4. Классификация сплавов. Железо и его сплавы. Материаловедение: конспект лекций [litres]
4. Классификация сплавов. Железо и его сплавы
Сталь и чугун – основные материалы в машиностроении. Они составляют 95 % всех используемых в технике сплавов.
Сталь – это сплав железа с углеродом и другими элементами, содержащий до 2,14 % углерода. Углерод – важнейшая примесь стали. От его содержания зависят прочность, твердость и пластичность стали. Кроме железа и углерода, в состав стали входят кремний, марганец, сера и фосфор. Эти примеси попадают в сталь в процессе выплавки и являются ее неизбежными спутниками.
Чугун – сплав на железной основе. Отличие чугуна от стали заключается в более высоком содержании в нем углерода – более 2,14 %. Наибольшее распространение получили чугуны, содержащие 3–3,5 % углерода. В состав чугунов входят те же примеси, что и в стали, т. е. кремний, марганец, сера и фосфор. Чугуны, у которых весь углерод находится в химическом соединении с железом, называют белыми (по виду излома), а чугуны, весь углерод которых или большая его часть представляет графит, получили название серых. В белых чугунах всегда имеется еще одна структурная составляющая – ледебурит. Это эвтектика, т. е. равномерная механическая смесь зерен аустенита и цементита, получающаяся в процессе кристаллизации, в ней 4,3 % углерода. Ледебурит образуется при температуре +1147 °C.
Феррит – твердый раствор небольшого количества углерода (до 0,04 %) и других примесей в? – железе. Практически это чистое железо. Цементит – химическое соединение железа с углеродом – карбид железа.
Перлит – равномерная механическая смесь в сплаве феррита и цементита. Такое название эта смесь получила потому, что шлиф при ее травлении имеет перламутровый оттенок. Так как перлит образуется в результате процессов вторичной кристаллизации, его называют эвтектоидом. Он образуется при температуре +727 °C. В нем содержится 0,8 % углерода.
Перлит имеет две разновидности. Если цементит в нем расположен в виде пластинок, его называют пластинчатым, если же цементит расположен в виде зерен, перлит называют зернистым. Под микроскопом пластинки цементита кажутся блестящими, потому что обладают большой твердостью, хорошо полируются и при травлении кислотами разъедаются меньше, чем пластинки мягкого феррита.
Если железоуглеродистые сплавы нагреть до определенных температур, произойдет аллотропическое превращение ? —железа в ? —железо и образуется структурная составляющая, которая называется аустенитом.
Аустенит представляет собой твердый раствор углерода (до 2,14 %) и других примесей в ? —железе. Способность углерода
растворяться в железе неодинакова при различных температурах. При температуре +727 °C ? —железо может растворять не более 0,8 % углерода. При этой же температуре происходит распад аустенита с образованием перлита. Аустенит – мягкая структурная составляющая. Он отличается большой пластичностью, не обладает магнитными свойствами.
При изучении структурных составляющих железоуглеродистых сплавов установлено, что они при комнатной температуре всегда состоят из двух структурных элементов: мягкого пластичного феррита и твердого цементита, упрочняющего сплав.
Поделитесь на страничкеtech.wikireading.ru
состав, структура, свойства, сферы применения, производство
Железо считается самым популярным материалом. Его используют во всех отраслях промышленности. Людям этот металл знаком с глубокой древности. Когда кузнецы научились получать чистый материал, он превзошёл известные на то время сплавы, вытеснил их из производства. Сплавы железа появились в результате попыток людей изменить характеристики этого металла.
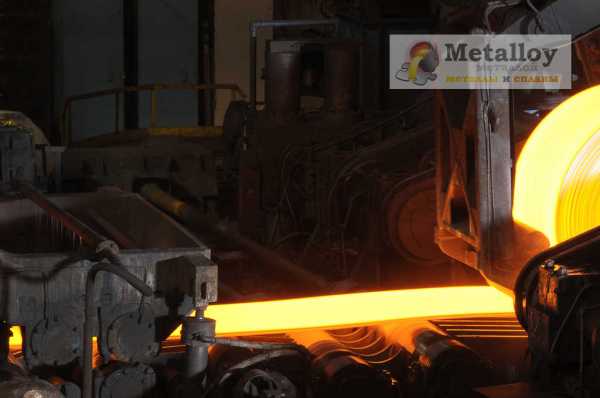
Сплав железа
Состав и свойства
Строение и свойства железа обуславливают его популярность относительно разных отраслей промышленности. Состав представляет собой основной материал с примесями другим веществ. Количество дополнительных металлов не превышает 0,8%. К основным параметрам относятся:
- Температура плавления — 1539 градусов по Цельсию.
- Твердость по Бринеллю — 350–450 Мн/кв. м.
- Удельная масса — 55,8.
- Плотность — 7,409 г/куб см.
- Теплопроводность — 74,04 Вт/(м·К) (при комнатной температуре).
- Электропроводность — 9,7·10-8 ом·м.
Нельзя забывать, что железо считается одним из важнейших элементов в организме человека. Однако он крайне сложно усваивается из пищи. Суточная норма, которую должен употреблять мужчина — 10 мг. Женщины должны потреблять 20 мг этого вещества, чтобы организм работал нормально.
История открытия
Из школьного курса все помнят «железный век». Это период истории, когда человек впервые научился получать этот металл из руды. Железный век приходится на период с 9 по 7 век до нашей эры. Этот металл оказал огромное влияние на развитие людей того времени. По своим характеристикам он вытеснил смеси цветных металлов. Из него изготавливали орудия труда, оружие, доспехи, материалы для строительства и многое другое. Постепенно кузнецы начали смешивать его с другими металлами, чтобы получить новые материалы. Так появлялись новые сплавы.
Сферы применения
Этот материл применяется в разных отраслях промышленности:
- Смеси и однородный металл применяются в машиностроении. Из них изготавливаются внутренние детали, корпуса, подвижные механизмы.
- Судостроение, самолётостроение, ракетостроение.
- Строительство — изготовление крепежей, расходных материалов.
- Приборостроение — изготовление электроники для дома.
- Радиоэлектроника — создание элементов для электроприборов.
- Медицина, станкостроение, химическая промышленность.
- Изготовление оружия.
Если для чего-то не подходит однородный материал, подойдут соединения на его основе, характеристики которых значительно отличаются.
Разновидности сплавов на основе железа
Сплав железа — это соединение, которое состоит из основного металла и дополнительных примесей. Соединения на основе этого материала называются чёрными металлами. К ним относятся:
- Сталь — соединение углерода с другими элементами. Углерода в составе сплава может содержаться до 2.14%. Выделяют конструкционные углеродистые, строительные, специальные и легированные стали.
- Чугун — смесь, которая пользуется огромной популярностью. Соединения могут содержать до 3,5% углерода. Дополнительно смеси содержать марганец, фосфор, серу.
- Перлит — смесь на основе железа. Содержит не более 0.8% углерода.
- Феррит — его называют чистым материалом. Связанно это с низким содержанием углерода, сторонних примесей (около 0.04%).
- Цементит — химическое соединение железа с углеродом.
- Аустенит — соединение с содержанием углерода до 2.14%. Дополнительно имеет сторонние примеси.
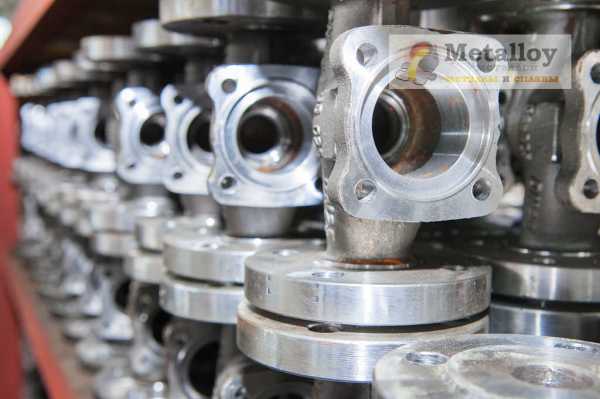
Легированная сталь
Состав и структура сплавов
Из-за большого количество соединений на основе железа была разработана маркировка, по которой можно отделить стали с высоким содержанием углерода от менее углеродистых, определить наличие основных легирующих элементов в составе материала, их количество. Зависимо от количества дополнительных элементов изменяются свойства соединений. К ним относится бор, ванадий, молибден, марганец, титан, углерод, хром, никель, кремний, вольфрам.
Характеристики смесей зависят от их структуры, состава. От этого изменяется прочность, пластичность, температура плавления, плотность, электропроводность и другие параметры. Например, структура чугуна определяет его хрупкость при ударах, больших физических нагрузках.
Свойства и маркировка сплавов
Относительно маркировки, первые цифры, которые идут на маркировке, говорят о процентном содержании углерода в составе. Далее идут заглавные буквы основных легирующих элементов. Начало маркировки могут начинать дополнительные буквы. Они указывают на назначение сплава.
Пластичность и вязкость будут уменьшаться при повышении количества углерода в составе сплава. На другие свойства металлов влияют основные легирующие элементы.
Производство и обработка сплавов на основе железа
Чтобы понять, как получают популярные соединения на основе железа, нужно кратко поговорить о технологиях получения чугуна, стали. Получить сталь можно несколькими способами:
- Прямая технология. Окатышки железной руды продуваются смесью угарного газа, кислорода аммиака. Процедура проводиться в шахтной печи разогретой до 1000 градусов.
- Мартеновский метод. Твердый чугун переплавляют с помощью мартеновских печей. Прежде чем закончить процедуру материал насыщается примесями.
- Электроплавильный способ. С его помощью получают высококачественный материал. Обработка проводится в закрытых печах при температуре до 2200 градусов.
- Кислородно-конверторный метод. Чугун, расположенный в печи, обдувается смесью кислорода с воздухом, что ускоряет процесс отжига.
Производство чугуна:
- Подготовка руды. Она дробится до мелкой фракции.
- Измельчение коксового угля.
- Дробление флюса.
- Загрузка в печь.
Для изготовления чугуна используются доменные печи.
Помимо процессов производства смесей, их подвергают дополнительно обработке. Это отжиг, нормализация, закалка и отпуск. Характеристики улучшаются.
Сплавы железа используются в разных отраслях промышленности. Они обладают разными характеристиками, однако не теряют параметров основного металла, входящего в их состав.
Металлургия стали 1 — железо, растворы, феррит, аустенит, цементит и перлит
Watch this video on YouTube
metalloy.ru
Классификация железоуглеродистых сплавов
Все железоуглеродистые сплавы, в соответствии с диаграммой железо-углерод, подразделяются на техническое железо (содержание углерода в сплаве менее 0,02%), стали (содержание углерода в сплаве от 0,02% до 2,14%) и чугуны (содержание углерода более 2,14%)
Характеристика сталей
Стали — сплавы железа (Fe) с углеродом (С), с содержанием последнего не более 2,14%. Стали характеризуются достаточно высокой плотностью (7,7 — 7,9 г/см3) и другими физическими величинами:*
- Удельная теплоёмкость при 20°C: 462 Дж/(кг·°C)
- Температура плавления: 1450—1520°C
- Удельная теплота плавления: 84 кДж/кг (20 ккал/кг, 23 Вт·ч/кг)
- Коэффициент линейного теплового расширения при температуре около 20°C: 11,5·10-6 1/°С
- Коэффициент теплопроводности при температуре 100°С: 30 Вт/(м·К)
*Данные характеристики представляют среднее значение. Фактическая величина свойств зависит от содержания углерода и легирующих элементов в стали. Для ее точного определения стоит пользоваться марочниками сталей и сплавов.
На практике используются стали с содержанием углерода не более 1,3%, т.к. при его более высоком содержании увеличивается хрупкость.
Классификация сталей
Стали характеризуются или классифицируются по множеству признаков:
Классификация по химическому составу
- углеродистые стали — классифицируются в зависимости от содержания углерода в %:
- низкоуглеродистые (< 0,25 %C)
- среднеуглеродистые (0,25-0,65 %C)
- высокоуглеродистые (> 0,65 %C)
- легированные стали — классифицируются в зависимости от суммарного содержания легирующих элементов в %:
- среднелегированные (2,5-10 %)
- высоколегированные (> 10 %)
Если содержание Fe меньше 45 %, то это сплав, на основе элемента самого высокого содержания. Если содержание Fe больше 45 %, то это сталь.
Классификация по назначению
- конструкционные – применяются для изготовления деталей машин и механизмов, содержание углерода <0,8%. Конструкционные подразделяются на цементуемые, с содержанием углерода <0,3% и улучшаемые, с содержанием углерода >0,3%. Основную классификацию и группы конструкционных сталей можно посмотреть здесь
- инструментальные – применяются для изготовления мерительного, режущего инструмента, штампов горячего и холодного деформирования. Содержание углерода >0,8%;
- с особыми свойствами: электротехнические, с особыми магнитными свойствами, жаропрочные, износостойкие и др.
Классификация по структуре
Классификация по Обергофферу — по структуре в равновесном состоянии
Изначально эта классификация содержала только 4 типа сталей:
- доэвтектоидные
- эвтектоидные
- заэвтектоидные
- ледебуритные (имеющие в литом состоянии эвтектику)
Позже были внесены дополнения:
- ферритные
- аустенитные
Равновесное состояние — состояние сплава или стали после медленного охлаждения, чаще всего после отжига
Классификация по Гийе — по структуре после нормализации (нагрева и охлаждения на воздухе)
- перлитные
- мартенситные
- ферритные
- аустенитные
- карбидные
Также могут быть смешанные классы: феррито-перлитный, аустенитно-ферритный и т.д.
Классификация сталей по качеству
Количественным показателем качества является содержания вредных примесей- серы и фосфора:
- обыкновенного качества (S≤0,05, P≤0,04)
- качественные стали (S, P ≤0,035)
- высококачественные (S, P ≤0,025)
- особовысококачественные (S≤0,015, P≤0,025)
Классификация по способу выплавки
- в мартеновских печах
- в кислородных конверторах
- в электрических печах: электродуговых, индукционных и др.
Классификация по степени раскисления
- кипящие (кп)
- полуспокойные (пс)
- спокойные (сп)
Расширенные характеристики и свойства (технологические, физические… химический состав) некоторых марок сталей смотрите здесь.
Классификация и маркировка чугунов
Чугунами называют сплавы железа с углеродом, содержащие более 2,14% углерода. Они содержат те же примеси, что и сталь, но в большем количестве.
Классификация чугунов
В зависимости от состояния углерода в чугуне, его подразделяют на следующие виды:
- белый чугун, в котором весь углерод находится в связанном состоянии в виде карбида
Такой чугун может быть доэвтектическими и заэвтектическими, а разделяет их эвтектический чугун (4,31% С). Структура доэвтектического чугуна – перлит, вторичный цементит и ледебурит, заэвтектического – первичный цементит с ледебуритом.
- графитизированный чугун, в котором углерод в значительной степени или полностью находится в свободном состоянии в виде графита, что определяет прочностные свойства сплава. Такие чугуны подразделяют на:
- серые — пластинчатая или червеобразная форма графита (ЧПГ)
- высокопрочные — с шаровидным графитом (ЧШГ)
- ковкие — хлопьевидный графит (ЧХГ)
- чугун с вермикулярным графитом (ЧВГ) — имеет промежуточные свойства между СЧ и ВЧ. По форме графита напоминает СЧ, но имеет более толстые и более короткие пластины с округленными концами
Еще чугуны классифицируются по основе, в которой расположен графит. Основа может быть перлитной, ферритной, феррито-перлитной.
Маркировка чугунов
Чугуны маркируют двумя буквами и двумя цифрами, соответствующими минимальному значению временного сопротивления δв при растяжении в МПа-10. Серый чугун обозначают буквами «СЧ» (ГОСТ 1412-85), высокопрочный — «ВЧ» (ГОСТ 7293-85), ковкий — «КЧ» (ГОСТ 1215-85).
Пример маркировки
СЧ10 — серый чугун с пределом прочности при растяжении 100 МПа;
ВЧ70 — высокопрочный чугун с сигма временным при растяжении 700 МПа;
КЧ35 — ковкий чугун с δв растяжением примерно 350 МПа.
Для работы в узлах трения со смазкой применяют отливки из антифрикционного чугуна АЧС-1, АЧС-6, АЧВ-2, АЧК-2 и др., что расшифровывается следующим образом: АЧ — антифрикционный чугун: С — серый, В — высокопрочный, К — ковкий. А цифры обозначают порядковый номер сплава согласно ГОСТу 1585-79.
Чугуны специального назначения
К этой группе чугунов относятся жаростойкие (ГОСТ 7769—82), жаропрочные и коррозионностойкие (ГОСТ 11849—76) чугуны. Сюда же можно отнести немагнитные, износостойкие и антифрикционные чугуны.
Жаростойкими являются серые и высокопрочные чугуны, легированные кремнием (ЧС5) и хромом (4Х28, 4Х32). Высокой термо- и жаростойкостью обладают аустенитные чугуны: высоколегированный никелевый серый ЧН15Д7 и с шаровидным графитом ЧН15ДЗШ.
К жаропрочным относятся аустенитные чугуны с шаровидным графитом ЧН19ХЗШ и ЧН11Г7Ш.
В качестве коррозионностойких применяют чугуны, легированные кремнием (ферросилиды) — ЧС13, ЧС15, ЧС17 и хромом — 4Х22, 4Х28, 4Х32. Для повышения коррозионной стойкости кремнистых чугунов их легируют молибденом (4С15М4, 4С17МЗ — антихлоры). Высокой коррозионной стойкостью в щелочах обладают никелевые чугуны, например аустенитный чугун 4Н15Д7.
В качестве немагнитных чугунов также применяются аустенитные чугуны.
К износостойким чугунам относятся половинчатые и отбеленные чугуны. К износостойким половинчатым чугунам относится, например, серый чугун марки И4НХ2, легированный никелем и хромом, а также чугуны И4ХНТ, И4Н1МШ (с шаровидным графитом).
heattreatment.ru
Сплавы железа, классификация — Энциклопедия по машиностроению XXL
Классификация металлических сплавов по химическому составу, основанная на указании главного компонента сплава (железо, медь, алюминий и др.), имеет традиционный характер и получила наибольшее распространение. Однако внутри таких классов, определенных с учетом химического состава по главному компоненту сплава, распределение на группы и подгруппы чаще всего проводится по характерным особенностям в свойствах или по области применения данного сплава или нескольких сплавов. [c.145]Существует несколько вариантов классификации сплавов железа. [c.213]
Классификация металлических сплавов по химическому составу, основанная на указании главного компонента сплава (железо, медь, алюминий и т. д.), пригодна лишь для распределения сплавов на небольшое число основных классов. Для дальнейшей характеристики этих многочисленных сплавов внутри каждого из таких классов данная классификация не пригодна. [c.384]
Хромистые сплавы. Свойства высокохромистого чугуна с большим содержанием углерода частично описано в разделе Отливки из жаростойкого чугуна , однако в химическом машиностроении применяются преимущественно высокохромистые сплавы с пониженным содержанием углерода. До сих пор нет единого мнения в классификации высокохромистых сплавов, содержащих более 1% С. По данным работы [57], характерное для чугуна эвтектическое превращение в сплавах, содержащих 35% Сг, наступает при содержании 1,5—2,5% С, а по данным работы [25], сплав, содержащий 20% Сг и более — 0,6% С должен классифицироваться как белый чугун, если применять терминологию, принятую для диаграммы железо—углерод. Бесспорным является то, что эвтектическое превращение в высокохромистых сплавах выявляется при значительно более низком содержании углерода, так как по мере увеличения содержания хрома в железоуглеродистом сплаве растворимость углерода непрерывно уменьшается. [c.225]
Широкое применение получили титановые сплавы, классификация и химический состав которых регламентированы АМТУ 388— 57. В состав сплавов входят ванадий, вольфрам, молибден, марганец, хром, железо, тантал, ниобий. [c.181]
Классификация литейных сплавов на основе железа представлена в табл. 70. [c.214]
Промышленная классификация металлов на две основные группы — черные п цветные сложилась исторически. К черным металлам относят железо и его сплавы (чугун, сталь, ферросплавы). Остальные металлы составляют группу цветных. [c.25]
Все металлы и образованные из них сплавы делят на черные (к ним относят железо и сплавы на его основе, на их долю приходится около 95% производимой в мире металлопродукции) и цветные. В технике принята условная классификация, по которой металлы делят на группы легкие (например, А1, Мд), тяжелые (Си, РЬ и др.), тугоплавкие (Ш, Мо и др.), благородные (Ли, Р1), рассеянные (Об, 1п, Т1), редкоземельные (5с, У), радиоактивные (Еа, О и др.). [c.5]
Исторически сложилась промышленная классификация металлов на две основные группы черные и цветные. К черным металлам относится железо и его сплавы (чугун, сталь, ферросплавы), а также марганец и хром. Все остальные металлы объединены в общую группу цветных, которая в свою очередь подразделяется на легкие (алюминий, магний, титан и др.), тяжелые (медь, никель, свинец, цинк, олово), малые цветные металлы (кобальт, кадмий, молибден, вольфрам, сурьма, ртуть, висмут), благородные (золото, серебро, платина и платиноиды), а также редкие и радиоактивные металлы. [c.10]
В рассматриваемых композитах могут быть использованы самые различные металлы. Классификация в данном случае основана на относительных свойствах матрицы и наполнителя 1) наполнитель тверже матрицы 2) наполнитель мягче матрицы. В первом случае в качестве наполнителя могут быть использованы, например, У, Сг, Мо. Это хрупкие металлы, но они обладают высокой теплостойкостью. Если в качестве матричной фазы воспользоваться металлами с высокой вязкостью, то можно получить жаростойкие композиты с хорошей вязкостью. Во втором случае в качестве наполнителя можно использовать частицы свинца, которые будут рассеяны в железе или медном сплаве. Такой композит обладает хорошей обрабатываемостью. [c.418]
Любой материал, каким бы уникальным он ни был, не является самоценным, а предназначен для изготовления изделия, которое может быть использовано как отдельно, так и в качестве детали более сложного оборудования. Таким образом, материал реализует свои свойства только в качестве компонента оборудования. Современные материалы создаются с заранее заданными свойствами, а следовательно, под конкретное, достаточно узкое назначение. Поэтому наименований и марок материалов очень много. Они собраны и классифицированы в специальных государственных стандартах и справочниках. Поскольку из материалов создается какое-либо изделие, естественно, что в основе классификации чаще всего лежат назначение (например, конструкционные материалы, инструментальные, электротехнические, строительные и т.п.) и/или основные свойства, определяющие область использования (например, магнитные, проводниковые, полупроводниковые, износостойкие, коррозионно-стойкие и др.). Часто классификация строится по химическому составу материала и/или структуре, которые, опять же, определяют в большей степени его дальнейшее применение (например, сплавы на основе железа, алюминия, меди, никеля, титана и других элементов, слюдяные, композитные, полимерные, металлические материалы и т.п.). Различные классификации дополняют друг друга, например классификация по назначению. (конструкционные материалы) включает в себя классификацию по свойству (коррозионно-стойкие материалы), которая, в свою очередь, содержит классификацию по структуре и химическому составу (металлические сплавы на основе [c.540]
Предлагаемая классификация не совпадает с общепринятой, согласно которой под черными металлами подразумеваются железо и его сплавы, а под цветными — все остальные металлы. [c.7]
Настоящая книга представляет собой учебник по термической обработке металлов для машиностроительных техникумов. Для изучения термической обработки по этой книге от учащегося требуется знание основ металловедения в объеме книги А. И. Самохоц-кого и М. П. Кунявского Металловедение или книги М. С. Ароновича и Ю. М. Лахтина Основы металловедения и термической обработки. или книги Б. С. Натапова Металловедение , представляющих собой также учебники для техникумов. Предполагается, что учащийся хорошо знаком с основными типами двойных диаграмм состояния, с кристаллическим строением металлов и сплавов, с элементарными структурами сталей и чугунов, с методикой металлографического исследования и с механическими испытаниями. Эти вопросы в настоящей книге не рассматриваются вовсе. Не рассматривается в настоящей книге и оборудование для термической обработки печи, закалочные баки, закалочные прессы и т. п., так как эти вопросы изучаются в отдельном курсе. В первой главе кратко, но несколько подробнее, чем в упомянутых учебниках по металловедению, рассмотрены классификация и характеристика сталей и диаграмма состояния сплавов железо—углерод. [c.3]
Промышленная классификация металлов, традиционно сложившаяся в нашей стране в период наиболее интенсивной индустриализации, не имеет четкой научной основы, но широко применяется в технической литературе и обиходе. Первое основание ее, принятое и в некоторых других странах, состоит в резколг зазличии масштабов производства железа и прочих металлов. 3 общей массе металлургической продукции, сплавы железа занимают около 93% (см. табл. 1), Поэтому различают железные металлы (железо и его сплавы — чугуны и стали) и прочие нежелезные . [c.17]
Феррооплавами называются сплавы железа с другими элементами, используемые для раскислеиия стали и различных сплавов, а также в качестве легирующего материала. По сложившейся классификации к ферросплавам относят и такие сплавы, в которых содержится относительно не большое количество железа. Ферросплавы производят в доменных и в электрических печах, а также металлотер мическим методом. [c.110]
В зависимости от структуры различают три основных класса нержавеющих сталей. Каждый класс включает ряд сплавов, которые несколько различаются по составу, но обладают сходными физическими, магнитными и коррозионными свойствами. Здесь приводятся обозначения сталей в соответствии с классификацией Американского института железа и стали (AISI), которую часто используют на практике. Перечень основных марок нержавеющих сталей, выпускаемых промышленностью, представлен в табл. 18.2. Основными классами нержавеющих сталей являются мартенситный, ферритный и аустенитный. [c.296]
Химический состав оловянного порошка (241). Гранулометрический состав оловянного порошка (241). Химический состав кобальтового порошка (241). Химический состав электролитического никелевого порошка (241). Химический состав серебряного порошка (242). Гранулометрический состав серебряного порошка (242). Примерное назначение стандартных металлических порошков (242). Классификация метаплокерамических изделий (244). Условное обозначение железографита (247). Физико-механические свойства желе-зографита (247). Примерное назначение железографита (248). Характеристика фрикционных желез ографитовых материалов (249). Физико-механические свойства фрикционных металлокерамических материалов, разработанных ЦНИИТмаш (249). Физико-механические свойства фрикционных металлокерамических сплавов (250). Физико-механические свойства металлокерамических конструкционных материалов (252). Физико-механические свойства металлокера- шческих контактных материалов (253). Технологические режимы изготовления типовых металлокерамических изделий (254). Реншмы токарной обработки металлокерамических изделий (255). [c.536]
Согласно общепринятой классификации железо и сплавы на его основе относятся к черным металлам, а все остальные металлы и сплавы на их основе — кцветным Легирующие элементы металлы можно условно разделить на следующие группы [c.8]
Шуман провел классификацию переходных Ы-, Ad- и 5 -элементов периодической системы элементов по их способности образовывать те или иные кристаллические структуры [52] и предложил гипотезу, согласно которой е-фаза должна образовываться как термодинамически устойчивая фаза при легировании железа элементами с числом внешних электронов 7—9 и атомным радиусом, превосходящим атомный радиус железа, но не более 10%. При этом в областях, окружающих легирующий элемент, должны возникать высокие сжимающие напряжения, приблизительно 1000—1500 МПа на 1% (ат.) легирующего элемента, что и обеспечивает компактное построение ГПУ структуры [52, 53]. Однако эта гипотеза не объясняет возможности существования е-фазы в концентрационном интервале (15—25% Мп). Кроме того, среди переходных 4й-элемен-тов марганец имеет аномально больщой атомный радиус и несколько нарушает закономерность, установленную Шуманом для элементов 5 и 6-го периодов, однако, в сплаве с железом марганец относится к группе элементов, стабилизирующих е-фазу при нормальном давлении [53]. [c.36]
Фазовый состав и микроструктура титановых сплавов изменяются в зависимости от содержания и соотношения легирующих элементов. Основой микроструктуры титановых сплавов являются твердые растворы а- и р-титана. Количественное соотношение между этими фазами в отожженном состоянии определяет классификацию титановых сплавов, которые подразделяют на а- и р-сплавы, псевдо-а- и псевдо-р-сплавы, двухфазные а+р-сплавы [294], На изменение количественного соотношения а- и р-фаз существенно влияет легирование (имеются элементы -стабилизаторы, например алюминий, и р-стабйлизаторы — молибден, ванадий, хром, железо и др.) и термическая обработка. При охлаждении с определенных температур нагрева возможно зафиксировать при комнатной температуре метастабильные фазы р, а или а». Характерная особенность а- и сх-Нр-сплавов — резкое укрупнение микроструктуры при переходе в р-область. Этот процесс слабее проявляется в высоколегированных р-сплавах [294, 295]. [c.180]
Усталостное нагружение более многофакторное, чем статическое деформирование и задача классификации дислокационных структур еще более усложняется. При напряжениях, близких к пределу выносливости, на стадии деформационного упрочнения в ОЦК-металлах и сплавах наблюдались самые различные дислокационные субструктуры [11, 14, 17, 24, 39, 32, 48-51], Отдельные изолированные сплетения дислокации (железо, плоский симметричный изгиб), плотные скопления, вытянутые клубки, геликоиды и ряды петель (железо, растяжение-сжатие), сплетения дислокации, отдельные почти прямые сегменты дислокационных границ (moho- и поликристаллическое железо, растяжение-сжатие), ряды дислокации и отдельные дислокации петлевого и геликоидального типов (железо, симметричный изгиб), спектр дислокационных структур -от отдельных скоплений дислокации до ячеистой и полосовой структур (железо, повтор- [c.84]
Создание различных сплавов на основе титана было обусловлено требованиями, которые выдвигали перед новым конструкционным материалом различные отрасли промышленности. В основу классификации титановых сплавов положено влияние леги-РЗ Ющих элементов на температуру аллотропического превращения титана. Элементы, повышающие температуру аллотропического превращения титана и тем самым расширяющие область существования а-фазы, называют а-стабилизаторами титана (алюминий, углерод, азот, кислород) понижающие ее — Р-стаби-лизаторами (ванадий, молибден, хром, железо, медь, марганец, водород, ниобий, тантал, серебро, золото и др.), а элементы, мало влияющие на эту температуру, — нейтральными упрочните-лями (олово, цирконий, германий и др.). В зависимости от природы и количества легирующих элементов можно получить три типа титановых сплавов а, а + Р и р-сплавы. Из исследуемых титановых сплавов ВТ1-1 и ВТ5 относятся к а-сплавам, а ВТ6 к а-ьр-сплаБам. [c.26]
Существует несколько систем классификации металлов и сплавов. Наиболее простой и естественной является классификация по основному эгементу железные сплавы медные сплавы алюминиевые сплавы магниевые сплавы титановые сплавы никелевые сплавы цинковые сплавы и т. д. Железо и железные сплавы иначе называют черными металлами, все остальные простые металлы и их сплавы — цветными металлами. [c.17]
Все металлы и образованные из них сплавы делят на черные (к ним относят железо и сплавы на его основе, на их долю приходится около 957о производи мой в мире металлопродукции) и цветные или, точ нее, нежелезные. Большое число нежелезных металлов и широкий диапазон их свойств не позволяют классифи цировать их по какому-либо единому признаку. В тех нике принята условная классификация, по которой ме таллы делят на группы легкие (например, А1, Mg) тяжелые (Си, РЬ и др.), тугоплавкие ( У, Мо и др.) благородные (Аи, Р1), рассеянные (0(1, Лп, Т1), редко земельные (5с, V, 2а), радиоактивные (Ка, и и др.) [c.5]
Четвертый — ферритный — класс классификации по структуре в равновесном состоянии совершенно совпадает с таким же классом по классификации Гийе область его также располагается в левом верхнем углу диаграммы, т. е. отвечает минимальному содержанию углерода при высоком количестве легирующего элемента, расширяющего область а-железа (феррита.) В таких сплавах, независимо от скорости охлаждения, получается зернистая структура легированного феррита, не имеющего превращений в твердом состоянии. [c.295]
Наблюдая момент изменения какого-нибудь из свойств металла, можно определить точку кристаллизации (плавления) металла. Помимо кристаллизации или плавления в чистых металлах возможны еще и превращения в твердом состоянии, к-рые состоят в переходе от одного типа расположения атомов в пространстве к другому и к-рые также сопровождаются скачками в изменении всех свойств. Такого рода превращения обычно называют аллотропическими. Из чистых металлов железо, кобальт, марганец 1 >лово имеют по несколько аллотропич. форм. Для чистых металлов характерно протекание всякого превращения при строго постоянной темп-ре, что обусловлено общим законом равновесия — правилом фаз. В сплавах двух металлов явления значительно сложнее и разнообразнее. Т. к. характер явлений, наблюдаемых при изменении темп-ры, в случае сплавов определяется тем, в какие взаимоотношения вступили при сплавлении компоненты, то надо прежде всего остановиться на классификации и характеристике типов взаимоотношения компонентов. Известны следующие основные случаи взаимоотношений компонентов 1) два компонента не смешиваются или смешиваются лишь частично в жидком состоянии 2) компоненты дают однородный жидкий сплав или раствор, к-рый при кристаллизации переходит в однородный твердый кристаллический раствор 3) компоненты дают однородный жидкий раствор, который при кристаллизации распадается на смесь двух видов кристаллических твердых растворов 4) компоненты образуют новое [c.376]
К высоколегированным сталям относят сплавы на основе железа, содержащие более 8—10% легирующих элементов. Озгласно ГОСТу 5632—71 наибольшую группу составляют нержавеющие стали и сплавы, легированные хромом, никелем, молибденом, кремнием, марганцем, титаном, ниобием, алюминием и другими элементами. В зависимости от степени легирования изменяются структурный состав и свойства сталей, в частности их свариваемость. Обилие марок сталей послужило поводом для их классификации по таким признакам, как структурный состав, процентное содержание хрома или никеля, область применения (коррозионностойкие, жаропрочные, высокопрочные и т. п.). В табл. 1.14 приведены наиболее распространенные марки высоколегированных сталей, применяемых в сварных конструкциях. [c.347]Две схемы КУ стоят в классификации конструктивных схем и способов достижения герметичности отдельно конструкция с расплавляемым (запаянным) контактом (схема 24) и конструкция с жидкостным уплотнением (схема 25). Герметизирующей средой в первой из них служат металлы, обладающие смачивающей способностью по отношению к материалу перекрывающего клапана. Выбор металла зависит от температуры прогрева при вакуумировании. Могут использоваться сплав Вуда, олово, золото, серебро, индий, медь — иногда с добавкой порощ-ка железа, никеля. Во второй схеме в качестве перекрывающей среды обычно используют ртуть. Эта схема находит применение в непрогреваемых системах низкого вакуума. [c.14]
mash-xxl.info
Классификация железоуглеродистых сплавов
В зависимости от концентрации углерода железоуглеродистые сплавы подразделяют на технически чистое железо, стали и чугуна.
а б в г
Рис. 6.12. Схемы структур чистого железа (а), доэвтектоидной (б),
эвтектоидной (в) и заэвтектоидной (г) стали
1. К технически чистому железу относят сплавы, содержащие не более 0,02% С. Под микроскопом структура технически чистого железа (рис.6.12,а) состоит из однородных зерен феррита и возможно с отдельными частицами третичного цементита по их границам.
2. К сталям относят сплавы, содержащие углерод в пределах от 0,02 до 2,14%. По своему положению на диаграмме они подразделяются на доэвтектоидные, заэвтектоидные, а при содержании углерода 0,8% сталь называют эвтектоидной.
Поскольку сравнительно малые изменения содержания углерода весьма ощутимо изменяют структуру, прочностные характеристики и технологичность стали, то по содержанию углерода различают:
а) низкоуглеродистые, содержащие углерода 0,25% и менее;
б) среднеуглеродистые, содержащие углерода 0,30-0,65%;
в) высокоуглеродистые, содержащие углерода 0,7% и более.
3. К чугунам относят сплавы, содержащие более 2,14% С. Они могут быть доэвтектическими и заэвтектическими, а разделяет их эвтектический чугун (4,31% С). Структура доэвтектического чугуна – перлит, вторичный цементит и ледебурит, заэвтектического – первичный цементит с ледебуритом. Чугуны с такой структурой называют белыми. Они тверды, хрупки и очень трудно обрабатываются резанием. Поэтому производятся для последующей переделки.
В технике чугуны применяют широко, прежде всего, за их превосходные литейные свойства. Цементит легко диссоциирует с образованием графита. Присутствие в структуре графита делает чугун серым и, что крайне важно, технологичным при обработке резанием. Графит может быть пластичным, хлопьевидным и глобулярным. В определении прочностных свойств серого чугуна форма графитных включений и их размеры играют решающее значение. Так, пластинчатый графит, образуя надрезы в металлической основе, резко снижает прочность и пластичность. Только поэтому получаемый литьем обычный серый чугун с пластинчатым графитом очень хрупок.
Ковкий чугун, получаемый длительным отжигом отливок из белого чугуна, имеет хлопьевидный графит, обеспечивающий ему достаточно высокую пластичность (табл. 6.3).
В результате модифицирования удается получить отливки чугуна с глобулярным графитом. Такой чугун называют высокопрочным. Он соединяет в себе присущую чугунам технологичность в литье и обработке резанием с прочностными свойствами стали, заменяя успешно стальные отливки, поковки и цветные сплавы.
Таблица 6.3
Марки и механические свойства некоторых чугунов
Марка чугуна | σв, кгс/мм2 | σ0,2, кгс/мм2 | σ,% | σизг, кгс/мм2 | Стрела прогиба, мм | аn, кгм/см2 | НВ |
СЧ 12-28 | 12 | – | – | 28 | 2 | – | 143–229 |
СЧ 44-64 | 44 | – | – | 64 | 3 | – | 229–289 |
КЧ 37-12 | 37 | – | 12 | – | – | – | 163 |
КЧ 63-2 | 63 | – | 2 | – | – | – | 269 |
ВЧ 33-17 | 38 | 24 | 17 | – | – | 6 | 140–170 |
ВЧ 120-4 | 120 | 90 | 4 | – | – | 3 | 302–369 |
Постоянные примеси в углеродистой стали
Примесные элементы содержатся в стали всегда. Одни из них (фосфор, сера, кислород, азот и водород) попадают в сталь из пихтовых материалов, топлива, огнеупоров, газов и присутствуют там в малом количестве, поскольку избавиться от них окончательно не удается. Другие (марганец, кремний) вводятся преднамеренно в процессе варки стали, как раскислители.
Фосфор попадает из руд. Он, растворяясь в железе в количестве до 0,1%, резко ухудшает пластичность стали, вызывая хладноломкость, поскольку образует с железом очень хрупкий фосфид – Fe3P. Даже при содержании всего 0,05% в виду склонности ликвировать, образует участки высокой концентрацииP, которые опасно охрупчивают сталь. При варке стали, фосфор стремятся возможно полнее отшлаковать известью, что осуществимо лишь при основной футеровке сталеплавильных печей.
Сера переходит в металл из минеральной составляющей топлива. Она почти не растворима в железе и образует с ним хрупкое химическое соединение – сульфид железа. Его частицы придают стали хладноломкость. Сульфид железа с железом способны образовать хрупкую и легкоплавкую сульфидную эвтектику (FeS+Fe) с точкой плавления 988 °C. В присутствии кислорода эвтектика становится еще более легкоплавкой. При температурах горячей обработки давлением эта эвтектика, располагающаяся по границам зерен, плавится, нарушая сплошность металла, вызывая появление трещин, что называют красноломкостью.
Серу отшлаковывают с помощью марганца. Его вводят в сталь перед разливкой в количестве, в пять раз большем предполагаемого содержания серы. По реакции замещения (FeS+Mn=Fe+MnS) марганец восстанавливает железо и образует сульфид марганца с точкой плавления 1610 °С. Его частички, обладая малым удельным весом, легко переходят в шлак. Избыток марганца при этом остается в стали в качестве постоянной примеси.
Кислород, азот и водород могут содержаться в стали в сравнительно малом количестве. Находясь в твердой стали,все они могут быть растворенными в феррите, присутствовать в виде частиц окислов, нитридов и гидридов или в свободном состоянии, заполняя микронесплошности. Все это сильно охрупчивает сталь.
От кислорода избавляются раскислением стали перед разливкой ее в изложницу кремнием, который образует при этом легко переходящую в шлак окись кремния –SiO2. А избыток кремния остается в стали, как постоянная примесь.
Содержание серы и фосфора, как вредных примесей, ухудшающих качество стали, ГОСТ оговаривает:
а) в стали обыкновенного качестваS0,05%,P0,05%;
б) в качественной сталиS0,04%,P0,04%;
в) в высококачественной сталиS0,03%,P0,025%.
Конструкционные стали обыкновенного качества
В производстве машин, станков и предметов широкого потребления в энергетике, на транспорте и в строительной индустрии широко используется горячий стальной прокат в виде прутков, полос, труб, уголков и других фасонных профилей.
Стали маркируются сочетанием букв Ст и цифрой (от 0 до 6), показывающей номер марки, а не среднее содержание углерода в ней, хотя с повышением номера содержание углерода в стали увеличивается. Стали групп Б и В имеют перед маркой буквы Б и В, указывающие на их принадлежность к этим группам. Группа А в обозначении марки стали не указывается. Степень раскисления обозначается добавлением индексов: в спокойных сталях – сп, в полуспокойных – пс, кипящих – кп, а категория нормируемых свойств (кроме категории 1) указывается последующей цифрой. В их составе разное содержание кремния: спокойные – 0,12–0,30, полуспокойные – 0,05–0,17, кипящие меньше 0,07, например Ст3сп, БСт3пс или ВСт3сп5 (в конце 5-я категория). Спокойными и полуспокойными производят стали Ст1–Ст6, кипящими – Ст1–Ст4 всех трех групп. Сталь Ст0 по степени раскисления не разделяют.
Стали группы А поставляются с гарантированными механическими свойствами (табл. 6.4), без указания химического состава.
Таблица 6.4
Механические свойства углеродистых сталей обыкновенного
качества группы А (образцы толщиной до 20 мм)
Сталь | σв, МПа | σ0,2,кгс/мм2 | σ,% | Сталь | σв,МПа | σ0,2,кгс/мм2 | σ,% |
Не менее | Не менее | ||||||
Ст.0 | >310 | – | 23 | Ст.4 | 420–540 | 240–270 | 24 |
Ст.1 | 320–420 | – | 34 | Ст.5 | 500–640 | 260–290 | 20 |
Ст.2 | 340–440 | 200–230 | 32 | Ст.6 | 600 | 320 | 13 |
Ст.3 | 380–490 | 210–250 | 27 |
Примечание. Механические свойства приведены для спокойных и полуспокойных сталей. В сталях Ст.1кп значение σв, на 10-20 МПа и σ на 10 МПа меньше, а значение σ на 1% больше, чем в спокойных и полуспокойных сталях того же номера.
Из табл. 3.4 следует, что с увеличением номера марки прочность увеличивается, а пластичность стали соответственно уменьшается.
Стали группы А используются в состоянии поставки для изделий изготовление которых не сопровождается горячей обработкой. В этом случае они сохраняют структуру нормализации и механические свойства, гарантируемые стандартом.
Стали группы Б поставляют с гарантированным химическим составом, но механические свойства не гарантируются. Стали этой группы применяют для изделий, изготавливаемых с применением горячей обработки (ковка, сварка и в отдельных случаях термическая обработка), при которой исходная структура и механические свойства не сохраняются. Для таких сталей важны сведения о химическом составе, необходимые для определения режима горячей обработки.
Стали группы В поставляются с гарантированными механическими свойствами и химическим составом. Стали группы В дороже, чем стали групп А и Б, их применяют для ответственных деталей (для производства сварных конструкций). В этом случае важно знать исходные механические свойства стали, так как они сохраняются неизменными на участках, не подвергаемых нагреву при сварке. Для оценки свариваемости важны ведения о химическом составе. Механические свойства на растяжение для каждой марки стали группы В соответствуют нормам для аналогичных марок стали группы А (табл. 6.4), а химический состав – нормам для тех же номеров марок группы Б (табл. 6.5). Например, сталь ВСт4сп имеет механические свойства на растяжение, аналогичные стали Ст4сп, а химический состав одинаковый со сталью БСт4сп.
Таблица 6.5
Химический состав (%) углеродистой стали
обыкновенного качества группы Б
Сталь | С | Mn | Siв сталях | S | P | ||
кп | пс | сп | не более | ||||
БСт0 | < 0,23 | – | – | – | – | 0,06 | 0,07 |
БСт1 | 0,06–0,12 | 0,25–0,5 | 0,05 | 0,05–0,17 | 0,12–0,3 | 0,05 | 0,04 |
БСт2 | 0,09–0,15 | 0,25–0,5 | 0,05 | 0,05–0,17 | 0,12–0,3 | 0,05 | 0,04 |
БСт3 | 0,14–0,22 | 0,30–0,65 | 0,07 | 0,05–0,17 | 0,12–0,3 | 0,05 | 0,04 |
БСт4 | 0,18–0,27 | 0,40–0,70 | 0,07 | 0,05–0,17 | 0,12–0,3 | 0,05 | 0,04 |
БСт5 | 0,28–0,37 | 0,50–0,80 | – | 0,05–0,17 | 0,15–0,35 | 0,05 | 0,04 |
БСт6 | 0,38–0,49 | 0,50–0,80 | – | 0,05–0,17 | 0,15–0,35 | 0,05 | 0,04 |
Примечание. 1. В сталях БСт1-БСт6 допускается не более 0,3% Cr; 0,3% Ni; 0,3% Cu; 0,08% As; 0,08% N. 2. В сталях, выплавленных из керченских руд, допускается до 0,15% As и 0,05% P.
Углеродистые стали обыкновенного качества (всех трех групп) предназначены для изготовления различных металлоконструкций, а также слабонагруженных деталей машин и приборов. Эти стали используются, когда работоспособность деталей и конструкций обеспечивается жесткостью.
В машиностроении применяют углеродистые качественные стали, поставляемые по ГОСТ 1050-88. Содержание серы и фосфора в них допускается в пределах 0,03-0,04% каждого из элементов. Маркируются эти стали двузначными цифрами 05,08, 10, 15, 20, …, 75,80,85, обозначающими среднее содержание углерода в сотых долях процента. Например, сталь 20 содержит в среднем 0,20% С, сталь 75 – 0,75% С и т.д.
К углеродистым сталям также относят стали с повышенным содержанием марганца (0,7–1,0%) марок 15Г, 20Г, 25Г, …, 70 Г, имеющих повышенную прокаливаемость (критический диаметр до 25–30 мм). В табл. 3.4 приведены гарантируемые механические свойства после нормализации углеродистых качественных сталей.
Данные в табл. 6.6 служат для контроля металлургического качества отдельных плавок, а механические свойства изделий будут определяться соответствующими режимами термической обработки, зависящими от размера и сечения деталей.
Спокойные стали маркируются без индекса, полуспокойные и кипящие – с индексом соответственно псикп. В табл. 6.4 приведены данные химического состава и свойств спокойных сталей. Кипящие стали производят марок 05кп, 08кп, 10кп, 15кп, 20кп, полуспокойные – 08пс, 10пс, 15пс, 20пс.
Таблица 6.6
Химический состав и механические свойства
углеродистых качественных сталей
Марка стали | Содержание углерода, % | Хром, не более | Механические свойства, не менее | |||||
σв,Мпа | στ,Мпа | δ, % | Ψ,% | KCU+20 МДж/м2 | НВ после отжига или высокого отпуска, не более | |||
08 | 0,05–0,01 | 0,10 | 330 | 200 | 33 | 60 | – | 131 |
10 | 0,07–0,14 | 0,15 | 340 | 210 | 31 | 55 | – | 143 |
15 | 0,12–0,19 | 0,25 | 380 | 230 | 27 | 55 | – | 149 |
20 | 0,17–0,24 | 0,25 | 420 | 250 | 25 | 55 | – | 163 |
30 | 0,27–0,35 | 0,25 | 500 | 300 | 21 | 50 | 0,8 | 179 |
40 | 0,37–0,45 | 0,25 | 580 | 340 | 19 | 45 | 0,6 | 217 |
50 | 0,47–0,55 | 0,25 | 640 | 380 | 14 | 40 | 0,4 | 241 |
60 | 0,57–0,65 | 0,25 | 690 | 410 | 12 | 35 | – | 255 |
70 | 0,67–0,75 | 0,25 | 730 | 430 | 9 | 30 | – | 269 |
Качественные стали широко применяются в машиностроении и приборостроении, так как за счет разного содержания углерода в них, а соответственно и термической обработки можно получить широкий диапазон механических и технологических свойств.
К чугунам относят сплавы, содержащие более 2,14% С. Они могут быть доэвтектическими и заэвтектическими, а разделяет их эвтектический чугун (4,31% С). Структура доэвтектического чугуна – перлит, вторичный цементит и ледебурит, заэвтектического – первичный цементит с ледебуритом. Чугуны с такой структурой называют белыми. Поэтому производятся для последующей переделки.
В технике чугуны применяют широко, прежде всего, за их превосходные литейные свойства. Цементит легко диссоциирует с образованием графита. Присутствие в структуре графита делает чугун серым и, что крайне важно, технологичным при обработке резанием. Графит может быть пластичным, хлопьевидным и глобулярным. В определении прочностных свойств серого чугуна форма графитных включений и их размеры играют решающее значение. Так, пластинчатый графит, образуя надрезы в металлической основе, резко снижает прочность и пластичность. Только поэтому получаемый литьем обычный серый чугун с пластинчатым графитом очень хрупок.
Ковкий чугун, получаемый длительным отжигом отливок из белого чугуна, имеет хлопьевидный графит, обеспечивающий ему достаточно высокую пластичность (табл. 6.7).
В результате модифицирования удается получить отливки чугуна с глобулярным графитом. Такой чугун называют высокопрочным. Он соединяет в себе присущую чугунам технологичность в литье и обработке резанием с прочностными свойствами стали, успешно заменяя стальные отливки, поковки и цветные сплавы.
Таблица 6.7
Химический состав и механические свойства некоторых марок чугунов
Марка чугуна | σв, кгс/мм2 | σ0,2, кгс/мм2 | σ,% | σизг, кгс/мм2 | Стрела прогиба, мм | аn, кгм/см2 | НВ |
СЧ 12-28 | 12 | – | – | 28 | 2 | – | 143–229 |
СЧ 44-64 | 44 | – | – | 64 | 3 | – | 229–289 |
КЧ 37-12 | 37 | – | 12 | – | – | – | 163 |
КЧ 63-2 | 63 | – | 2 | – | – | – | 269 |
ВЧ 33-17 | 38 | 24 | 17 | – | – | 6 | 140–170 |
ВЧ 120-4 | 120 | 90 | 4 | – | – | 3 | 302–369 |
Механические свойства серого чугуна зависят от свойств металлической основы и ее количества, формы и размеров графитных включений (пустот).
Марка серого чугуна состоит из букв Сч (серый чугун) и цифры, показывающей значение временного сопротивления при растяжении (кгс/мм2). Показателями механических свойств серых чугунов в соответствии с ГОСТ 1412-85 является прочность при статическом растяжении (табл. 6.8).
Таблица 6.8
Механические свойства серых чугунов
Чугун | НВ | Структура металлической основы | |
Сч15 | 150 | 163-229 | Феррит |
Сч25 | 250 | 180-250 | Феррит + перлит |
Сч40 | 400 | 207-285 | Перлит |
Сч45 | 450 | 229-289 | Перлит |
Графит способствует измельчению стружки при обработке резанием и оказывает смазывающее действие, что повышает износостойкость чугуна. Номенклатура отливок из серого чугуна и их масса разнообразны: от деталей в несколько граммов до 100 т и более.
Ферритные серые чугуны марки Сч10, Сч15 используются для слабо- и средненагруженных деталей: крышки, фланцы, маховики, суппорты, тормозные барабаны, диски сцепления и т.д.
Ферритно-перлитные серые чугуны марки Сч20, Сч25 применяются для деталей, работающих при повышенных статистических и динамических нагрузках: картеры двигателя, поршни цилиндров, барабаны сцепления, станины станков и другие отливки разного назначения.
Перлитный чугун применяют для отливки станин мощных станков и механизмов. Часто используют перлитные серые модифицированные чугуны. Такие чугуны получают при добавлении в жидкий чугун перед разливкой специальных добавок – ферросилиция (0,3-0,6% от массы шихты). К таким чугунам относятся СЧ40 и СЧ45, которые обладают более высокими механическими свойствами из-за измельчения формы графитных включений. Эти марки чугунов применяются для корпусов насосов, компрессоров и гидроприводов.
Для деталей, работающих при повышенных температурах, применяют легированные серые чугуны, которые дополнительно содержат хром, никель, молибден и алюминий.
studfile.net
Диаграмма состояния сплавов железо-углерод — Википедия
Диагра́мма фа́зового равнове́сия (диаграмма состоя́ния) желе́зо—углеро́д (иногда эту диаграмму называют «диаграмма железо—цементит») — графическое отображение фазового состояния сплавов железа с углеродом в зависимости от их химического состава и температуры.
Железо образует с углеродом химическое соединение Fe3C цементит. Так как на практике применяют металлические сплавы на основе железа с содержанием углерода до 5 %, практически интересна часть диаграммы состояния от чистого железа до цементита[1]. Поскольку цементит — метастабильная фаза, то и соответствующая диаграмма называется метастабильной (сплошные линии на рисунке).
Для серых чугунов и графитизированных сталей рассматривают стабильную часть диаграммы железо—графит (Fe—Гр), поскольку именно графит является в этом случае стабильной фазой. Цементит выделяется из расплава намного быстрее графита и во многих сталях и белых чугунах может существовать достаточно долго, несмотря на метастабильность. В серых чугунах графит существует обязательно.
На рисунке тонкими пунктирными линиями показаны линии стабильного равновесия (то есть с участием графита), там где они отличаются от линий метастабильного равновесия (с участием цементита), а соответствующие точки обозначены штрихом. Обозначения фаз и точек на этой диаграмме приведены согласно неофициальному международному соглашению.
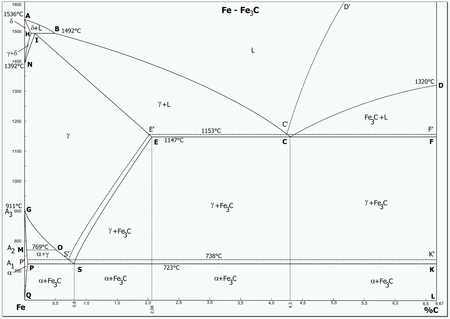
В системе железо — углерод существуют следующие фазы: жидкая фаза, феррит, аустенит, цементит, графит.
Жидкая фаза. В жидком состоянии железо хорошо растворяет углерод в любых пропорциях[источник не указан 853 дня] с образованием однородной жидкой фазы.
Феррит — Твёрдый раствор внедрения углерода в α-железе с объёмно-центрированной кубической решёткой.
Феррит имеет переменную, зависящую от температуры предельную растворимость углерода: минимальную — 0,006 % при комнатной температуре (точка Q), максимальную — 0,02 % при температуре 700 °C (точка P). Атомы углерода располагаются в центре грани или (что кристаллогеометрически эквивалентно) на середине рёбер куба, а также в дефектах решетки[2].
При температуре выше 1392 °C существует высокотемпературный феррит с предельной растворимостью углерода около 0,1 % при температуре около 1500 °C (точка H).
Свойства феррита близки к свойствам чистого железа. Он мягок (твёрдость по Бринеллю — 130 НВ) и пластичен, ферромагнитен (при отсутствии углерода) до точки Кюри — 770 °C.
Аустенит (γ) — твёрдый раствор внедрения углерода в γ-железе с гранецентрированной кубической решёткой.
Атомы углерода занимают место в центре гранецентрированной кубической ячейки. Предельная растворимость углерода в аустените — 2,14 % при температуре 1147 °C (точка Е). Аустенит имеет твёрдость 200—250 НВ, пластичен, парамагнитен. При растворении других элементов в аустените или в феррите изменяются свойства и температурные границы их существования[3].
Цементит (Fe3C) — химическое соединение железа с углеродом (карбид железа), со сложной ромбической решёткой, содержит 6,67 % углерода. Он твёрдый (свыше 1000 HВ), и очень хрупкий. Цементит — метастабильная фаза и при длительном нагреве самопроизвольно разлагается с выделением графита.
В железоуглеродистых сплавах цементит как фаза может выделяться при различных условиях:
- цементит первичный (выделяется из жидкости),
- цементит вторичный (выделяется из аустенита),
- цементит третичный (из феррита),
- цементит эвтектический и
- эвтектоидный цементит.
Цементит первичный выделяется из жидкой фазы в виде крупных пластинчатых кристаллов. Цементит вторичный выделяется из аустенита и располагается в виде сетки вокруг зёрен аустенита (после эвтектоидного превращения они станут зёрнами перлита). Цементит третичный выделяется из феррита и в виде мелких включений располагается у границ ферритных зёрен[4].
Эвтектический цементит наблюдается лишь в белых чугунах. Эвтектоидный цементит имеет пластинчатую форму и является составной частью перлита. Цементит может при специальном сфероидизируюшем отжиге или закалке с высоким отпуском выделяться в виде мелких сфер. Влияние на механические свойства сплавов оказывает форма, размер, количество и расположение включений цементита, что позволяет на практике для каждого конкретного применения сплава добиваться оптимального сочетания твёрдости, прочности, стойкости к хрупкому разрушению и т. п.[5]
Графит — фаза состоящая только из углерода со слоистой гексагональной решёткой. Плотность графита (2,3 г/см3) много меньше плотности всех остальных фаз (около 7,5—7,8 г/см3) и это затрудняет и замедляет его образование, что и приводит к выделению цементита при более быстром охлаждении. Образование графита уменьшает усадку при кристаллизации, графит выполняет роль смазки при трении, уменьшая износ, способствует рассеянию энергии вибраций.
Графит имеет форму крупных крабовидных (изогнутых пластинчатых) включений (обычный серый чугун) или сфер (высокопрочный чугун).
Графит обязательно присутствует в серых чугунах и их разновидности — высокопрочных чугунах. Графит присутствует также и в некоторых марках стали — в так называемых графитизированных сталях.
Линия ACD — это линия ликвидуса, показывающая температуры начала затвердевания (конца плавления) сталей и белых чугунов. При температурах выше линии ACD — жидкий сплав. Линия AECF — это линия солидуса, показывающая температуры конца затвердевания (начала плавления).
По линии ликвидуса АС (при температурах, отвечающих линии АС) из жидкого сплава кристаллизуется аустенит, а по линии ликвидуса CD — цементит, называемый первичным цементитом. В точке С при 1147 °С и содержании 4,3 % углерода из жидкого сплава одновременно кристаллизуется аустенит и цементит первичный, образуя эвтектику, называемую ледебуритом. При температурах, соответствующих линии солидуса AE, сплавы с содержанием углерода до 2,14 % окончательно затвердевают с образованием структуры аустенита. На линии солидуса EC (1147° С) сплавы с содержанием углерода от 2,14 до 4,3 % окончательно затвердевают с образованием эвтектики ледебурита. Так как при более высоких температурах из жидкого сплава выделялся аустенит, следовательно, такие сплавы после затвердевания будут иметь структуру аустенит + ледебурит.
На линии солидуса CF (1147 °С) сплавы с содержанием углерода от 4,3 до 6,67 % окончательно затвердевают также с образованием эвтектики ледебурита. Так как при более высоких температурах из жидкого сплава выделялся цементит (первичный), следовательно, такие сплавы после затвердевания будут иметь структуру — первичный цементит + ледебурит[6].
В области ACEA, между линией ликвидуса AC и солидуса AEC, будет жидкий сплав + кристаллы аустенита. В области CDF, между линией ликвидуса CD и солидуса CF, будет жидкий сплав + кристаллы цементита (первичного). Превращения, протекающие при затвердевании сплавов, называют первичной кристаллизацией. В результате первичной кристаллизации во всех сплавах с содержанием углерода до 2,14 % образуется однофазная структура — аустенит. Сплавы железа с углеродом, в которых в результате первичной кристаллизации в равновесных условиях получается аустенитная структура, называют сталями.
Сплавы с содержанием углерода более 2,14 %, в которых при кристаллизации образуется эвтектика ледебурит, называют чугунами. В рассматриваемой системе практически весь углерод находится в связанном состоянии, в виде цементита. Излом таких чугунов светлый, блестящий (белый излом), поэтому такие чугуны называют белыми[4].
В железоуглеродистых сплавах превращения происходят также и в твердом состоянии, называемые вторичной кристаллизацией и характеризуемые линиями GSE, PSK, PQ. Линия GS показывает начало превращения аустенита в феррит (при охлаждении). Следовательно, в области GSP будет структура аустенит + феррит.
Линия SE показывает, что с понижением температуры растворимость углерода в аустените уменьшается. Так, при 1147 °С в аустените может раствориться углерода 2,14 %, а при 727°С — 0,8 %. С понижением температуры в сталях с содержанием углерода от 0,8 до 2,14 % из аустенита выделяется избыточный углерод в виде цементита, называемого вторичным. Следовательно, ниже линии SE (до температуры 727°С) сталь имеет структуру: аустенит + цементит (вторичный). В чугунах с содержанием углерода от 2,14 до 4,3 % при 1147 °С, кроме ледебурита, есть аустенит, из которого при понижении температуры тоже будет выделяться вторичный цементит. Следовательно, ниже линии EC (до температуры 727 °С) белый чугун имеет структуру: ледебурит + аустенит + цементит вторичный.
Линия PSK (727° С) — это линия эвтектоидного превращения. На этой линии во всех железоуглеродистых сплавах аустенит распадается, образуя структуру, представляющую собой механическую смесь феррита и цементита и называемую перлитом. Ниже 727°С железоуглеродистые сплавы имеют следующие структуры.
- Стали, содержащие углерода менее 0,8 %, имеют структуру феррит + перлит и называются доэвтектоидными сталями.
- Сталь с содержанием углерода 0,8 % имеет структуру перлита и называется эвтектоидной сталью.
- Стали с содержанием углерода от 0,8 до 2,14 % имеют структуру цементит + перлит и называются заэвтектоидными сталями.
- Белые чугуны с содержанием углерода от 2,14 до 4,3 % имеют структуру перлит + вторичный цементит + ледебурит и называются доэвтектическими чугунами.
- Белый чугун с содержанием углерода 4,3 % имеет структуру ледебурита и называется эвтектическим чугуном.
- Белые чугуны с содержанием углерода от 4,3 до 6,67 % имеют структуру цементит первичный + ледебурит и называются заэвтектическими чугунами[5].
Линия PQ показывает, что с понижением температуры растворимость углерода в феррите уменьшается от 0,02 % при 727 °С до 0,006 % при комнатной температуре. При охлаждении ниже температуры 727° С из феррита выделяется избыточный углерод в виде цементита, называемого третичным. В большинстве сплавов железа с углеродом третичный цементит в структуре можно не учитывать из-за весьма малых его количеств. Однако в низкоуглеродистых сталях в условиях медленного охлаждения третичный цементит выделяется по границам зерен феррита (рис. 76). Эти выделения уменьшают пластические свойства стали, особенно способность к холодной штамповке[5].
- ↑ Кузьмин, 1971, с. 91.
- ↑ Циммерман, 1982, с. 31.
- ↑ Циммерман, 1982, с. 33.
- ↑ 1 2 Кузьмин, 1971, с. 93.
- ↑ 1 2 3 Кузьмин, 1971, с. 95.
- ↑ Кузьмин, 1971, с. 92.
- Кузьмин Б. А., Самохоцкий А. И., Кузнецова Т. Н. Металлургия, металловедение и конструкционные материалы. — Москва: Высшая школа, 1971. — 352 с.
- Циммерман Р., Гюнтер К. Металлургия и материаловедение. — Справ. издание. Пер. с нем.. — Москва: Металлургия, 1982. — 480 с.
ru.wikipedia.org
Стали и сплавы на основе железа
Сталь – это основной материал, широко применяемый в машино-, приборо- и авиастроении, строительстве, а также для изготовления различных инструментов. Этот материал отличается сравнительно низкой стоимостью, производится в больших количествах и обладает комплексом механических, физико-химических и технологических свойств. Стали классифицируются по химическому составу, назначению, качеству, степени раскисления и структуре.
Классификация сталей по химическому составу. По химическому составу стали подразделяют на углеродистые и легированные.
Стали, свойства которых в основном зависят от содержания углерода, называют углеродистыми. Углеродистые стали, в свою очередь, классифицируют по содержанию в них углерода (С): на низко- (до 0,25 % С), средне- (0,25…0,6 % С) и высокоуглеродистые (> 0,6 % С).
Легированными называют стали, в химический состав которых входят специально введенные химические элементы для придания им требуемых свойств. Легированные стали подразделяют по количеству введенных легирующих элементов на три группы: низколегированные, в которых суммарное содержание легирующих элементов до 2,5 %; среднелегированные, где содержание легирующих элементов 2,5…10 %; высоколегированные с содержанием легирующих элементов > 10 %. В зависимости от введенных легирующих элементов легированные стали бывают хромистые, марганцовистые, хромоникелевые и т.д.
Классификация сталей по назначению. По назначению стали делят на конструкционные, инструментальные и стали специального назначения с особыми свойствами. Конструкционные стали представляют собой наиболее обширную группу, предназначенную для изготовления деталей машин, приборов и элементов строительных конструкций. Из конструкционных сталей можно выделить: цементируемые, азотируемые, улучшаемые, автоматные, высокопрочные и пружинно-рессорные стали.
Инструментальные стали подразделяют на стали для изготовления режущего инструмента, измерительного инструмента, для штампов холодного и горячего деформирования (штамповые стали).
Стали специального назначения – это коррозионно-, жаро- и износостойкие, жаропрочные и др.
Классификация сталей по качеству. По качеству стали классифицируют на стали обыкновенного качества, качественные, высококачественные, особовысококачественные. Под качеством стали понимают совокупность свойств, определяемых металлургическим процессом ее производства. Однородность химического состава, строение и свойства стали зависят от содержания вредных примесей и газов (кислорода, водорода, азота, серы и фосфора). Основными показателями для классификации сталей по качеству являются нормы содержания вредных примесей: серы (S) и фосфора (P). Стали обыкновенного качества содержат (%) до 0,06 S и 0,07 P; качественные до 0,035 S и 0,035 P; высококачественные до 0,025 S и 0,025 P и особовысококачественные до 0,015 S и 0,025 P.
Классификация сталей по степени раскисления. Раскислением называют процесс удаления кислорода из стали в расплавленном (жидком) состоянии. Нераскисленная сталь отмечается низкой пластичностью и подвержена хрупкому разрушению при горячей обработке давлением.
По степени раскисления стали разделяют на спокойные, полуспокойные и кипящие.
Спокойные стали – это стали с высокой степенью раскисления марганцем, алюминием и кремнием в печи или ковше. Они затвердевают в изложнице спокойно, без газообразования.
Кипящие стали – это стали раскисленные только марганцем. Они раскислены не полностью. Перед разливкой в них содержится повышенное количество кислорода, который при затвердевании слитка частично реагирует с углеродом и выделяется в виде пузырей оксида углерода СО, создавая ложное “кипение” стали.
Полуспокойные стали по степени раскисления занимают промежуточное положение между спокойными и кипящими сталями. Частично их раскисляют в печи или ковше, а частично – в изложнице с помощью содержащегося в металле углерода.
Классификация сталей по структуре. По структуре стали классифицируют в двух состояниях: после отжига и после нормализации. В отожженном (равновесном) состоянии стали делят на доэвтектоидные, имеющие в структуре избыточный феррит; эвтектоидные, состоящие из перлита; заэвтектоидные, в структуре которых содержатся вторичные карбиды, выделяющиеся из аустенита; ледебуритные – с первичными (эвтектическими) карбидами; аустенитные; ферритные. По структуре после нормализации стали подразделяют на следующие классы: перлитный, мартенситный, аустенитный, ферритный.
Широко применяемые в авиационном двигателестроении деформируемые стали и сплавы на железоникелевой основе приведены в табл. 1. Химический состав деформируемых сталей и сплавов на основе железа представлен в табл. 2, а режимы термической обработки и их механические свойства – в табл. 3.
Таблица 1. Основные деформируемые стали и сплавы на основе железа и области их применения
Марка материала | ГОСТ, ТУ _______________ | Сортамент | Обработка давлением | Область применения |
12Х13 | ТУ 14-1-377–72 и 14-1-378–72, ЧМТУ 1-518–68, ГОСТ 5949–75 | Прутки, листы | Деформируется в холодном и горячем состояниях. Интервал горячей штамповки 1150…900 °С | Детали авиационные и другие слабонагруженные детали, работающие при температурах до 400 °С |
20Х13 | Прутки, листы и ленты | Деформируется в холодном и горячем состояниях. Температурный интервал штамповки 1150…900 °С | Для деталей авиационных приборов и других деталей, работающих в легких коррозионных условиях | |
30Х13 | Прутки, листы | Деформируется в горячем состоянии. Температурный интервал штамповки 1160…900 °С. Охлаждение после деформации медленное | Детали, не имеющие концентраторов напряжений, работающие преимущественно на износ | |
40Х13 | Деформируется в горячем состоянии. Рекомендуется медленный ступенчатый нагрев перед деформацией. Температурный интервал штамповки 1150…900 °С. Рекомендуется медленное охлаждение после деформации | Детали высокой твердости (HRC > 50), работающие на износ | ||
2Х18Н10В2 (ЭП 610) | ТУ 14-1-204–72 | Прутки | Деформируется в горячем состоянии. Температурный интервал штамповки 1180…800 °С | Азотируемые детали, работающие на износ во влажной среде при температурах до 500 °С |
12Х17Г9АН4 (ЭИ 878) | ТУ 14-1-377–72 и 14-1-569–73, ЧМТУ 1-518–68, ГОСТ 5949–75 | Прутки, полосы, листы | Хорошо деформируется в горячем состоянии. Температурный интервал штамповки 1160…850 °С. Охлаждение после деформации на воздухе | Детали, работающие длительно во всех климатических условиях при температурах до 400 °С и кратковременно при тех же условиях до 800 °С |
12Х18Н10Т, 12Х18Н9Т (Я1Т) | ТУ 14-1-377–72, 14-1-378–72, 14-1-652–73 и 14-1-1073–74, ГОСТ 5949–75 | Прутки и полосы, листы, термически обработанные листы, нагартованные (без термической обработки) | Хорошо деформируется в холодном и горячем состояниях. Температурный интервал штамповки 1180…850 °С. Охлаждение после деформации на воздухе | Цельные и сварные детали самолетов и двигателей, работающие при температурах до 800 °С |
Х20Н6МД2Т (ЭП 309, ВНС-4) | ТУ 14-1-892–74 и 14-1-905–74 | Листы, ленты | Деформируется в горячем состоянии. Температурный интервал штамповки 1160…800 °С. Охлаждение после деформации на воздухе | Детали и сварные узлы, работающие в атмосферных условиях при температурах до 300 °С и кратковременно и при тех же условиях до 800 °С |
03Х11Н10М2Т (ВНС-17, ЭП 678) | ТУ 122–68 и 14-130-7–71 | Прутки, листы, ленты | Хорошо деформируется в горячем состоянии. Температурный интервал штамповки 1200… 900 °С. Охлаждение после горячей деформации на воздухе | Детали обшивки самолетов, работающие при криогенных температурах. При повышенных температурах длительное время до 400 °С, кратковременно до 500 °С |
03Х11Н10М2Т (ВНС-17У, ЭП 679) | ТУ 14-370-7–71 и 14-130-62–73 | Листы и ленты, проволока пружинная | ||
95Х18 (ЭП 229) | ТУ 14-1-377–72, ГОСТ 5949–75 | Прутки | Деформируется в горячем состоянии небольшими обжатиями. Рекомендуется медленный нагрев перед деформацией. Температурный интервал штамповки 1160…900 °С. Охлаждение после горячей деформации медленное | Детали высокой твердости, работающие на износ в условиях влажной атмосферы (коррозионностойкие шарикоподшипники и т.п.) |
1Х15Н4АМ3-Ш (ЭП 310-Ш, ВНС-5-Ш) | ТУ 14-1-940–74 | Прутки | Деформируется в горячем состоянии. Температурный интервал штамповки 1180…950 °С. Охлаждение после деформации на воздухе | Силовые детали и детали крепежа, работающие при температурах 180…300 °С |
13Х11Н2В2МФ (ЭИ 961) | ТУ 14-1-944–74, ГОСТ 5949–75 | Деформируется в горячем и холодном состояниях. Температурный интервал штамповки 1180…900 °С. Охлаждение после горячей деформации медленное | Пружины, работающие при температурах до 350 °С в топливе, маслах и атмосферных условиях с ограниченной влажностью | |
Х11Н23Т3МР (ЭП 33, ЭИ 696М) | ТУ 14-1-116–74, ГОСТ 5949–75 | Удовлетворительно деформируется в горячем состоянии. Температурный интервал штамповки 1100…900 °С | Пружины, работающие при температурах до 600 °С, кратковременно до 650 °С | |
Х15Н27Т3МР (ЭП 700) | ТУ 14-131-128–73 | Пружины, работающие при температурах до 650 °С | ||
40ХН2МА (40ХНМА) | ГОСТ 4543–71 | Деформируется в горячем состоянии. Температурный интервал штамповки 1220…800 °С | Валы, диски компрессорных машин и другие тяжело нагруженные детали, работающие при температурах до 450 °С | |
40Х2Н2МА | Валы и тяжело нагруженные детали | |||
18Х2Н4МА | ГОСТ 4543–71 | Прутки | Деформируется в горячем состоянии. Температурный интервал штамповки 1200…800 °С | Валы, шестерни и другие тяжело нагруженные детали, работающие в интервале температур 70…450 °С |
65Г | ГОСТ 14959–79 | Пружины, рессоры, тормозные диски | ||
50ХФА | Деформируется в горячем состоянии. Температурный интервал штамповки 1180…800 °С | Тяжело нагруженные пружины с повышенными требованиями к усталостной прочности, работающие при температурах до 300 °С | ||
60С2, 60С2А | Деформируется в горячем состоянии. Температурный интервал штамповки 1200…800 °С | Тяжело нагруженные пружины, торсионные валы, пружинные шайбы, работающие при температурах до 250 °С | ||
13Х14Н3В2ФР (ЭИ 736) | ГОСТ 5949–75, ТУ 14-1-3297–82 | Прутки, полосы | Деформируется в горячем состоянии. Температурный интервал штамповки 1160…850 °С. Медленные нагрев под горячую штамповку и охлаждение после горячей деформации | Для высоконагруженных деталей, дисков, стяжных болтов, лопаток компрессора, работающих при температурах до 500 °С |
10Х11Н2МБФ (ЭП 609) | ТУ 14-1-931–74 | Прутки | Деформируется в горячем состоянии. Температурный интервал штамповки 1160…950 °С. Медленное охлаждение после горячей деформации | Для сварных узлов, работающих при температурах до 600 °С |
15Х12Н2МФВАБ (ЭП 517) | ТУ 14-1-1161–75 | Прутки | Деформируется в горячем состоянии. Температурный интервал штамповки 1160…900 °С. Требует медленного нагрева охлаждения после горячей деформации | Для высоконагруженных деталей двигателя, в том числе дисков и лопаток компрессора, работающих при температурах до 650 °С |
15Х16Н2АМ (ЭП 479) | ТУ14-1-948–74 | Деформируется в горячем состоянии. Температурный интервал штамповки 1160…900 °С. Требует замедленного нагрева и охлаждения после горячей деформации | Для деталей двигателя, в том числе лопаток компрессора, работающих при температурах до 500 °С | |
14Х17Н2 (ЭИ 268) | ТУ 14-1-377–72, ГОСТ 5949–75 | Прутки, полосы | Для деталей, работающих при температурах до 400 °С в условиях влажной среды | |
16Х20К6Н2МВФ (ЭП 768, ВНС-22) | ТУ 14-1-957–74 | Прутки | Деформируется в горячем состоянии. Температурный интервал штамповки 1160…950 °С | Для лопаток компрессора, работающих в условиях морского климата при температурах до 550 °С |
Таблица 2. Химический состав основных деформируемых сталей и сплавов на основе железа
Марка материала | ГОСТ, ТУ | Химический состав, % | |||||||||
Ca | Cu | C | Cr | Ni | Mo | W | Nb | Ti | Al | ||
12Х13 | ГОСТ 5632–72 | – | 0,09… 0,15 | 12…14 | – | ||||||
Fe | Mn | Si | Zr | Ce | B | S | P | N | Co | ||
Основа | ≤ 0,6 | – | ≤ 0,025 | ≤ 0,030 | – | ||||||
Марка материала | ГОСТ, ТУ | Химический состав, % | |||||||||
Ca | Cu | C | Cr | Ni | Mo | W | Nb | Ti | Al | ||
20Х13 | ГОСТ 5632–72 | – | 0,16… 0,24 | 12…14 | – | ||||||
Fe | Mn | Si | Zr | Ce | B | S | P | N | Co | ||
Основа | ≤ 0,6 | – | ≤ 0,025 | ≤ 0,030 | – | ||||||
Марка материала | ГОСТ, ТУ | Химический состав, % | |||||||||
Ca | Cu | C | Cr | Ni | Mo | W | Nb | Ti | Al | ||
30Х13 | ГОСТ 5632–72 | – | 0,25… 0,34 | 12…14 | – | ||||||
Fe | Mn | Si | Zr | Ce | B | S | P | N | Co | ||
Основа | ≤ 0,6 | – | ≤ 0,025 | ≤ 0,030 | – | ||||||
Марка материала | ГОСТ, ТУ | Химический состав, % | |||||||||
Ca | Cu | C | Cr | Ni | Mo | W | Nb | Ti | Al | ||
40Х13 | ГОСТ 5632–72 | – | 0,35… 0,44 | 12…14 | – | ||||||
Fe | Mn | Si | Zr | Ce | B | S | P | N | Co | ||
Основа | ≤ 0,6 | – | ≤ 0,025 | ≤ 0,030 | – | ||||||
Марка материала | ГОСТ, ТУ | Химический состав, % | |||||||||
Ca | Cu | C | Cr | Ni | Mo | W | Nb | Ti | Al | ||
2Х18Н10В2 (ЭП 610) | – | – | 0,21… 0,28 | 17…19 | 9…11 | – | 2,0… 2,5 | – | |||
Fe | Mn | Si | Zr | Ce | B | S | P | N | Co | ||
– | ≤ 0,7 | 0,3… 0,8 | – | ≤ 0,030 | – | ||||||
Марка материала | ГОСТ, ТУ | Химический состав, % | |||||||||
Ca | Cu | C | Cr | Ni | Mo | W | Nb | Ti | Al | ||
12Х17Г9АН4 (ЭИ 878) | ГОСТ 5632–72 | – | ≤ 0,12 | 16… 18 | 3,5… 4,5 | – | |||||
Fe | Mn | Si | Zr | Ce | B | S | P | N | Co | ||
Основа | 8,0… 10,5 | ≤ 0,8 | – | ≤ 0,020 | ≤ 0,035 | 0,15… 0,25 | – | ||||
Марка материала | ГОСТ, ТУ | Химический состав, % | |||||||||
Ca | Cu | C | Cr | Ni | Mo | W | Nb | Ti | Al | ||
12Х18Н10Т | ГОСТ 5632–72 | – | ≤ 0,12 | 17…19 | 9…11 | – | 2,6…3,2 | – | |||
Fe | Mn | Si | Zr | Ce | B | S | P | N | Co | ||
Основа | ≤ 2,0 | – | ≤ 0,8 | ≤ 0,020 | – | ||||||
Марка материала | ГОСТ, ТУ | Химический состав, % | |||||||||
Ca | Cu | C | Cr | Ni | Mo | W | Nb | Ti | Al | ||
Х20Н6МД2Т (ЭП 309) | – | – | 1,8… 2,5 | ≤ 0,1 | 19,5… 21,5 | 5,0… 7,5 | 1,3… 1,8 | – | 0,40… 0,65 | – | |
Fe | Mn | Si | Zr | Ce | B | S | P | N | Co | ||
Основа | ≤ 1,0 | ≤ 0,8 | – | ≤ 0,020 | ≤ 0,030 | – | |||||
Марка материала | ГОСТ, ТУ | Химический состав, % | |||||||||
Ca | Cu | C | Cr | Ni | Mo | W | Nb | Ti | Al | ||
03Х11Н10М2Т (ЭП 678) | ТУ 14-1 4608–89 | ≤ 0,05 | – | ≤ 0,1 | 10,0… 11,5 | 9,0… 10,5 | 1,8… 2,3 | – | ≤ 0,15 | 0,7…1,1 | ≤ 0,15 |
Fe | Mn | Si | Zr | Ce | B | S | P | N | Co | ||
Основа | – | ≤ 0,1 | ≤ 0,02× | – | ≤ 0,003× | ≤ 0,01 | – | ||||
Марка материала | ГОСТ, ТУ | Химический состав, % | |||||||||
Ca | Cu | C | Cr | Ni | Mo | W | Nb | Ti | Al | ||
03Х11Н10М2Т (ЭП 679) | – | ≤ 0,05 | – | ≤ 0,1 | 10,0… 11,5 | 9,0… 10,5 | 1,8… 2,3 | – | ≤ 0,15 | 0,7…1,1 | ≤ 0,15 |
03Х11Н10М2Т (ЭП 679) | – | Fe | Mn | Si | Zr | Ce | B | S | P | N | Co |
Основа | – | ≤ 0,1 | ≤ 0,02× | – | ≤ 0,003× | ≤ 0,01 | ≤ 0,01 | – | |||
Марка материала | ГОСТ, ТУ | Химический состав, % | |||||||||
Ca | Cu | C | Cr | Ni | Mo | W | Nb | Ti | Al | ||
95Х18 (ЭИ 229) | ГОСТ 5632–72, ТУ 14-1-377–72 и 14-1-3957–85 | – | 0,9… 1,0 | 17…19 | – | ||||||
Fe | Mn | Si | Zr | Ce | B | S | P | N | Co | ||
Основа | ≤ 0,7 | ≤ 0,8 | – | ≤ 0,025 | ≤ 0,030 | – | |||||
Марка материала | ГОСТ, ТУ | Химический состав, % | |||||||||
Ca | Cu | C | Cr | Ni | Mo | W | Nb | Ti | Al | ||
1Х15Н4АМ3-Ш (ЭП 310-Ш) | ТУ 14-1-940–74 | – | 0,11… 0,16 | 14,0… 15,5 | 4,0… 5,0 | 2,3…2,8 | – | ||||
Fe | Mn | Si | Zr | Ce | B | S | P | N | Co | ||
Основа | ≤ 1,0 | ≤ 0,7 | – | ≤ 0,02 | ≤ 0,03 | 0,05… 0,10 | – | ||||
Марка материала | ГОСТ, ТУ | Химический состав, % | |||||||||
V | Cu | C | Cr | Ni | Mo | W | Nb | Ti | Al | ||
13Х11Н2В2МФ (ЭИ 961) | ТУ 14-1-933–74, ГОСТ 5632–72 | 0,18… 0,30 | – | 0,10… 0,16 | 10,5… 12,0 | 1,50… 1,80 | 0,35… 0,50 | 1,6… 2,0 | – | ||
Fe | Mn | Si | Zr | Ce | B | S | P | N | Co | ||
Основа | ≤ 0,60 | – | ≤ 0,02 | ≤ 0,03 | – | ||||||
Марка материала | ГОСТ, ТУ | Химический состав, % | |||||||||
Ca | Cu | C | Cr | Ni | Mo | W | Nb | Ti | Al | ||
Х11Н23Т3МР (ЭП 33, ЭИ 696М) | ГОСТ 5632–72 | – | ≤ 0,1 | 10… 12 | 21… 25 | 1,0… 1,6 | – | 2,6…3,2 | ≤ 0,8 | ||
Fe | Mn | Si | Zr | Ce | B | S | P | N | Co | ||
Основа | ≤ 0,60 | – | ≤ 0,002× | ≤ 0,010 | ≤ 0,020 | – | |||||
Марка материала | ГОСТ, ТУ | Химический состав, % | |||||||||
Ca | Cu | C | Cr | Ni | Mo | W | Nb | Ti | Al | ||
Х15Н27Т3МР (ЭП 700) | ТУ 14-131-128–73 | ≤ 0,13 | – | ≤ 0,1 | 14… 16 | 25… 28 | 1,0… 1,6 | – | 2,6…3,2 | ≤ 0,5 | |
Fe | Mn | Si | Zr | Ce | B | S | P | N | Co | ||
Марка материала | ГОСТ, ТУ | Химический состав, % | |||||||||
Сa | Cu | C | Cr | Ni | Mo | W | Nb | Ti | Al | ||
Х15Н27Т3МР (ЭП 700) | ТУ 14-131-128–73 | Основа | ≤ 0,60 | – | ≤ 0,01 | ≤ 0,02 | – | ||||
Марка материала | ГОСТ, ТУ | Химический состав, % | |||||||||
Ca | Cu | C | Cr | Ni | Mo | W | Nb | Ti | Al | ||
40ХН2МА | ГОСТ 4543–71 | – | ≤ 0,3 | 0,37… 0,44 | 0,6… 0,9 | 1,25… 1,65 | 0,15… 0,25 | – | |||
Fe | Mn | Si | Zr | Ce | B | S | P | N | Co | ||
– | 0,5.. .0,8 | 0,17… 0,37 | – | ≤ 0,025 | – | ||||||
Марка материала | ГОСТ, ТУ | Химический состав, % | |||||||||
Ca | Cu | C | Cr | Ni | Mo | W | Nb | Ti | Al | ||
40Х2Н2МА | ГОСТ 4543–71 | – | ≤ 0,3 | 0,35… 0,42 | 1,25… 1,65 | 1,35… 1,75 | 0,2… 0,3 | – | |||
Fe | Mn | Si | Zr | Ce | B | S | P | N | Co | ||
– | 0,3… 0,7 | 0,17… 0,37 | – | ≤ 0,025 | – | ||||||
Марка материала | ГОСТ, ТУ | Химический состав, % | |||||||||
Ca | Cu | C | Cr | Ni | Mo | W | Nb | Ti | Al | ||
18Х2Н4МА | – | – | ≤ 0,3 | 0,14… 0,20 | 1,35… 1,65 | 4,0… 4,4 | 0,3… 0,4 | – | |||
Fe | Mn | Si | Zr | Ce | B | S | P | N | Co | ||
– | 0,25… 0,55 | 0,17… 0,37 | – | ≤ 0,025 | – | ||||||
Марка материала | ГОСТ, ТУ | Химический состав, % | |||||||||
Ca | Cu | C | Cr | Ni | Mo | W | Nb | Ti | Al | ||
65Г | ГОСТ 14959–79 | – | ≤ 0,20 | 0,62… 0,70 | ≤ 0,25 | – | |||||
Fe | Mn | Si | Zr | Ce | B | S | P | N | Co | ||
– | 0,9… 1,2 | 0,17… 0,37 | – | ≤ 0,035 | – | ||||||
Марка материала | ГОСТ, ТУ | Химический состав, % | |||||||||
V | Cu | C | Cr | Ni | Mo | W | Nb | Ti | Al | ||
50ХФА | – | 0,1… 0,2 | ≤ 0,20 | 0,46… 0,54 | 0,8… 1,1 | ≤ 0,25 | – | ||||
50ХФА | – | Fe | Mn | Si | Zr | Ce | B | S | P | N | Co |
– | 0,5… 0,8 | 0,17… 0,37 | – | ≤ 0,025 | – | ||||||
Марка материала | ГОСТ, ТУ | Химический состав, % | |||||||||
Ca | Cu | C | Cr | Ni | Mo | W | Nb | Ti | Al | ||
60С2А | ГОСТ 14959–79 | – | ≤ 0,2 | 0,58… 0,63 | ≤ 0,3 | ≤ 0,25 | – | ||||
Fe | Mn | Si | Zr | Ce | B | S | P | N | Co | ||
– | 0,6… 0,9 | 1,6… 2,0 | – | ≤ 0,025 | – | ||||||
Марка материала | ГОСТ, ТУ | Химический состав, % | |||||||||
V | Cu | C | Cr | Ni | Mo | W | Nb | Ti | Al | ||
13Х14Н3В2ФР (ЭИ 736) | ГОСТ 5632–72 | 0,18… 0,28 | – | 0,10… 0,16 | 13…15 | 2,8… 3,4 | – | 1,6…2,2 | – | ≤ 0,05 | – |
Fe | Mn | Si | Zr | Ce | B | S | P | N | Co | ||
Основа | ≤ 0,6 | – | 0,004 | ≤ 0,025 | – | ||||||
Марка материала | ГОСТ, ТУ | Химический состав, % | |||||||||
V | Cu | C | Cr | Ni | Mo | W | Nb | Ti | Al | ||
10Х11Н2МБФ (ЭП 609) | ТУ 14-1-931–74 | 0,15… 0,25 | – | 0,05… 0,09 | 10,5… 12,0 | 1,4… 1,8 | 0,35… 0,50 | – | 0,05… 0,15 | – | |
Fe | Mn | Si | Zr | Ce | B | S | P | N | Co | ||
Основа | ≤ 0,6 | – | ≤ 0,02 | ≤ 0,03 | – | ||||||
Марка материала | ГОСТ, ТУ | Химический состав, % | |||||||||
V | Cu | C | Cr | Ni | Mo | W | Nb | Ti | Al | ||
15Х12Н2АМФВАБ (ЭП 517) | ТУ 14-1-1161–75 | 0,18… 0,30 | – | 0,13… 0,18 | 1,0… 12,5 | 1,7… 2,1 | 1,35… 1,65 | 0,65… 1,00 | 0,20… 0,35 | – | |
Fe | Mn | Si | Zr | Ce | B | S | P | N | Co | ||
Марка материала | ГОСТ, ТУ | Химический состав, % | |||||||||
V | Cu | C | Cr | Ni | Mo | W | Nb | Ti | Al | ||
15Х12Н2АМФВАБ (ЭП 517) | ТУ 14-1-1161–75 | Основа | ≤ 0,5 | – | ≤ 0,015 | ≤ 0,030 | 0,02… 0,08 | – | |||
Марка материала |
extxe.com