Быстрорежущая сталь — Википедия
Быстроре́жущие ста́ли — легированные стали, предназначенные главным образом для изготовления металлорежущего инструмента, работающего при высоких скоростях резания.
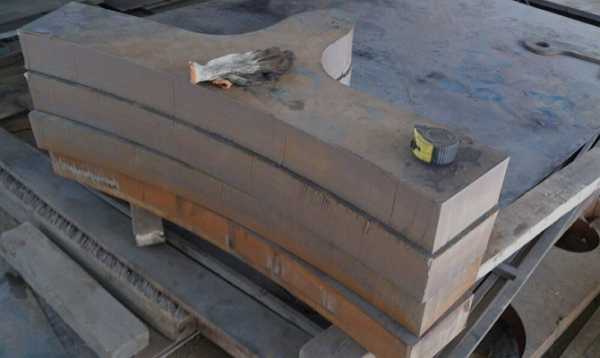
Быстрорежущая сталь должна обладать высокими сопротивлением разрушению, твёрдостью (в холодном и горячем состояниях) и красностойкостью.
Высокими сопротивлением разрушению и твердостью в холодном состоянии обладают и углеродистые инструментальные стали. Однако инструмент из них не в состоянии обеспечить высокоскоростные режимы резания. Легирование быстрорежущих сталей вольфрамом, молибденом, ванадием и кобальтом обеспечивает горячую твердость и красностойкость стали.
Сверло с покрытием из нитрида титанаДля обточки деталей из дерева, цветных металлов, мягкой стали резцы из обычной твердой стали были вполне пригодны, но при обработке стальных деталей резец быстро разогревался, скоро изнашивался и деталь нельзя было обтачивать со скоростью больше 5 м/мин
Барьер этот удалось преодолеть после того, как в 1858 году Р. Мюшетт получил сталь, содержащую 1,85 % углерода, 9 % вольфрама и 2,5 % марганца. Спустя десять лет Мюшетт изготовил новую сталь, получившую название самокалки. Она содержала 2,15 % углерода, 0,38 % марганца, 5,44 % вольфрама и 0,4 % хрома. Через три года на заводе Самуэля Осберна в Шеффилде началось производство мюшеттовой стали. Она не теряла режущей способности при нагревании до 300 °C и позволяла в полтора раза увеличить скорость резания металла — 7,5 м/мин.
Спустя сорок лет на рынке появилась быстрорежущая сталь американских инженеров Тэйлора и Уатта. Резцы из этой стали допускали скорость резания до 18 м/мин. Эта сталь стала прообразом современной быстрорежущей стали Р18.
Ещё через 5—6 лет появилась сверхбыстрорежущая сталь, допускающая скорость резания до 35 м/мин. Так, благодаря вольфраму было достигнуто повышение скорости резания за 50 лет в семь раз и, следовательно, во столько же раз повысилась производительность металлорежущих станков.
Дальнейшее успешное использование вольфрама нашло себе применение в создании твердых сплавов, которые состоят из вольфрама, хрома, кобальта. Были созданы такие сплавы для резцов, как стеллит. Первый стеллит позволял повысить скорость резания до 45 м/мин при температуре 700—750 °C. Сплав вида, выпущенный Круппом в 1927 году, имел твердость по шкале Мооса 9,7—9,9 (твердость алмаза равна 10).
В 1970-х годах в связи с дефицитом вольфрама быстрорежущая сталь марки Р18 была почти повсеместно заменена на сталь марки Р6М5 (так называемый «самокал», самозакаливающаяся сталь), которая, в свою очередь, вытесняется безвольфрамовыми Р0М5Ф1 и Р0М2Ф3.
Характеристики быстрорежущих сталей[править | править код]
Горячая твердость[править | править код]
При нормальной температуре твердость углеродистой стали даже несколько выше твердости быстрорежущей стали. Однако в процессе работы режущего инструмента происходит интенсивное выделение тепла. При этом до 80 % выделившегося тепла уходит на разогрев инструмента. Вследствие повышения температуры режущей кромки начинается отпуск материала инструмента и снижается его твердость.
После нагрева до 200 °C твердость углеродистой стали начинает быстро падать. Для этой стали недопустим режим резания, при котором инструмент нагревался бы выше 200 °C. У быстрорежущей стали высокая твердость сохраняется при нагреве до 500—600 °C. Инструмент из быстрорежущей стали более производителен, чем инструмент из углеродистой стали.
Красностойкость[править | править код]
Если горячая твердость характеризует то, какую температуру сталь может выдержать, то красностойкость характеризует, сколько времени сталь будет выдерживать такую температуру. То есть насколько длительное время закаленная и отпущенная сталь будет сопротивляться разупрочнению при разогреве.
Существует несколько характеристик красностойкости. Приведем две из них.
Первая характеристика показывает, какую твердость будет иметь сталь после отпуска при определенной температуре в течение заданного времени.
Второй способ охарактеризовать красностойкость основан на том, что интенсивность снижения горячей твердости можно измерить не только при высокой температуре, но и при комнатной, так как кривые снижения твердости при высокой температуре и комнатной идут эквидистантно, а измерить твердость при комнатной температуре, разумеется, гораздо проще, чем при высокой. Опытами установлено, что режущие свойства теряются при твердости 50 HRC при температуре резания, что соответствует примерно 58 HRC при комнатной. Отсюда красностойкость характеризуется температурой отпуска, при которой за 4 часа твердость снижается до 58 HRC (обозначение K
Марка стали | Температура отпуска, °C | Время выдержки, час | Твердость, HRCэ |
---|---|---|---|
У7, У8, У10, У12 | 150—160 | 1 | 63 |
Р9 | 580 | 4 | |
У7, У8, У10, У12 | 200—220 | 1 | 59 |
Р6М5К5, Р9, Р9М4К8, Р18 | 620—630 | 4 |
Сопротивление разрушению[править | править код]
Химический состав быстрорежущих сталей[править | править код]
Марка стали | C | Cr | W | Mo | V | Co |
---|---|---|---|---|---|---|
Р0М2Ф3 | 1,10—1,25 | 3,8—4,6 | — | 2,3—2,9 | 2,6—3,3 | — |
Р6М5 | 0,82—0,90 | 3,8—4,4 | 5,5—6,5 | 4,8—5,3 | 1,7—2,1 | < 0,50 |
Р6М5Ф2К8 | 0,95—1,05 | 3,8—4,4 | 5,5—6,6 | 4,6—5,2 | 1,8—2,4 | 7,5—8,5 |
Р9 | 0,85—0,95 | 3,8—4,4 | 8,5—10,0 | < 1,0 | 2,0—2,6 | — |
Р18 | 3,8—4,4 | 17,0—18,5 | < 1,0 | 1,0—1,4 | < 0,50 |
Изготовление и обработка быстрорежущих сталей[править | править код]
Быстрорежущие стали изготавливают как классическим способом (разливка стали в слитки, прокатка и проковка), так и методами порошковой металлургии (распыление струи жидкой стали азотом)[3]. Качество быстрорежущей стали в значительной степени определяется степенью её прокованности. При недостаточной проковке изготовленной классическим способом стали наблюдается карбидная ликвация.
При изготовлении быстрорежущих сталей распространенной ошибкой является подход к ней как к «самозакаливающейся стали». То есть достаточно нагреть сталь и охладить на воздухе, и можно получить твердый износостойкий материал. Такой подход абсолютно не учитывает особенности высоколегированных инструментальных сталей.
Перед закалкой быстрорежущие стали необходимо подвергнуть отжигу. В плохо отожженных сталях наблюдается особый вид брака: нафталиновый излом, когда при нормальной твердости стали она обладает повышенной хрупкостью.
Грамотный выбор температуры закалки обеспечивает максимальную растворимость легирующих добавок в α-железе, но не приводит к росту зерна.
После закалки в стали остается 25—30 % остаточного аустенита. Помимо снижения твердости инструмента, остаточный аустенит приводит к снижению теплопроводности стали, что для условий работы с интенсивным нагревом режущей кромки является крайне нежелательным. Снижения количества остаточного аустенита добиваются двумя путями: обработкой стали холодом или многократным отпуском
Принципы легирования быстрорежущих сталей[править | править код]
Высокая твердость мартенсита объясняется растворением углерода в α-железе. Известно, что при отпуске из мартенсита в углеродистой стали выделяются мельчайшие частицы карбида. Пока выделившиеся карбиды ещё находятся в мельчайшем дисперсном рассеянии (то есть на первой стадии выделения при отпуске до 200 °C), твердость заметно не снижается. Но если температуру отпуска поднять выше 200 °C, происходит рост карбидных выделений, и твердость падает.
Чтобы сталь устойчиво сохраняла твердость при нагреве, нужно её легировать такими элементами, которые затрудняли бы процесс коагуляции карбидов. Если ввести в сталь какой-нибудь карбидообразующий элемент в таком количестве, что он образует специальный карбид, то красностойкость скачкообразно возрастает. Это обусловлено тем, что специальный карбид выделяется из мартенсита и коагулирует при более высоких температурах, чем карбид железа, так как для этого требуется не только диффузия углерода, но и диффузия легирующих элементов. Практически заметная коагуляция специальных карбидов хрома, вольфрама, молибдена, ванадия происходит при температурах выше 500 °C.
Красностойкость создается легированием стали карбидообразующими элементами (вольфрамом, молибденом, хромом, ванадием) в таком количестве, при котором они связывают почти весь углерод в специальные карбиды, и эти карбиды переходят в раствор при закалке. Несмотря на сильное различие в общем химическом составе, состав твердого раствора очень близок во всех сталях, атомная сумма W+Mo+V, определяющая красностойкость, равна примерно 4 % (атомн.), отсюда красностойкости и режущие свойства у разных марок быстрорежущих сталей близки. Быстрорежущая сталь, содержащая кобальт, превосходит по режущим свойствам остальные стали (он повышает красностойкость), но кобальт очень дорогой элемент.
В советских и российских марочниках сталей марки быстрорежущих сталей обычно имеют особую систему обозначений и начинаются с буквы «Р» (rapid — быстрый). Связано это с тем, что эти стали были изобретены в Англии, где такую сталь называли «rapid steel». Цифра после буквы «Р» обозначает среднее содержание в ней вольфрама (в процентах от общей массы, буква В пропускается). Затем указывается после букв М, Ф и К содержание молибдена, ванадия и кобальта. Инструменты из быстрорежущей стали иностранного производства обычно маркируются аббревиатурой HSS (High Speed Steel), а также HSSE (кобальтовая сталь).
Сравнение твёрдости быстрорежущих сталей с кобальтом и сталей без кобальта в зависимости от температуры.В последние десятилетия использование быстрорежущей стали сокращается в связи с широким распространением твёрдых сплавов. Из быстрорежущей стали изготавливают в основном концевой инструмент (метчики, свёрла, фрезы небольших диаметров) В токарной обработке резцы со сменными и напайными твердосплавными пластинами почти полностью вытеснили резцы из быстрорежущей стали.
По применению отечественных марок быстрорежущих сталей существуют следующие рекомендации.
- Сталь Р9 рекомендуют для изготовления инструментов простой формы, не требующих большого объёма шлифовки, для обработки обычных конструкционных материалов. (резцов, фрез, зенкеров).
- Для фасонных и сложных инструментов (для нарезания резьб и зубьев), для которых основным требованием является высокая износостойкость, рекомендуют использовать сталь Р18 (вольфрамовая).
- Кобальтовые быстрорежущие стали (Р9К5, Р9К10) применяют для обработки деталей из труднообрабатываемых коррозионно-стойких и жаропрочных сталей и сплавов, в условиях прерывистого резания, вибраций, недостаточного охлаждения.
- Ванадиевые быстрорежущие стали (Р9Ф5, Р14Ф4) рекомендуют для изготовления инструментов для чистовой обработки (протяжки, развёртки, шеверы). Их можно применять для обработки труднообрабатываемых материалов при срезании стружек небольшого поперечного сечения.
- Вольфрамомолибденовые стали (Р9М4, Р6М3) используют для инструментов, работающих в условиях черновой обработки, а также для изготовления протяжек, долбяков, шеверов, фрез.
- ↑ Мезенин Н. А. Занимательно о железе. — М.: «Металлургия», 1972. — 200 с.
- ↑ Марочник сталей и сплавов / В. Г. Сорокин, А. В. Волосникова, С. А. Вяткин, и др. Под общ. ред. В. Г. Сорокина. — М.: Машиностроение, 1989. — 640 с.
- ↑ 1 2 Гуляев А. П. Металловедение. Учебник для втузов. 6-е изд., перераб. и доп. — М.: «Металлургия», 1986. — 544 с.
- Технология конструкционных материалов. Под ред. А. М. Дальского. — М.: «Машиностроение», 1958.
ru.wikipedia.org
Аустенит — Википедия
Материал из Википедии — свободной энциклопедии
Текущая версия страницы пока не проверялась опытными участниками и может значительно отличаться от версии, проверенной 8 октября 2018; проверки требуют 2 правки. Текущая версия страницы пока не проверялась опытными участниками и может значительно отличаться от версии, проверенной 8 октября 2018; проверки требуют 2 правки.Аустенит (γ-фаза) — высокотемпературная гранецентрированная модификация железа и его сплавов.
Фаза названа в честь сэра Уильяма Чандлера Робертс-Остина (англ. William Chandler Roberts-Austen, 1843—1902).
В углеродистых сталях аустенит — это твёрдый раствор внедрения, в котором атомы углерода входят внутрь элементарной ячейки γ-железа во время конечной термообработки. В сталях, содержащих другие металлы (кроме железа, легированные стали), атомы металлов замещают атомы железа в кристаллической решётке и возникает твёрдый раствор замещения. В чистом железе существует в интервале температур 910—1401 °C; в углеродистых сталях аустенит существует при температурах не ниже 727 °C.
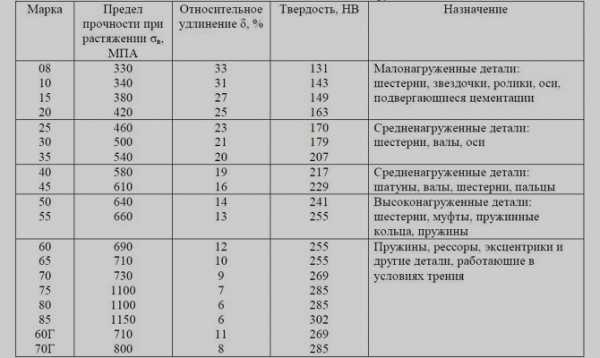
В легированных сталях аустенит может существовать и при гораздо более низких температурах. Такие элементы, как никель стабилизируют аустенитную фазу. Нержавеющие стали, такие как 08Х18Н10Т или AISI 304, AISI 316 и т. д. относятся к аустенитному классу. Присутствие никеля в количестве 8—10 % приводит к тому, что аустенитная фаза сохраняется и при комнатной температуре. Мартенситностареющие нержавеющие стали типа 08Х15Н2ДТ или Ph 17-4 могут содержать некоторое количество остаточного аустенита. Оптическая металлография во многих случаях не позволяет выявить присутствие аустенита, расположенного, как правило, по границам мартенситных пакетов. Основными способами определения количества остаточного аустенита являются рентгеноструктурный анализ и просвечивающая электронная микроскопия.
- Гуляев А. П. Металловедение.
- Потак Я. М. Высокопрочные стали.
- Лившице Б. Г. Металлография.
ru.wikipedia.org
Обсуждение:Сталь — Википедия
Глупая война правок. Я прекрасно знаю, что в Википедии это спор решен и что правильно писать «на Украине», но остаюсь на стороне анонимного участника, который пытался пропихнуть версию с «В». Я живу в Украине и всегда пишу и встречаю (в книгах, прессе) версию «в Украине». Признаю, что в России ситуация может быть другой, но это выглядит довольно смешно и глупо. Но согласен, холивар устраивать смысла нет. Ink 19:54, 13 декабря 2010 (UTC)
Вна Украине — пишут «в», в России — «на». Соответственно — в русском разделе википедии пишут по-русски. А не по-украински…
- По правилам русского языка, правильно писать «на Украине». HarDNoxぎ¿ 19:37, 13 июня 2015 (UTC)
Господа, существующее определение стали можно подогнать любое г… на основе железа с примесью углерода до 2,14% Потому-то и есть гостированные ограничения по количеству примесей. Кроме того, не все стали ковкие! Яркий пример сталь ХВГ, которая не куется, потому что очень хрупкая. Еще, при указывании верхнего предела по содержанию углерода указывайте уже и нижний предел, а то норот подумает, что железо с 0,005% углерода тоже сталь. Предлагаю следующее определение: Сталь — это сплав железа с углеродом с содержанием углерода от 0,01% до 2,14% (на практике до 2%), а также содержанием постоянных примесей: серы до 0,04%, фосфора до 0,04%, марганца до 0,8% и кремния до 0,08%.
Далее. Следует перечислить виды классиикации стали, описать хотябы виды обычной углеродистой стали по структуре, та в конце концов, описание стали нужно начинать с диаграммы железо-углерод!
Статью писал безграмотный студент-двоишник 2-го курса машиностроительного вуза —213.227.245.156 12:34, 5 апреля 2012 (UTC)
Изменяю определение стали[править код]
Совершенно безграмотное определение стали. Сталь вовсе не обязана быть твердым раствором (эвтектика — не твердый раствор) или иметь эвтектическое превращение (низкоуглеродистые стали — доэевтектические). Поэтому меняю определение. Chivesud 20:14, 19 августа 2013 (UTC)
не хватает истории появления стали, развития производства стали 213.87.122.208 11:21, 6 сентября 2013 (UTC) Жорик
Очень хреновая статья.[править код]
Господа металлурги, у кого есть день-другой свободного времени? Пожалуйста… Абсолютно с Вами согласен. Хрень полная.217.118.83.166
Электротермический способ[править код]
«до 800 кВт / ч на 1 т стали»
Энергия получается не делением, а умножением мощности (кВт) на время (час): кВт•час. Лучше словом: киловатт-час. Леонид 87.99.93.122 12:21, 14 декабря 2015 (UTC)
«Кодовый символ». Наверное, всё же условный знак (или усл. обозначение). Текст, случаем, не из школьного учебника «перетяпан», в большей своей части? Yury Tarasievich 06:28, 3 января 2016 (UTC)
…до 1991 учитывает РСФСР или СССР? Yury Tarasievich 06:28, 3 января 2016 (UTC)
Пункты 3 и 7 называются одинаково: «Производство стали»
213.141.146.181 18:39, 2 февраля 2016 (UTC)
Я удивляюсь вам, господа мелаллурги. Посвятить столько места и усилий на устаревшие методы — мартеновский, бессемеровский, томасовский… Только читателя путаете. Может кто не ленивый может их обработать, чтобы историческая значимость была отмечена, а большая часть букв (совершенно ненужных) была выкинута?
Chivesud (обс.) 17:58, 22 октября 2017 (UTC)
ru.wikipedia.org
Углеродистая сталь
Углеродистая сталь — это инструментальная сталь, содержащая 0,04- 2% углерода и всегда присутствующие примеси, не содержащая легирующих легируемых элементов. Углеродистая сталь в зависимости от процентного содержания углерода, разделяется на три основных типа:
- низкоуглеродистая;
- среднеуглеродистая;
- высокоуглеродистая.
Данный материал нуждается в термообработке, после которой становится достаточно твердым и прочным чтобы выдерживать достаточные нагрузки в ответственных узлах. Спав применяется в производстве инструмента. Углеродистая сталь классифицируется как:
- качественная, содержит до 0,035% фосфора и серы;
- высококачественная, содержит до 0,025% фосфора и серы.
Углеродистая сталь марки
Углеродистая сталь марки которой имеют большое разнообразие. Согласно ГОСТ 1435-99 металлургическая промышленность выпускает следующие марки инструментальной углеродистой стали:
- У7;
- У7А;
- У8;
- У8А;
- У9А;
- У10;
- У11;
- УНА;
- У12;
- У12А;
- У13;
- У13А.
Буква У обращает внимание что сталь углеродистая. Обозначение буквы А, в конце марки, означает группу высококачественной стали с более чистым наличием серы и фосфора. Цифры в обозначении показывают процентное содержание углерода в сплаве, численное выражение которого для удобства умножено на 10. Отсутствие буквы А означает качественную сталь. Цифра указывает содержание углерода, среднее, Г- показывает на высокое наличие марганца. Углеродистая сталь марки имеют малую стоимость и большую твердость и этим отличается от других инструментальных сталей. Износостойкость этих марок и теплостойкость низкая. Углеродистая сталь марки У7, У7А успешно используют для деревообрабатывающих инструментов — топоров, стамесок, долот, также инструментов по металлу — зубила, кузнечные штампы, слесарные инструменты, молотки, кувалды, отвертки, кусачки и др. Марки У8, У8А, У8Г, У8ГА используют для изготовления таких инструментов, которые очень стойкие к разогреву при работе и выдерживают нагрузки вращения- фрезы по дереву, зенковки, пилы продольные, дисковые, накатные ролики и др. Углеродистая сталь марки У10, У10А служит для изготовления игольной проволоки, также инструмента, который не вызывает нагрева режущей кромки. У13, У13А используют для инструментов, где необходима повышенная износостойкость, лезвия бритвы, хирургические инструменты, инструментов для гравировки металла, камня.
Свойства углеродистой стали
Свойства углеродистой стали значительно улучшаются, когда она подвергается термообработке. После данного процесса сплав приобретает высокую твердость, прочность, способность реагировать на большие нагрузки, выдерживать высокую температуру при работе режущей кромки. Свойства углеродистой стали позволяют ей быть одним из самых востребованных видов стали. Характеристики и свойства материала регулируют при выплавке, соблюдая необходимые нормы процентного содержания элементов сплава. Свойства углеродистой стали позволяют успешно сваривать ее, обрабатывать резанием, введенные в нее легирующие элементы изменяют свойства, повышаются механические способности, снижается хладноломкость.
Типы углеродистой стали
Типы углеродистой стали разделяют на:
- А- поставляемую по своим механическим свойствам, которые можно изменить;
- Б- по своим химическим свойствам, при этом механические свойства меняются, а уровень определяется химическим составом;
- В- поставляют по химическому содержанию и по своим механическим свойствам для деталей.
Типы углеродистой стали по виду обработки выделяют:
- горячекатаная;
- кованая;
- калиброванная;
- круглую со специальной отделкой поверхности.
По степени раскисления:
- полуспокойная;
- спокойная;
- кипящая.
metallsmaster.ru
Что такое углеродистая сталь, ее производство, маркировка и способы применения
Благодаря своим прочностным характеристикам и доступной цене углеродистая сталь является весьма распространенным сплавом. Его главные элементы — это железо и углерод с минимумом присесей. Из углеродной стали производят различную машиностроительную продукцию, детали трубопроводов и котлов, инструменты. В строительстве сплавы тоже нашли широкое применение.
Основные характеристики
В зависимости от основного своего назначения углеродистые стали делятся на инструментальные и конструкционные, легирующих элементов в их составе практически нет. От обыкновенных стальных сплавов они отличаются еще и тем, что имеют в составе значительно меньше базовых примесей: марганца, магния, кремния. Содержание главного элемента — углерода — варьируется в довольно широких пределах. В составе высокоуглеродистой стали содержится 0,6−2% C, среднеуглеродистой — 0,3−0,6%, низкоуглеродистой — до 0,25%.
Основной элемент определяет свойства и структуру. Во внутренней структуре сплавов с менее чем 0,8% C (сталь доэвтектоидная) — преимущественно перлит и феррит, а при увеличении концентрации главного элемента формируется вторичный цементит.
Представленные стали с преобладанием ферритной структурой высоко пластичны и имеют низкую прочность. Если в структуре преобладает цементит, металл характеризуется высокой прочностью, однако и большой хрупкостью. При повышении содержания C до 0,8−1% растет прочность и твердость, но сильно ухудшается вязкость и пластичность.
Количественное содержание углерода сказывается на технологических характеристиках, в частности, на свариваемости, легкости обработки резанием и давлением.
- Из низкоуглеродистых сталей изготавливают детали и конструкции, не предназначенные для значительных нагрузок.
- Характеристики среднеуглеродистых сталей делают их основным конструкционным материалом, который используется в производстве конструкций и деталей для транспортного и общего машиностроения.
- Высокоуглеродистые сплавы оптимальны для изготовления деталей, которые должны иметь повышенную износостойкость, в производстве измерительного и ударно-штампового инструмента.
Металл, как и иные стальные сплавы, в составе содержат примеси:
- кремний;
- фосфор;
- марганец;
- азот;
- серу;
- водород;
- кислород.
Кремний и марганец — это полезные примеси, которые вводятся в состав на стадии выплавки для раскисления. Фосфор и сера — вредные примеси, ухудшающие качественные характеристики сплава.
Считается, что легирование и углеродистые виды несовместимы, тем не менее с целью улучшения их технологических и физико-механических характеристик может выполняться микролегирование с помощью добавления различных добавок:
- бора;
- титана;
- циркония;
- редкоземельных элементов.
С их помощью не удастся превратить металл в нержавейку, но значительно улучшить свойства получится.
Классификация по степени раскисления
На разделение на типы влияет, в частности, степень раскисления. В зависимости от этого параметра наши сплавы делят на полуспокойные, спокойные и кипящие.
Более однородную внутреннюю структуру имеют спокойные стали, чье раскисление достигается путем добавления в расплавленный металл алюминия, ферросилиция и ферромарганца. Благодаря тому, что сплавы нашей категории полностью раскислились в печи, в их составе отсутствует закись железа. Остаточный алюминий, препятствующий росту зерна, обеспечивает мелкозернистую структуру. Она и практически абсолютное отсутствие растворенных газов позволяет получить качественный металл для изготовления из него самых ответственных деталей и конструкций. Наряду с плюсами у спокойных сплавов есть большой минус — достаточно дорогая выплавка.
Есть более дешевые, хотя и менее качественные, углеродистые сплавы, при выплавке которых используют минимум специальных добавок. В структуре такого металла из-за того, что процесс раскисления в печи не довели до конца, есть растворенные газы, негативно отражающиеся на характеристиках. Азот, например, плохо влияет на свариваемость и провоцирует образование трещин в области шва. Развитая ликвация в структуре сплавов приводит к тому, что металлопрокат, сделанный из них, отличается неоднородностью по структуре и механическим характеристикам.
У полуспокойных сталей промежуточное положение по свойствам и степени раскисления. Перед заливкой в изложницы в состав их вводится немного раскислитилей, благодаря которым затвердеванием металла происходит практически без кипения, но выделение газов в нем продолжается. В результате получается отливка, в структуре которой меньше газовых пузырей, чем в кипящих сталях. Эти внутренние поры при последующей прокатке металла завариваются практически полностью.
Большая часть полуспокойных углеродистых сталей используется как конструкционные материалы.
Производство и деление по качеству
Углеродистые стали получают путем использования разных технологий. Различают:
- качественные углеродистые стали;
- высококачественные стальные сплавы;
- углеродистые стальные сплавы обыкновенного качества.
Сплавы обыкновенного качества получают в мартеновских печах, а из них формируются большие слитки. К плавильному оборудованию, использующемуся для получения таких сталей, относятся, в частности, кислородные конвертеры. В сравнении с качественными стальными сплавами, в металле может содержаться много вредных примесей, что отражается на характеристиках и стоимости производства.
Сформированные и застывшие слитки прокатывают горячими или холодными. Горячей прокаткой получают сортовые и фасонные изделия, тонколистовой и толстолистовой металл, широкие металлические полосы. Холодной прокаткой получают тонколистовой металл.
Для производства качественной и высококачественной стали используются мартеновские печи и конвертеры, а также плавильные печи, которые работают на электричестве.
К составу, а именно к наличию в структуре вредных и неметаллических примесей, ГОСТ предъявляет жесткие требования. В высококачественных сталях должно быть не более 0,04% серы и не более 0,035% фосфора. Высококачественные и качественные стальные сплавы благодаря строгим требованиям к способу выплавки и характеристикам имеют повышенную чистоту структуры.
Применение и маркировка
Инструментальные сплавы, в которых 0,65−1,32% C, используются для изготовления различного инструмента. Для улучшения механических свойств инструментов делают закалку материала изготовления.
Из конструкционных сплавов делают детали для разного оборудования, элементы конструкций строительного и машиностроительного назначения, крепежные детали и прочее. Из конструкционной стали делается проволока углеродистая, которая используется в быту, в производстве крепежа, в строительстве, для изготовления пружин. После цементации конструкционные сплавы успешно используются в производстве деталей, подвергающихся при эксплуатации серьезному поверхностному износу и испытывающих большие динамические нагрузки.
Маркировка говорит о химическом составе сплава и о его категории. В обозначении углеродистой стали обыкновенного качества есть буквы «ст». ГОСТ оговаривает семь условных номеров марок (0−6), также указывающихся в обозначении. Степень раскисления обозначают буквы «кп», «пс», «сп», проставленные в конце маркировки. Марки высококачественных и качественных сталей обозначаются цифрами, которые указывают на содержание в сплаве C в сотых долях процента.
О том, что сплав инструментальный, можно понять по букве «У» в начале маркировки. Цифра, следующая за этой буквой, говорит о содержании C в десятых долях процента. Литера «А», если таковая присутствует в обозначении инструментальной стали, указывает на улучшенные качественные характеристики сплава.
Стали с повышенным содержанием углерода могут быть менее склонными к образованию структур малой пластичности. При воздействии структурных и сварочных напряжений металл малой пластичности может разрушиться. Этому способствует наличие в нем и его сварочном шве диффузионного водорода. Для предупреждения появления холодных трещин применяются способы, позволяющие устранить факторы, способствующие появлению таких недостатков.
tokar.guru
Углеродистая сталь — Мегаэнциклопедия Кирилла и Мефодия — статья
Углеро́дистая сталь — нелегированная конструкционная или инструментальная сталь, содержащая менее 2, 14% углерода. Углеродистые стали классифицируют по структуре, способу производства и раскисления, по качеству. По структуре углеродистая сталь может быть доэвтектоидной (содержит до 0, 8% углерода, структура состоит из феррита и перлита), эвтектоидной (содержит около 0, 8% углерода, структура состоит только из перлита), заэвтектоидной, (содержит 0, 8-2, 14% углерода, структура состоит из зерен перлита, окаймленных сеткой цементита). По способу производства различают углеродистые стали, выплавленные в электропечах, мартеновских печах и кислородно-конвертерным способом. По способу раскисления различают кипящие, полуспокойные, спокойные стали. По назначению углеродистые стали делятся на конструкционные стали и инструментальные стали; существует также группа углеродистых сталей специального назначения. По содержанию углерода углеродистые стали подразделяются на низкоуглеродистые, с содержанием углерода до 0, 25 %; среднеуглеродистые, с содержанием углерода в 0, 3-0, 6%; высокоуглеродистые, с содержанием углерода выше 0, 6%. Различают также обыкновенные углеродистые стали и качественные углеродистые стали.Содержание углерода в стали определяет ее структуру и свойства, так как с увеличением концентрации углерода в стали в ее структуре увеличивается количество цементита. Структура стали с содержанием углерода менее 0, 8 % состоит из феррита и перлита, при более высоком содержании углерода в структуре стали, кроме перлита, появляется структурно свободный вторичный цементит. Сталь со структурой феррита достаточно пластичная, но имеет низкую прочность; сталь со структурой цементита хрупкая, но имеет высокую твердость. С увеличением содержания углерода (до 0, 8-1, 0 %) увеличивается твердость и прочность нелегированных сталей, но уменьшается их вязкость и пластичность. Содержание углерода влияет на такие технологические свойства стали, как свариваемость, обрабатываемость давлением и резанием. Низкоуглеродистые стали используются для изготовления малонагруженных деталей и конструкций, среднеуглеродистые стали — основной конструкционный материал в общем и транспортном машиностроении, высокоуглеродистые стали используются для изготовления деталей с высокой износостойкостью, а также для изготовления измерительного, режущего, ударно-штампового инструмента.
На свойства стали влияет содержание постоянных (марганец, кремний, сера, фосфор) и скрытых (кислород, азот, водород) примесей. Полезными примесями являются марганец и кремний, которые вводят в сталь в процессе выплавки для раскисления. Вредными примесями в углеродистой стали являются сера и фосфор. Для улучшения физико-химических и технологических свойств применяют микролегирование углеродистой стали титаном, цирконием, бором, редкоземельными элементами.
Характерной чертой кипящей стали является незавершенный процесс ее раскисления. Эта сталь имеет повышенную пластичность, хорошо штампуется и сваривается. Она более дешевая, так как при ее выплавке расходуется минимальное количество специальных добавок и обеспечивается максимальный выход годного продукта. Недостатком кипящей стали является развитая ликвация, в результате которой прокат из ее неоднороден по структуре и механическим свойствам.
Спокойная сталь раскислена ферромарганцем, ферросилицием, алюминием и более однородна по составу. Остаточный алюминий снижает склонность к росту зерна, поэтому прочность и хладостойкость проката из спокойной и мелкозернистой стали выше, чем у проката из кипящей стали. Полуспокойная сталь характерна промежуточной степенью раскисления. В отличие от кипящей стали ее перед разливкой обрабатывают небольшим количеством раскислителей. По свойствам она занимает промежуточное положение между кипящей и спокойной сталями.В углеродистых сталях обыкновенного качества допускается более высокое содержание вредных примесей, чем в качественных углеродистых сталях. Их выплавляют в крупных мартеновских печах и кислородных конвертерах, обозначают буквами Ст и цифрами от 0 до 6. Цифры указывают условный номер марки стали в зависимости от ее химического состава. Буквы кп, пс, сп в конце марки указывают на способ раскисления: кп — кипящая, пс — полуспокойная, сп — спокойная. К углеродистым сталям обыкновенного качества относятся горячекатаная стать (сортовая, фасонная, толстолистовая, тонколистовая, широкополосная) и холоднокатаная сталь (тонколистовая).
К качественным углеродистым сталям предъявляются жесткие требования по содержанию вредных примесей (содержание серы не должно превышать 0, 04%, фосфора — 0, 035 %). Их выплавляют в электропечах, кислородных конвертерах, мартеновских печах. Качественные углеродистые стали маркируются двузначными цифрами (05, 10, 15), указывающими среднее содержание углерода в сотых долях процента. Буква А в конце марки указывает на улучшенное металлургическое качество. При обозначении кипящей или полуспокойной стали указывается степень раскисленности: кп, пс. У спокойной стали степень раскисленности не указывается.
megabook.ru
Углеродистая сталь: марки и классификация
Углеродистая сталь, марки которой описаны ниже, широко применяется в различных отраслях. Выбор определенной марки углеродистой стали осуществляется, исходя из конкретной цели, в которой она будет использована. Это связано с тем, что каждая марка отличается своими характеристиками.
Классификация стали
Все углеродистые стали, в зависимости от области предназначения, разделяются на низкоуглеродистые, среднеуглеродистые и высокоуглеродистые стали, и делятся по нескольким параметрам:
- Метод раскисления.
- Состав химических элементов.
- Микроструктура.
- Качество.
Согласно основным стандартам, углеродистые стали делятся на:
- Конструкционную обычную.
- Конструкционную качественную.
- Инструментальную качественную.
- Инструментальную высокого качества.
Технология изготовления
Изготовление стали в металлургической промышленности производится различными способами. Каждый метод производства отличается, в зависимости от применяемого оборудования. Так, все оборудование для производства углеродистых сталей можно разделить на три типа:
- Конверторные плавильные печи.
- Печи мартеновского типа.
- Электрические печи.
Конверторные
Конверторные печи осуществляют расплавление всего состава сплава. При таком методе расплавленная масса подвергается обработке техническим кислородом. Для очистки раскаленной массы от разнообразных примесей в нее добавляют известь. Так удается превратить примеси в шлак. Во время производственного процесса активно происходит процесс окисления металла. Это провоцирует выделение большого количества угара.
Изготовление углеродистых сталей в печах конверторного типа имеет существенный недостаток. К нему относится то, что при работе происходит выделение большого количества пыли. Это приводит к необходимости установки дополнительных фильтровальных установок, что влечет за собой затраты денежных средств. Несмотря на это, конверторный метод имеет высокую производительность, и широко применяется в металлургии.
Мартеновские
Получение различных марок углеродистой стали с использованием печей мартеновского типа дает возможность получить конечный продукт высокого качества. Производственный процесс происходит следующим образом:
- В специализированный отсек печи загружаются составляющие сплава: чугун, стальной лом и т. д.;
- Весь состав нагревается до высокой температуры;
- Под воздействием температуры все составляющие превращаются в однородную раскаленную массу;
- При плавлении происходит взаимодействие всех компонентов сплава железа и углерода;
- Материал, получившийся в результате химического взаимодействия, выходит из печи.
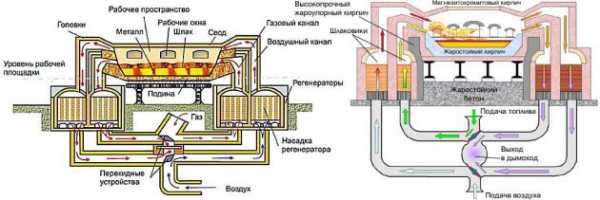
Принцип работы мартеновской печи
Электрические
Способ получения различных марок углеродистой стали в электрических печах отличается от вышеперечисленных. Его отличие состоит в способе нагрева состава. Применение электричества для разогрева компонентов снижает окисляемость металла. Это значительно уменьшает количество водорода в составе металла, что улучшает структуру сплава и влияет на качество окончательного продукта.
Использование стали
Углеродистая сталь различных марок используется для изготовления конструкций во многих отраслях. В зависимости от области применения продукции, используются определенные марки.
Обычного качества
Количество посторонних примесей, находящихся в готовой продукции, регламентировано ГОСТ 380-2005. Углеродистая сталь обычного качества используется для производства:
- Ст0 – обшивки, арматуры и т. д.;
- Ст1 – швеллеров, тавровых и двутавровых балок. Отличается низкой твердостью, но хорошей вязкостью;
- Ст2 – частей неответственных конструкций. Является высокопластичным материалом;
- Ст3 – металлопроката, применяемого для возведения строительных конструкций, кузова, дисков автомобильной техники и т. п.;
- Ст5 – болтов, гаек, рычагов, пальцев, осей и т. д.;
- Ст6 – деталей повышенной прочности для деревообрабатывающих и металлообрабатывающих станков.
Качественная
Из марок качественной стали изготавливают:
Применение углеродистой стали
- Трубы и детали, которые применимы в котлостроении.
- Изделия с высокой пластичностью – болты, гайки и др.
- Детали, предназначенные для создания свариваемых конструкций.
- Различного рода патрубки, пальцы, оси.
- Шестерни, муфты сцепления грузовых автомобилей, автобусов и другой техники.
- Пружинные шайбы, кольца.
Инструментальная
Углеродистые инструментальные стали разных марок имеют повышенную прочность, и большой показатель ударной вязкости. Они применяются для создания всевозможных инструментов и сменных элементов. При производстве изделия подвергаются многократному воздействию высокой температуры, что улучшает их физические свойства. Изделия устойчивы к быстрому изменению температуры, и имеют высокую устойчивость к коррозии.
Маркировка стали
Все углеродистые согласно маркировке стали делятся на три категории:
- Группа А. К ней относятся сплавы, соответствующие строго заданным механическим свойствам;
- Группа Б. Стали этой группы четко соответствуют по химическому составу;
- Группа В. Продукция этой группы должна соответствовать механическим, физическим и химическим свойствам одновременно.
У стали обыкновенного качества в начале обозначения стоят буквы Ст. За буквами Ст в маркировке идет цифровое обозначение. Цифра в маркировке обозначает номер марки металла. Далее, после номера, вписывается тип сплава. Обозначение типа сплава следующее:
- КП – кипящий;
- ПС – полуспокойный;
- СП – спокойный.
Непосредственно перед буквенным обозначением сплава стоит буква, обозначающая группу стали. Если продукт относится к группе А, то буква не проставляется.
Цветовая маркировка
Для быстрого определения марки производитель наносит специализированной краской соответствующие полосы:
- Ст0 – зеленая полоса + красная.
- Ст1 – одна желтая + одна черная.
- Ст3Гсп – коричневая + синяя.
- Ст3 – красная.
- Ст4 – черная.
- Ст5Гпс – коричневая + зеленая.
- Ст5 – зеленая.
- Ст6 – синяя.
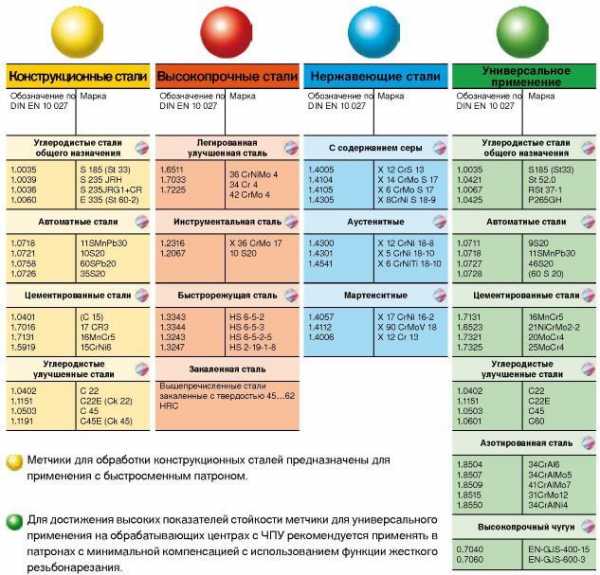
Цветовая маркировка
Степень наличия углерода в материале определяется в самом начале. Количество углерода для металла группы А указывается в сотых частях процента. Для Б и В – в десятых. В некоторых случаях после этих цифр производитель проставляет букву Г. Она означает, что в изделии содержится большое количество марганца.
Категории качественной стали
Качественные стали разной маркировки можно разделить на несколько категорий:
- 08пс, 08кп – имеют высокую пластичность. Хорошо подходят для холодной прокатки;
- От 10 до 25 – используется для горячей штамповки или прокатки;
- От 60 до 85 – применяется для выполнения ответственных конструкций, таких как рессоры, пружины, муфты сцепления;
- 30, 50, 30Г, 50Г – повышенной прочности, выдерживающие большие нагрузки.
Исключения в обозначениях
Качественные стали имеют некоторые исключения в обозначениях. К ним относятся:
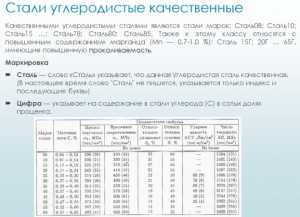
Качественные углеродистой стали
- 15К, 20К, 22К – применяются в строении котлов;
- 20-ПВ – имеет в своем составе 0.2 процента углерода и медь с хромом. Из нее выполняются трубы для систем отопления;
- ОсВ – содержит добавки никеля, хрома и меди. Из нее изготавливают оси железнодорожных вагонов;
- А75, АСУ10Е, АУ10Е – применима для деталей в часовых механизмах.
Из вышеперечисленного следует, что перед использованием изделия из углеродистой стали необходимо обратить внимание на его маркировку. Так можно определить его физико-химические свойства и область предназначения. Зная значение маркировки металлической продукции, не возникнет трудностей при подборе конкретного вида для любых целей.
Видео по теме: Углеродистые и легированные стали
promzn.ru