные типы и количества легирующих элементов использованы определения твердости, пластичности и прочности стали.
Легирующий элемент отвечает за поддержание структуры кристаллической решетки стали путем предотвращения перемещению атомов железа. Таким образом, он действует для стали в качестве затвердителя.
Плотность стали в зависимости от добавленных в нее компонентов варьируется в диапазоне от 7750 и 8050 кг/м3.
Еще одним способом изменения механических свойств стали является ее термическая обработка. Этот процесс влияет на пластичность, твердость, электрические и теплопроводные свойств стали.
Для чего используется сталь?
Существуют различные виды стали, такие как углеродистая сталь, мягкая сталь, нержавеющая сталь, оцинкованная сталь и другие, которые в основном используется для строительства. Здания, стадионы, железнодорожные пути, мосты и тому подобное.
Кроме того, сталь используется практически во всех отраслях промышленности, производстве транспортных средств, судов, самолетов и так далее.
Большинство ежедневно используемых нами предметов быта также изготовлено из стали, например посуда, бытовая техника. В наше время сталь используют также для изготовления мебели, она является неотъемлемой частью стиля Hi Tech.
Для чего нужны нержавеющие и оцинкованные стали?
Несмотря на все преимущества стали, такие как твердость, долговечность, тепло и электропроводность, от железа она унаследовала один основной недостаток – подверженность коррозии – ее способность окисляться.
Путем долгих исследований и испытаний человечество получило стали, способные успешно бороться с коррозией нержавеющую и оцинкованную сталь.
Нержавеющая сталь
Нержавеющая сталь в отличие от других стальных сплавов, практически не подвержена коррозии или ржавчине. При этом она имеет все основные свойства стали – прочность, износостойкость, пластичность.
По составу нержавеющая сталь отличается от углеродистой стали количеством присутствующего в ней хрома. Она содержит как минимум 10,5-11% хрома. Поэтому на поверхности нержавеющей стали, образуется слой оксида хрома, который является инертным. Это является основной причиной антикоррозионных свойств нержавеющей стали. Благодаря этому, нержавеющая сталь используется в случаях контакта поверхности металла с водой или агрессивными средами.
Оцинкованная сталь
Оцинкованная сталь это та же углеродистая сталь с нанесенным покрытием, предохраняющим металл от коррозии. Как можно догадаться в качестве покрытия оцинкованной стали используется материал с высокими антикоррозионными свойствами — цинк. Технологический процесс нанесения цинка на углеродистую сталь называется цинкованием или гальванизация. Существует два способа нанесения цинкового покрытия – погружение в расплавленный цинк и метод электролиза, выделение цинка на поверхности стали из солей цинка под воздействием электрического тока.
Более подробно подробную информацию читайте в статье «Различие между нержавеющей и оцинкованной сталью».
sdlc.ru
Что такое сталь?
Что такое сталь?
«Бытовое» определение стали звучит примерно так: «Твердый и прочный металл на основе железа с легированием небольшим количеством углерода, а также часто другими металлами, такими как никель, хром, марганец». Хотя и нельзя сказать, что это определение полностью неправильное, но оно вряд ли адекватно отражает понятие «сталь».
Более точное определение стали может быть таким: «Сплав на основе железа, хорошо деформируемый в определенном интервале температур и содержащий углерод, и часто другие легирующие элементы. В углеродистых и низколегированных сталях максимальное содержание углерода около 2 %, в высоколегированных сталях – до 2,5 %. Разделительная линия между низколегированными и высоколегированными сталями обычно проходит по 5 % металлических легирующих элементов.
Три фазы стали – феррит, цементит и аустенит
В принципе, все стали являются смесями, а точнее, сплавами железа и углерода. Однако даже самые обычные стали, так называемые стали общего назначения, имеют небольшие, но контролируемые количества марганца и кремния, а также малое и обычно неизбежное количество фосфора и серы. Содержание углерода в сталях общего назначения обычно составляет от 0,05 до 1,0 %.
Механизм легирования железа углеродом отличается от других систем сплавов тем, что является двухступенчатым. На первом этапе железо соединяется с 6,67 % углерода, образуя карбид железа, который чаще называют цементитом. Поэтому при комнатной температуре обычная сталь содержит смесь цементита и феррита. Оба они являются фазами. Фазой называют физически гомогенный и выделенную часть материальной системы. Когда сталь нагревают до 725 ºС цементит цементит растворяется в железе и образуется новая фаза – аустенит. Заметим, что не надо путать «фазы стали» и «структуры стали». Любая сталь может иметь только три фазы, тогда как может быть несколько структур, а также их смесей.
Классификация сталей
Невозможно определить точное число составов сталей, которые существует в настоящее время. Их насчитается, по крайней мере, за тысячу. Жесткой классификации сталей не существует. Однако чаще всего стали разбивают на пять групп, что вполне устраивает большинство специалистов, которые работаю со сталью.
К этим пяти классам относятся:
углеродистые стали;
легированные стали, иногда их называют низколегированными сталями;
нержавеющие стали – стандарты называют их «коррозионно-стойкими»;
инструментальные стали;
специальные стали,
К специальным сталям относят стали со специальными свойствами, которые нужны для применения их в специфических условиях работы. Кроме того, это могут быть стали, которые очень похожи на стали из первых четырех групп, но все таки настолько отличаются от них, что требуют отдельного обозначения сплава.
Почему сталь главная?
Было бы несправедливо заявлять, что какой-то один металл является более важным, чем другой. Например, без алюминия и титана не было бы современных самолетов и космических кораблей.
Сталь, тем не менее, значительно более широко применяется, чем любой другой металл. Обычно бытует мнение, что причина доминирования стали заключается в избытке железной руды, а также легкости, с которой железо можно извлекать из руды. И то, и другое ошибочно. Железо не является самым распространенным элементом. Извлекать его из руды не так-то просто, а вот, медь, например, в некоторых районах мира встречается в почти чистом виде.
Сталь является таким важным материалом благодаря ее невероятной гибкости в ее обработке и применении. Эту гибкость ей дает разнообразие вариантов ее структуры и методов деформационной и термической обработки для их достижения.
Широкие возможности для применения стали дают два ее важных металлургических феномена:
1) железо является аллотропическим элементом, то есть может существовать в более чем одной кристаллических форм;
2) размер атом углерода составляет только 1/30 от размера атома железа.
Железо – основа стали
Все чистые металлы, а также сплавы имеют индивидуальные фазовые диаграммы, которые чаще называют диаграммами состояния. Как правило, по горизонтальной оси откладывают процентное содержание в сплаве легирующего элемента. Температуру откладывают по вертикали. Диаграмма чистого железа является прямой линией. При охлаждении чистого железа оно изменяется от одной фазы в другую при постоянной температуре.
Чистое железо затвердевает при 1538 ºС с образованием кристаллической структуры, которая называют ферритом или дельта-железом. Эта фаза имеет объемноцентрированную кубическую атомную решетку . При дальнейшем охлаждении с достижением температуры 1395 ºС атомы перестраиваются в 14-ти атомную решетку, которая называется гамма-железо.
При продолжении охлаждения ниже температуры 910 °С структура железа возвращается 9-ти атомной решетке или альфа-железу. Изменение в точке 770 °С просто обозначает изменение от немагнитного железа к магнитному и не является сменой фаз. Все поле ниже 910 °С является ферритом вплоть до комнатной температуры и ниже. Феррит, который образуется выше аустенита, часто называют «дельта-феррит», а то феррит, которые образуется ниже точки А3 – альфа-феррит, хотя структурно оба они совершенно одинаковые.
Механизм аллотропии является наиважнейшим свойством железа, которое и обеспечивает ему разнообразие его структуры и гибкость термической обработки сталей.
steel-guide.ru
История производства и использования железа — Википедия
Выплавка железа в Средние века[1]История производства и использования железа берёт своё начало в доисторической эпохе, скорее всего, с использования метеоритного железа. Выплавка в сыродутной печи применялась в XII веке до н. э. в Индии, Анатолии и на Кавказе. Также отмечается использование железа при выплавке и изготовлении орудий и инструментов в 1200 году до н. э. в Африке южнее Сахары[2][3]. Уже в первом тысячелетии до н. э. использовалось кованое железо (англ. Wrought iron). Об обработке железа упоминается в первой книге Библии (Быт. 4:22).
Диаграмма состояний сплавов железа и углеродаМатериал, в обиходе называемый «железом», как правило, является сталью или чугуном и представляет собой сплав железа (Fe), как химического элемента, с углеродом (C). Кроме железа и углерода сплав содержит незначительные количества других химических элементов.
При концентрации углерода в сплаве менее 0,3 % получается мягкий пластичный тугоплавкий (температура плавления железа 1539 °C) сплав, за которым и закрепляется название его основного ингредиента — железа. Представление о том железе, с которым имели дело наши предки, сейчас можно получить, исследовав механические свойства гвоздя.
При концентрации углерода в сплаве от 0,3 до 2,14 % сплав называется «сталью». В первозданном виде сталь походит по своим свойствам на железо, но, в отличие от него, поддается закалке: при резком охлаждении после нагрева до определённых температур сталь приобретает большую твёрдость — замечательное достоинство, однако, почти совершенно сводимое на нет приобретённой в процессе той же закалки хрупкостью.
При концентрации углерода в сплаве свыше 2,14 % сплав называется «чугуном». Чугун — хрупкий легкоплавкий сплав, пригодный для литья, но не поддающийся обработке ковкой. Чугун насыщен графитовыми включениями, делающими его неоднородным и механически непрочным. Температура плавления чугуна варьируется от 1150 до 1300 °C.
Технологии производства и обработки железа и сплавов[править | править код]
Для производства железа исторически применялось несколько технологий, которые сложно расположить в хронологическом порядке.
Метеоритное железо[править | править код]
Использование железа началось намного раньше, чем его производство. Иногда люди находили куски серовато-чёрного металла, попавшие на Землю с метеоритами — метеоритное железо, использовали их для изготовления оружия: перековывали в кинжалы или наконечники копий. Метеоритное железо было более прочным и пластичным, чем бронза, и дольше «держало» остроту лезвия. Поскольку железные метеориты содержали железоникелевый сплав, можно предположить, что качество некоторых уникальных кинжалов могло соперничать с современным ширпотребом[4]. Однако, та же уникальность приводила к тому, что такое оружие оказывалось не на поле боя, а в сокровищнице очередного правителя.
Сыродутная печь[править | править код]
Первым устройством для получения железа из руды стала одноразовая сыродутная печь (сыродутный горн, домница). Несмотря на наличие недостатков способ получения железа с использованием такой печи долгое время оставался единственным способом получения железа из руды. На Руси появление первых домниц относят к IX веку[5].
Впервые железо научились обрабатывать народы Анатолии. Древние греки считали, что открывателями железа был народ халибов. В литературе этот народ назывался устойчивым выражением «отец железа». Слово «сталь» на греческом языке («Χάλυβς») происходит от этого этнонима.
«Железная революция» началась на рубеже I тысячелетия до нашей эры в Ассирии. Железные мечи научились изготавливать представители Гальштатской культуры. С VIII века до нашей эры сварочное железо быстро стало распространяться в Европе, в III веке до нашей эры оно вытеснило бронзу в Галлии, во II веке новой эры появилось в Германии, а в VI веке уже широко употреблялось в Скандинавии; племенами же, проживающими на территории будущей Руси — киммерийцами, а позже скифами и сарматами — железо использовалось ещё до н. э.. В Японии железный век наступил только в VII веке нашей эры.
Известный популяризатор науки Айзек Азимов так описывает историю перехода человечества из бронзового века в железный[6]:
Где-то около XV—XIV вв. до н. э. техника выплавки и науглероживания железа была разработана в кавказских предгорьях в Урарту. Эта страна находилась тогда под властью Хеттского царства, которое находилось на высшей точке своей мощи. Хеттские цари тщательно охраняли монополию на новую технику, ибо понимали её важность. Вначале получали только маленькие партии железа, и в течение нескольких столетий оно стоило порой в сорок раз дороже серебра. Но ещё до того, как выплавку можно было увеличить, а хеттам — этим воспользоваться, им пришёл конец. Хеттское царство было разрушено во время беспорядков, последовавших за движением «народов моря», и хеттская монополия на железо была нарушена. Технология выплавки железа быстро распространялась в том числе, конечно, в Ассирию, которая граничила с «железным царством» Урарту. Торговля железом восстановила процветание Ассирии. Открылся путь для новых завоеваний. Вторгшиеся в Грецию дорийские племена обладали железным оружием, именно поэтому они так легко покорили вооруженных бронзой ахейцев. Было железо и у «народов моря», и, когда филистимляне захватывали ханаанское побережье, в сражениях они использовали железное оружие, Но они были не настолько глупы, чтобы раскрывать секрет выплавки железа. Пока им удавалось хранить эту техническую тайну, израильтянам приходилось обороняться более примитивным оружием. Благодаря железу филистимляне не только легко закрепились на побережье, но и обложили данью ближайшие к ним племена. Около двух веков (до прихода к власти Давида в 1013 году до н. э.) им удавалось господствовать над более многочисленными израильскими племенами. |
Первым шагом в зарождающейся чёрной металлургии было получение железа путём восстановления его из окиси. Болотная руда перемешивалась с древесным углём и закладывалась в печь. При высокой температуре, создаваемой горением угля, углерод начинал соединяться не только с атмосферным кислородом, но и с тем кислородом, который был связан с атомами железа.
После выгорания угля в печи оставалась так называемая «крица» — комок пористого восстановленного железа с примесью большого количества шлаков. Крицу потом снова разогревали и подвергали обработке ковкой, выколачивая шлак из железа. Полученный брусок железа (в котором всё же оставалось 2—4 % шлака) назывался «кричной болванкой». Долгое время ковка была основным процессом в технологии производства железа, причём, с приданием изделию формы она была связана в последнюю очередь. Ковкой получался сам материал.
Сварное оружие[править | править код]
Сталь производилась уже из готового железа путём насыщения углеродом последнего. При высокой температуре и недостатке кислорода углерод, не успевая окисляться, пропитывал железо. Чем больше было углерода, тем твёрже оказывалась сталь после закалки.
Как можно было заметить, ни один из перечисленных выше сплавов не обладает таким свойством, как упругость. Железный сплав может приобрести это качество, только если в нём возникает чёткая кристаллическая структура, что происходит, например, в процессе застывания из расплава. Проблема же древних металлургов заключалась в том, что расплавить железо они не могли. Для этого требуется разогреть его до 1540 °C, в то время как технологии древности позволяли достичь температур в 1000‑1300 °C. Вплоть до середины XIX века было невозможно расплавить железо и сталь с содержанием углерода менее 0,4 %, так как плавкость железных сплавов снижается по мере уменьшения концентрации углерода.
Таким образом ни железо, ни сталь сами по себе для изготовления оружия не годились. Орудия и инструменты из чистого железа выходили слишком мягкими, а из чистой стали — слишком хрупкими. Потому, чтобы изготовить, например, меч, приходилось делать «бутерброд» из двух пластин железа, между которыми закладывалась стальная пластина. При заточке мягкое железо стачивалось и появлялась стальная режущая кромка.
Такое оружие, сваренное из нескольких слоёв с разными механическими свойствами, называлось сварным. Общими недостатками этой технологии являлись излишняя массивность и недостаточная прочность изделий. Сварной меч не мог пружинить, вследствие чего неизбежно ломался или гнулся при ударе о непреодолимую преграду.
Отсутствием упругости недостатки сварного оружия не исчерпывались. В дополнение к упомянутым недостаткам, его, например, невозможно было «толком» заточить. Железу можно было придать какую угодно остроту (хотя и стачивалось оно быстро), но и тупилась мягкая режущая кромка из железа почти мгновенно. Сталь же точиться не желала — режущая кромка крошилась. Здесь налицо полная аналогия с карандашами — мягкий грифель легко сделать острым, но он сразу затупится, а твёрдый до особой остроты не доведёшь — десять раз сломается. Так что, бритвы приходилось делать из железа и затачивать заново ежедневно.
В целом же сварное оружие не превосходило остротой столовый нож. Уже одно это обстоятельство требовало делать его достаточно массивным для придания удовлетворительных рубящих свойств.
Единственной мерой, позволяющей достичь сочетания остроты и твёрдости в рамках технологии сварки, была закалка изделия уже после его заточки. Применим же этот метод становился в случае, если стальная режущая кромка приваривалась просто к железному обуху, а не заключалась в «бутерброд» из железа. Либо после заточки могли быть закалены клинки, у которых железный сердечник покрывался снаружи сталью. Недостатком такого метода было то, что заточка оказывалась возможна лишь однажды. Когда стальное лезвие повреждалось и тупилось, весь клинок приходилось перековывать.
Тем не менее именно освоение техники сварки — несмотря на все её недостатки — произвело настоящий переворот во всех сферах человеческой деятельности и привело к огромному возрастанию производительных сил. Сварные орудия были вполне функциональны и, при том, общедоступны. Только с их распространением каменные орудия оказались окончательно вытеснены, и наступил век металла.
Железные орудия решительно расширили практические возможности человека. Стало возможным, например, строить рубленные из брёвен дома — ведь железный топор валил дерево уже не в три, как медный, а в 10 раз быстрее, чем каменный. Широкое распространение получило и строительство из тёсаного камня. Он, естественно, употреблялся и в эпоху бронзы, но большой расход сравнительно мягкого и дорогого металла решительно ограничивал такие эксперименты. Значительно расширились также и возможности земледельцев.
Булатная сталь и дамаск[править | править код]
Увидеть железо жидким металлурги смогли только в XIX веке, однако ещё на заре железной металлургии — в начале I тысячелетия до нашей эры — индийские мастера сумели решить проблему получения высокоуглеродистой стали с композитной структурой. Такую сталь называли булатом, но из-за сложности изготовления и отсутствия необходимых материалов в большей части мира эта сталь так и осталась индийским секретом на долгое время.
Более технологичный путь получения упругой стали, при котором не требовались ни особо чистая руда, ни графит, ни специальные печи, был найден в Китае во II веке нашей эры. Сталь перековывали до двенадцати раз, при каждой ковке складывая заготовку вдвое, в результате чего получался отличный оружейный материал, называемый «дамаском», из которого, в частности, делались японские катаны (мечи). Количество слоёв стали рассчитывается по формуле A=2Nx{\displaystyle A=2^{N}x}, где N{\displaystyle N} — количество проковок, а x{\displaystyle x} — изначальное количество видов (слоёв) стали, сковываемой в «бутерброд». При каждой ковке количество слоёв удваивалось, а после 12 проковок количество слоёв достигало 4096, и слои становились неразличимы.
Штукофен[править | править код]
Более высокую, по сравнению с сыродутной печью, ступень в развитии чёрной металлургии представляли собой постоянные высокие печи, называемые в Европе штукофенами. Это действительно была высокая печь — с четырёхметровой трубой для усиления тяги. Мехи штукофена «качались» уже несколькими людьми, а иногда и водяным двигателем. Штукофен имел дверцы, через которые раз в сутки извлекалась крица.
Изобретены штукофены были в Индии в начале первого тысячелетия до новой эры. В начале нашей эры они попали в Китай, а в VII веке вместе с «арабскими» цифрами арабы заимствовали из Индии и эту технологию. В конце XIII века штукофены стали появляться в Германии и Чехии (а ещё до того были на юге Испании) и в течение следующего века распространились по всей Европе.
Производительность штукофена была несравненно выше, чем сыродутной печи — в день он давал до 250 кг железа, а температура в нём оказывалась достаточна для науглероживания части железа до состояния чугуна. Однако штукофенный чугун при остановке печи застывал на её дне, смешиваясь со шлаками, а очищать металл от шлаков умели тогда только ковкой, но как раз ей-то чугун и не поддавался. Его приходилось выбрасывать.
Иногда, впрочем, штукофенному чугуну пытались найти какое-то применение. Например, древние индусы отливали из грязного чугуна гробы, а турки в начале XIX века — пушечные ядра. Трудно судить, сколь хорошими были гробы, но ядра из него получались невысокого качества.
Ядра для пушек из железистых шлаков в Европе отливали ещё в конце XVI века. Из литой брусчатки делались дороги. В Нижнем Тагиле до сих пор сохранились здания с фундаментами из литых шлаковых блоков[7].
Блауофен[править | править код]
Металлурги давно заметили связь между температурой плавления и выходом продукта — чем выше была температура, тем большую часть содержащегося в руде железа удавалось восстановить. Потому рано или поздно им приходила мысль улучшить штукофен — добавить предварительный подогрев воздуха и увеличить высоту трубы. В середине XV века в Европе появились печи нового типа — блауофены, которые сразу преподнесли сталеварам неприятный сюрприз.
Более высокая температура действительно значительно повысила выход железа из руды, но она же повысила и долю железа науглероживающегося до состояния чугуна. Теперь уже не 10 %, как в штукофене, а 30 % выхода составлял чугун — «свиное железо», ни к какому делу не годное. В итоге, выигрыш часто не окупал модернизации.
Блауофенный чугун, как и штукофенный, застывал на дне печи, смешиваясь со шлаками. Он выходил несколько лучшим, так как его самого было больше, следовательно, относительное содержание шлаков выходило меньше, но продолжал оставаться малопригодным для литья. Чугун, получаемый из блауофенов, оказывался уже достаточно прочен, но оставался ещё очень неоднородным. Из него выходили только предметы простые и грубые — кувалды, наковальни, пушечные ядра.
Кроме того, если в сыродутных печах могло быть получено только железо, которое потом науглероживалось, то в штукофенах и блауофенах внешние слои крицы оказывались состоящими из стали. В блауофенных крицах стали было даже больше, чем железа. С одной стороны, это было хорошо, но вот отделить сталь от железа оказалось весьма затруднительно. Содержание углерода становилось трудно контролировать. Только долгой ковкой можно было добиться однородности его распределения.
В своё время, столкнувшись с этими затруднениями, индусы не стали двигаться дальше, а занялись тонким усовершенствованием технологии и пришли к получению булата. Но индусов в ту пору интересовало не количество, а качество продукта. Европейцы, экспериментируя с чугуном, скоро открыли передельный процесс, поднявший металлургию железа на качественно новый уровень.
Доменная печь[править | править код]
Следующим этапом в развитии металлургии стало появление доменных печей. За счёт увеличения размера, предварительного подогрева воздуха и механического дутья, в такой печи всё железо из руды превращалось в чугун, который расплавлялся и периодически выпускался наружу. Производство стало непрерывным — печь работала круглосуточно и не остывала. За день она выдавала до полутора тонн чугуна. Перегнать же чугун в железо в горнах было значительно проще, чем выколачивать его из крицы, хотя ковка все равно требовалась — но теперь уже выколачивали шлаки из железа, а не железо из шлаков.
Хотя найденные в Китае чугунные изделия восходят к V веку до нашей эры[8], самые ранние доменные печи, производящие чугун в «чушках» (слитках), который мог переплавляться в очищенный чугун в вагранках, датируются III—II веками до нашей эры. Подавляющее большинство обнаруженных ранних мест доменного производства относятся к периоду после введения государственной монополии на соль и железорудную промышленность в 117 году до нашей эры (период правления императора У-ди, 141—87 до н. э.) в эпоху династии Хань (202 год до нашей эры — 220 год нашей эры). Большинство железоделательных мест, открытых до 117 года до нашей эры, занимались лишь литьём из заготовок, выплавленных в доменных печах в других районах, отдалённых от населённых пунктов[9][10].
В Европе доменные печи впервые были применены на рубеже XV—XVI веков. На Ближнем Востоке и в Индии эта технология появилась только в XIX веке (в значительной степени, вероятно, потому, что водяной двигатель из-за характерного дефицита воды на Ближнем Востоке не употреблялся). Наличие в Европе доменных печей позволило ей обогнать в XVI веке Турцию если не по качеству металла, то по валу. Это оказало несомненное влияние на исход борьбы, особенно когда оказалось, что из чугуна можно лить пушки.
Георгий Агрикола так описывает средневековую технологию плавки[11]:
Обычай выдающихся плавильщиков, умеющих управлять четырьмя элементами (имеются в виду земля, воздух, огонь и вода — вне цитаты), таков. Они смешивают в правильных пропорциях руды, содержащие земли, и загружают их в печи. Затем льют нужное количество воды и умело управляют движением воздуха, поступающего из мехов, забрасывая руду туда, где огонь горит с наибольшей силой. Мастер равномерно обрызгивает водой внутреннее пространство печи, слегка увлажняя древесный уголь с тем, чтобы к нему приставали мелкие частицы руды; иначе эти частицы приводятся в движение силой дутья и огня и уносятся вместе с дымом. |
Также Агрикола верно объясняет необходимость изменения конструкции печи в зависимости от типа руд[11]:
Так как природа руд, подлежащих плавке, бывает различной, плавильщикам приходится устраивать горн то выше, то ниже и устанавливать трубу, куда вводятся насадки мехов под меньшим или большим углом для того, чтобы дутье при надобности было более или менее сильным. Если руды нагреваются и плавятся легко, то для работы плавильщиков необходим низкий горн, а труба должна быть установлена под небольшим углом, чтобы дутье было легкое. Наоборот, если руды нагреваются и плавятся медленно, то требуется высокий горн, а труба должна быть установлена с крутым уклоном, чтобы обеспечить сильное дутье. Для руд этого рода нужна весьма горячая печь, в которой сначала расплавляются шлаки, штейны или легкоплавкие камни для того, чтобы руда не могла пригореть к поду горна и закрыть выпускное отверстие. |
Передельный процесс[править | править код]
С XVI века в Европе получил распространение так называемый передельный процесс в металлургии — технология, при которой железо ещё при получении за счёт высокой температуры плавления и интенсивного науглероживания перегонялось в чугун, а уже затем, жидкий чугун, освобождаясь от лишнего углерода при отжиге в горнах, превращался в сталь.
Из передельной стали уже можно было изготавливать кривые мечи (например, сабли), чего не позволяла сделать сварная технология.
Применение угля, коксование, пудлингование, горячее дутьё[править | править код]
С начала XVII века европейской кузницей стала Швеция, производившая половину железа в Европе. В середине XVIII века её роль в этом отношении стала стремительно падать в связи с очередным изобретением — применением в металлургии каменного угля.
Прежде всего надо сказать, что до XVIII века включительно каменный уголь в металлургии практически не использовался — из-за высокого содержания вредных для качества продукта примесей, в первую очередь — серы. С XVII века в Англии каменный уголь, правда, начали применять в пудлинговочных печах для отжига чугуна, но это позволяло достичь лишь небольшой экономии древесного угля — большая часть топлива расходовалась на плавку, где исключить контакт угля с рудой было невозможно.
Потребление же топлива в металлургии уже тогда было огромно — домна (доменная печь) пожирала воз угля в час. Древесный уголь превратился в стратегический ресурс. Именно изобилие дерева в самой Швеции и принадлежащей ей Финляндии позволило шведам развернуть производство таких масштабов. Англичане, имевшие меньше лесов (да и те были зарезервированы для нужд флота), вынуждены были покупать железо в Швеции до тех пор, пока не научились использовать каменный уголь. Его ввёл в употребление в XVII веке Клемент Клерк и его мастера кузнечных дел и литья.
С 1709 году в местечке Коулбрукдейл Абрахам Дарби, основатель целой династии металлургов и кузнецов, использовал кокс для получения чугуна из руды в доменной печи. Из него поначалу делали лишь кухонную утварь, которая отличалась от работы конкурентов лишь тем, что её стенки были тоньше, а вес меньше. В 1750-х годах сын Дарби (Абрахам Дарби II) построил ещё несколько домен, и к этому времени его изделия были ещё и дешевле, чем изготовленные на древесном угле. В 1778 году внук Дарби, Абрахам Дарби III, из своего литья построил в Шропшире знаменитый Железный мост, первый мост в Европе, полностью состоящий из металлических конструкций.
Для дальнейшего улучшения качества чугуна в 1784 году Генри Корт разработал процесс пудлингования. Среди многих металлургических профессий того времени, пожалуй, самой тяжелой была профессия пудлинговщика. Пудлингование было основным способом получения железа почти на протяжении всего XIX века. Это был очень тяжёлый и трудоёмкий процесс. Работа при нём шла так. На подину пламенной печи загружались чушки (слитки) чугуна; чушки расплавляли. По мере выгорания из металла углерода и других примесей температура плавления металла повышалась, и из жидкого расплава начинали «вымораживаться» кристаллы довольно чистого железа. На подине печи собирался комок слипшейся тестообразной массы. Рабочие-пудлинговщики приступали к операции накатывания крицы при помощи железного лома. Перемешивая ломом массу металла, они старались собрать вокруг лома комок, или крицу, железа. Такой комок весил до 50—80 кг и более. Крицу вытаскивали из печи и подавали сразу под молот — для проковки с целью удаления частиц шлака и уплотнения металла[7].
Рост производства и улучшение качества английского металла к концу XVIII века позволило Великобритании полностью отказаться от импорта шведского и российского железа. Развернулось сооружение каналов, позволявших перевозить уголь и металлы.
С 1830 по 1847 год производство металла в Англии возросло более чем в 3 раза. Применение горячего дутья при плавке руды, начавшееся в 1828 году, втрое сократило расход топлива и позволило использовать в производстве низшие сорта каменного угля, С 1826 по 1846 год экспорт железа и чугуна из Великобритании увеличился в 7,5 раза[12].
Конвертерное производство и мартеновские печи[править | править код]
В 1856 году Генри Бессемер получил патент на новую технологию производства стали (бессемеровский процесс). Он изобрёл конвертер — устройство, в котором сквозь жидкий чугун, получаемый в доменных печах, продувался воздух. В конвертере происходит выгорание углерода, растворённого в железе, что позволяет получать сталь в существенно больших количествах, чем это было ранее доступно.
Альтернативой применения конвертера на протяжении XX века являлась мартеновская печь, в которой также происходило дожигание углерода. К концу XX века мартеновские печи стали очевидно устаревшей технологией и были вытеснены кислородно-конвертерным производством стали.
В середине XX века был изобретён турбодетандер, позволяющий снизить затраты на производство кислорода. Кислород стал достаточно дешёвым, чтобы получить массовое применение в сталелитейной промышленности. Продувка расплавленного чугуна кислородом существенно разогревает металл, что упрощает производство (железо не «вымораживается», а остаётся жидким), позволяет также в конвертер сбрасывать металлолом для переплавки, а также в ряде случаев улучшает качество металла за счёт отсутствия растворённого в металле азота.
Электрометаллургия[править | править код]
Способность постоянного электрического тока восстанавливать металлы была обнаружена ещё в самом начале XIX века, однако отсутствие мощных источников электроэнергии ограничивало применение этих процессов лабораторными исследованиями. Появление в начале XX века мощных электростанций позволило создать промышленные технологии электрометаллургии. Изначально такие процессы применялись для производства цветных металлов, но к середине XX века пришли и в чёрную металлургию. Широкое применение нашли процессы электрической рудовосстанавливающей плавки, при которой железная руда, смешенная с незначительным количеством углерода, подвергается воздействию мощной электрической дуги, где происходит электрическое восстановление железа на катоде и выгорание примесей на аноде. Таким способом удаётся получить чугун высокого качества, сократить расход кислорода и снизить уровень выбросов углекислого газа. Передельные электрометаллургические процессы дают возможность плавить чугун в вакууме, в среде защитного газа, в присутствии химически активных легирующих элементов, что позволяет получать легированные стали высокого качества и специальные стали (жаропрочные, радиационно стойкие). Стали, получение которых возможно только электрометаллургическими процессами называют электросталями.
Восстановление водородом[править | править код]
Доменные печи и конвертерное производство является достаточно современным, но весьма грязным для экологии процессом. При том, что большая часть железа получается в кислородно-конвертерном производстве, велики и выбросы углекислого и угарного газов в атмосферу. Модной альтернативой становится прямое восстановление железа из руды водородом. При этом образующиеся частички железа расплавляются в электрических печах, после чего добавляется углерод и получается сталь.
Кузнецы-любители[править | править код]
Первыми производство железных изделий организовали кузнецы-любители — обычные крестьяне, промышлявшие таким ремеслом в свободное от обработки земли время. Кузнец сам находил «руду» (болотная руда вблизи ржавого болота или красный песок), сам выжигал уголь, сам строил сыродутную печь и выплавлял железо, сам ковал, сам обрабатывал.
Умение мастера на данном этапе закономерно было ограничено выковыванием изделий самой простой формы. Инструментарий же его состоял из мехов, каменных молота и наковальни и точильного камня. Железные орудия производились с помощью каменных инструментов.
Если удобные для разработки залежи руды имелись поблизости, то и целая деревня могла заниматься производством железа, но такое было возможным только при наличии устойчивой возможности выгодного сбыта продукции, чего практически не могло быть в условиях натурального хозяйства.
При такой организации производства железа, никогда не удавалось за его счёт полностью покрыть все потребности в самом простом оружии и самых необходимых орудиях труда. Из камня продолжали изготавливаться топоры, из дерева — гвозди и плуги. Металлические доспехи оставались недоступными даже для вождей. Концентрация железных изделий составляла всего порядка 200 граммов на душу населения[источник не указан 1036 дней].
На таком уровне доступности железа находились в начале нашей эры наиболее отсталые племена среди бриттов, германцев и славян. В XII‑XIII веке прибалты и финны сражаясь с крестоносцами пользовались ещё каменным и костяным оружием. Все эти народы умели уже делать железо, но ещё не могли получить его в необходимом количестве.[источник не указан 1036 дней]
Профессиональные кузнецы[править | править код]
ru.wikipedia.org
Производство стали – технология, оборудование, этапы
Производство стали сегодня осуществляется в основном из отработанных стальных изделий и передельного чугуна. Сталь представляет собой сплав железа и углерода, последнего в котором содержится от 0,1 до 2,14%. Превышение содержания углерода в сплаве приведет к тому, что он станет слишком хрупким. Суть процесса производства стали, в составе которой содержится гораздо меньшее количество углерода и примесей, по сравнению с чугуном, состоит в том, чтобы в процессе плавки перевести эти примеси в шлак и газы, подвергнуть их принудительному окислению.
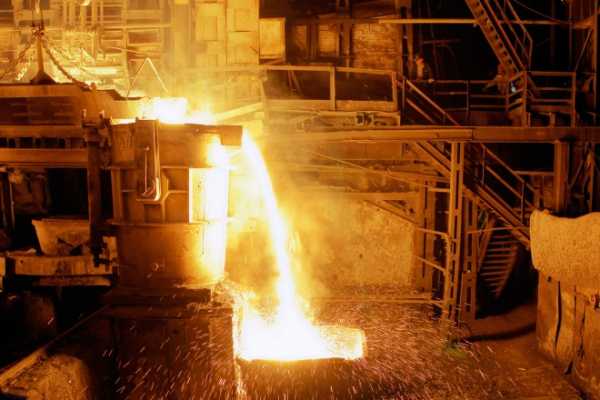
Процесс производства стали
Особенности процесса
Производство стали, осуществляемое в сталеплавильных печах, предполагает взаимодействие железа с кислородом, в процессе которого металл окисляется. Окислению также подвергаются углерод, фосфор, кремний и марганец, содержащиеся в передельном чугуне. Окисление данных примесей происходит за счет того, что оксид железа, образующийся в расплавленной ванне металла, отдает кислород более активным примесям, тем самым окисляя их.
Производство стали предполагает прохождение трех стадий, каждая из которых имеет свое значение. Рассмотрим их подробнее.
Расплавление породы
На данном этапе расплавляется шихта и формируется ванна из расплавленного металла, в которой железо, окисляясь, окисляет примеси, содержащиеся в чугуне (фосфор, кремний, марганец). В процессе этого этапа производства из сплава необходимо удалить фосфор, что достигается за счет содержания в шлаке расплавленного оксида кальция. При соблюдении таких условий производства фосфорный ангидрид (Р2О5) создает с оксидом железа (FeO) неустойчивое соединение, которое при взаимодействии с более сильным основанием — оксидом кальция (CaO) — распадается, и фосфорный ангидрид превращается в шлак.
Чтобы производство стали сопровождалось удалением из ванны расплавленного металла фосфора, необходима не слишком высокая температура и содержание в шлаке оксида железа. Чтобы удовлетворить эти требования, в расплав добавляют окалину и железную руду, которые и формируют в ванне расплавленного металла железистый шлак. Содержащий высокое количество фосфора шлак, формирующийся на поверхности ванны расплавленного металла, удаляется, а вместо него в расплав добавляются новые порции оксида кальция.
Кипение ванны расплавленного металла
Дальнейший процесс производства стали сопровождается кипением ванны расплавленного металла. Такой процесс активизируется с повышением температуры. Он сопровождается интенсивным окислением углерода, происходящим при поглощении тепла.
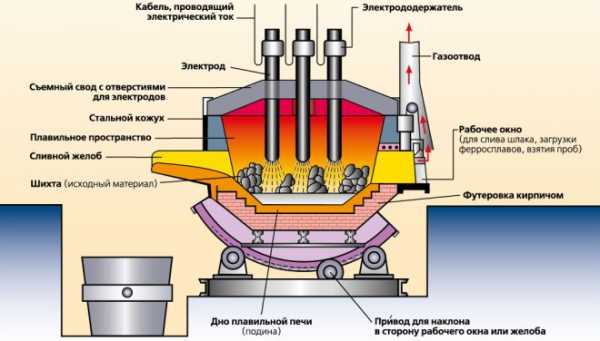
Процесс производства стали в электропечах
Производство стали невозможно без окисления излишков углерода, такой процесс запускают при помощи добавления в ванну расплавленного металла окалины или вдувания в нее чистого кислорода. Углерод, взаимодействуя с оксидом железа, выделяет пузырьки оксида углерода, что создает эффект кипения ванны, в процессе которого в ней снижается количество углерода, а температура стабилизируется. Кроме того, к всплывающим пузырькам оксида углерода прилипают неметаллические примеси, что способствует уменьшению их количества в расплавленном металле и приводит к значительному улучшению его качества.
На данной стадии производства из сплава также удаляется сера, присутствующая в нем в форме сульфида железа (FeS). При повышении температуры шлака сульфид железа растворяется в нем и вступает в реакцию с оксидом кальция (CaO). В результате такого взаимодействия образовывается соединение CaS, которое растворяется в шлаке, но раствориться в железе не может.
Раскисление металла
Добавление в расплавленный металл кислорода способствует не только удалению из него вредных примесей, но и увеличению содержания данного элемента в стали, что приводит к ухудшению ее качественных характеристик.
Чтобы уменьшить количество кислорода в сплаве, выплавка стали предполагает осуществление процесса раскисления, который может выполняться диффузионным и осаждающим методом.
Диффузионное раскисление предполагает введение в шлак расплавленного металла ферросилиция, ферромарганца и алюминия. Такие добавки, восстанавливая оксид железа, снижают его количество в шлаке. В результате растворенный в сплаве оксид железа переходит в шлак, распадается в нем, высвобождая железо, которое возвращается в расплав, а высвобожденные оксиды остаются в шлаке.
Производство стали с осаждающим раскислением осуществляется путем введения в расплав ферросилиция, ферромарганца и алюминия. Благодаря наличию в своем составе веществ, обладающих большим сродством к кислороду, чем железо, такие элементы образуют соединения с кислородом, который, отличаясь невысокой плотностью, выводится в шлак.
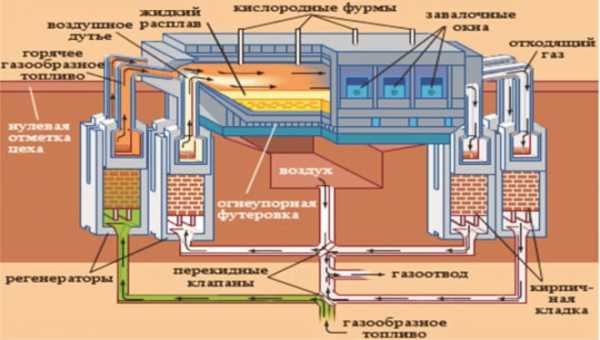
Производство стали в мартеновских печах
Регулируя уровень раскисления, можно получать кипящую сталь, которая не полностью раскислена в процессе плавки. Окончательное раскисление такой стали происходит при затвердевании слитка в изложнице, где в кристаллизующемся металле продолжается взаимодействие углерода и оксида железа. Оксид углерода, который образуется в результате такого взаимодействия, выводится из стали в виде пузырьков, также содержащих азот и водород. Полученная таким образом кипящая сталь, содержит незначительное количество металлических включений, что придает ей высокую пластичность.
Производство сталей может быть направлено на получение материалов следующего типа:
- спокойных, которые получаются, если в ковше и печи процесс раскисления полностью завершен;
- полуспокойных, которые по степени раскисления находятся между спокойными и кипящими сталями; именно такие стали раскисляются и в ковше, и в изложнице, где в них продолжается взаимодействие углерода и оксида железа.
Если производство стали предполагает введение в расплав чистых металлов или ферросплавов, то в результате получаются легированные сплавы железа с углеродом. Если в стали данной категории необходимо добавить элементы, которые имеют меньшее сродство к кислороду, чем железо (кобальт, никель, медь, молибден), то их вводят в процессе плавки, не опасаясь за то, что они окислятся. Если же легирующие элементы, которые необходимо добавить в сталь, имеют большее сродство к кислороду, чем железо (марганец, кремний, хром, алюминий, титан, ванадий), то их вводят в металл уже после его полного раскисления (на окончательном этапе плавки или в ковш).
Необходимое оборудование
Технология производства стали предполагает использование на сталелитейных заводах следующего оборудования.
Участок кислородных конверторов:
- системы обеспечения аргоном;
- сосуды конверторов и их несущие кольца;
- оборудование для фильтрации пыли;
- система для удаления конверторного газа.
Участок электропечей:
- печи индукционного типа;
- дуговые печи;
- емкости, с помощью которых выполняется загрузка;
- участок складирования металлического лома;
- преобразователи, предназначенные для обеспечения индукционного нагревания.
Участок вторичной металлургии, на котором осуществляется:
- очищение стали от серы;
- гомогенизация стали;
- электрошлаковый переплав;
- создание вакуумной среды.
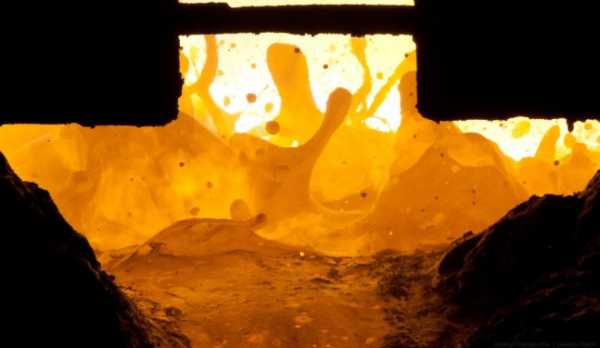
Кипящая сталь
Участок для реализации ковшовой технологии:
- LF-оборудование;
- SL-оборудование.
Ковшовое хозяйство, обеспечивающее производство стали, также включает в себя:
- крышки ковшей;
- ковши литейного и разливочного типа;
- шиберные затворы.
Производство стали также предполагает наличие оборудования для непрерывной разливки стали. К такому оборудованию относится:
- поворотная станина для манипуляций с разливочными ковшами;
- оборудование для осуществления непрерывной разливки;
- вагонетки, на которых транспортируются промежуточные ковши;
- лотки и сосуды, предназначенные для аварийных ситуаций;
- промежуточные ковши и площадки для складирования;
- пробочный механизм;
- мобильные мешалки для чугуна;
- оборудование для обеспечения охлаждения;
- участки, на которых выполняется непрерывная разливка;
- внутренние транспортные средства рельсового типа.
Производство стали и изготовление из нее изделий представляет собой сложный процесс, сочетающий в себе химические и технологические принципы, целый перечень специализированных операций, которые используются для получения качественного металла и различных изделий из него.
Оценка статьи:
Загрузка…Поделиться с друзьями:
met-all.org