Химический состав стали
Свойства стали определяются ее химическим составом. Содержащиеся в стали компоненты можно разделить на четыре группы: постоянные (обыкновенные), скрытые, случайные и специальные (легирующие).
К постоянным примесям относятся углерод, марганец, кремний, сера и фосфор.
Углерод — неотъемлемая составляющая часть стали, оказывающая на ее свойства основное влияние. Его содержание в выпускаемых марках стали колеблется от 0,1 до 1,4 %. С увеличением содержания углерода в стали повышаются ее твердость и прочность, уменьшаются пластичность и вязкость.
Марганец относится к постоянным примесям, если его содержание составляет менее 1 %. При содержании более 1 % он является легирующим элементом.
Марганец является раскислителем стали. Он повышает ее прочность, износостойкость и прокаливаемость, снижает коробление при закалке, улучшает режущие свойства стали. Однако ударная вязкость при этом снижается. Сталь, содержащая 11—14 % марганца (сталь Гатфильда), отличается высокой износостойкостью, так как способна упрочняться при пластической деформации. Сталь, содержащая 10—12 % марганца, становится немагнитной.
Кремний также является раскислителем стали и легирующим элементом, если его содержание превышает 0,8 %. Он увеличивает прочностные свойства стали, предел упругости, коррозионную и жаростойкость, однако снижает ее ударную вязкость.
Сера и фосфор являются вредными примесями. Так, сера делает сталь «красноломкой», а фосфор, повышая твердость стали, снижает ее ударную вязкость и вызывает «хладноломкость», т. е. хрупкость при температурах ниже —50°C.
Скрытые примеси представляют собой кислород, азот
Случайные примеси — это медь, цинк, свинец, хром, никель и другие металлы, попадающие в сталь с шихтовыми материалами. В основном они ухудшают качество стали.
Специальные добавки (легирующие элементы) вводятся в сталь с целью придания ей тех или иных свойств. К ним относятся марганец, кремний, хром, никель, молибден, вольфрам, ванадий, бор, ниобий, цирконий, селен, теллур, медь и др.
Наиболее распространенным легирующим элементом является
Никель повышает прочность стали при сохранении высокой вязкости, препятствует росту зерна при нагреве, снижает коробление при закалке, увеличивает коррозионную стойкость и прокаливаемость. При содержании никеля 18—20 %-я сталь становится немагнитной, жаростойкой, жаропрочной и коррозионностойкой.
Молибден измельчает зерно стали, значительно повышает ее прокаливаемость, стойкость против отпуска, вязкость при низких температурах, ковкость и абразивную стойкость, снижает склонность к отпускной хрупкости.
Вольфрам повышает твердость и режущие свойства стали, прокаливаемость, прочность и вязкость. Стали с содержанием 9 и 18 % вольфрама известны как быстрорежущие.
Ванадий создает мелкозернистую структуру стали, задерживает рост зерна при нагреве, повышает ударную вязкость, устойчивость против вибрационных нагрузок, прокаливаемость и стойкость против отпуска.
Бор увеличивает прокаливаемость стали, повышает ее циклическую вязкость, способность гасить колебания высокой частоты, снижает склонность к необратимой отпускной хрупкости.
Ниобий предотвращает межкристаллическую коррозию, улучшает сварочные свойства, повышает пластичность, прочность и ползучесть стали при высоких температурах.
Цирконий повышает предел выносливости стали на воздухе и в коррозионных средах, улучшает ее прочностные характеристики при повышенных температурах и ударную вязкость при температуре ниже нуля, замедляет рост зерна, повышает прокаливаемость и свариваемость.
Медь повышает коррозионную стойкость стали, а селен и теллур — механические свойства стали и особенно ее пластичность.
Химический состав сталей, %
Сталь | ГОСТ | С | Mn | Si |
Ст4 Сталь45 20ХНЗА | 380—71 1050—60 | 0,18—0,27 0,42—0,50 0,17—0,23 | 0,40—0,70 0,50—0,80 0,30—0,60 | 0,12—0,30 0,17—0,37 0,17—0,37 |
Продолжение табл. 1
Сталь | ГОСТ | Cr | Ni | Р | |
Ст4 Сталь 45 20ХНЗА | 380—71 1050—60 4543—71 | ≤0,3 ≤0,25 0,60-0,90 | ≤0,3 ≤0,25 2,75-3,15 | ≤0,050 ≤0,045 ≤0,025 | ≤0,040 ≤0,040 ≤0,025 |
Сталь 45, согласно ГОСТ, в состоянии поставки (после прокатки и отжига) имеет твердость не более НВ 207. При твердости НВ 190— 200 сталь имеет предел прочности не выше 600—620 МПа, а при твердости ниже НВ 180 предел прочности не превышает 550—600 МПа. Для отожженной углеродистой стали отношение σт/σв составляет примерно 0,5. Следовательно, предел текучести стали 45 в этом состоянии не превышает 270—320 МПа.
Сталь 20ХНЗА, согласно ГОСТ, в состоянии поставки (после прокатки и отжига) имеет твердость не более
Таким образом, для получения заданной величины предела текучести вал необходимо подвергнуть термической обработке.
Для низкоуглеродистой стали Ст4 улучшающее влияние термической обработки незначительно. Кроме того, Ст4 — как сталь обыкновенного качества имеет повышенное содержание серы и фосфора (см. табл. 1), которые понижают механические свойства и особенно сопротивление ударным нагрузкам.
Для такого ответственного изделия, как вал двигателя, поломка которого нарушает работу машины, применение более дешевой по составу стали обыкновенного качества нерационально.
Сталь 45 относится к классу качественной углеродистой, а сталь 20ХН3А — к классу высококачественной легированной стали. Они содержат соответственно 0,42—0,50 и 0,17—0,23%С и принимают закалку.
Для повышения прочности можно применять нормализацию или закалку с высоким отпуском.
Последний вариант обработки сложнее, но позволяет получить не только более высокие характеристики прочности, но и более высокую вязкость. В стали 45 минимальные значения ударной вязкости (
Так как вал двигателя воспринимает в работе динамические нагрузки, а также и вибрации, более целесообразно применить закалку и отпуск. После закалки в воде углеродистая сталь 45 получает структуру мартенсита. Однако вследствие небольшой прокаливаемости углеродистой стали эта структура в изделиях диаметром более 20—25 мм образуется только в сравнительно тонком поверхностном слое толщиной до 2—4 мм.
Последующий отпуск вызывает превращение мартенсита и троостита в сорбит только в тонком поверхностном слое, но не влияет на структуру и свойства перлита и феррита в основной массе изделий.
Сорбит отпуска обладает более высокими механическими свойствами, чем феррит и перлит.
Наибольшие напряжения от изгиба, кручения и повторно переменных нагрузок воспринимают наружные слои, которые и должны обладать повышенными механическими свойствам. Однако в сопротивлении динамическим нагрузкам, которые воспринимает вал, участвуют не только поверхностные, но и нижележащие слои металла.
Таким образом, углеродистая сталь не будет иметь требуемых свойств по сечению вала диаметром 70 мм.
Сталь 20ХНЗА легирована никелем и хромом для повышения прокаливаемости и закаливаемости. Она получает после закалки достаточно однородные структуру и механические свойства в сечении диаметром до 75 мм.
Для стали 20ХНЗА рекомендуется термическая обработка:
1. Закалка с 820—835° С в масле.
При закалке с охлаждением в масле (а не в воде, как это требуется для углеродистой стали) возникают меньшие напряжения, а, следовательно, и меньшая деформация. После закалки сталь имеет структуру мартенсита и твердость не ниже HRC 50.
2. Отпуск 520—530° С. Для предупреждения отпускной хрупкости, к которой чувствительны стали с хромом (марганцем, вал после нагрева следует охлаждать в масле.
Механические свойства стали 20ХНЗА в изделии диаметром до 75 мм после термической обработки:
Предел прочности σв=900—1000 МПа, предел текучести σт = 750—800 МПа , относительное удлинение δ = 8—10 %, относительное сужение ψ = 45—50 %, ударная вязкость ан = 900 кДж /м2 .
Таким образом, эти свойства обеспечивают требования, формулированные в задаче, для вала диаметром 70 мм.
№ 2. Зубчатые колеса в зависимости от условий работы и возникающих напряжений можно изготавливать из стали обыкновенного качества, качественной углеродистой и легированной с различным содержанием легирующих элементов.
Выбрать, руководствуясь техническими и экономическими соображениями, сталь для изготовления колес диаметром 50 мм и высотой 30 мм с пределом прочности не ниже 360—380 МПа.
Указать термическую обработку колес, механические свойства и структуру выбранной стали в готовом изделии и для сравнения механические свойства и структуру сталей 45 и 40ХН после улучшающей термической обработки.
№ 3. Выбрать сталь для изготовления валов диаметром 50 мм для двух редукторов. По расчету сталь для одного из валов должна иметь предел текучести не ниже 350 МПа, а для другого — не ниже 500 МПа.
Указать: 1) состав и марку выбранных сталей; 2) рекомендуемый режим термической обработки; 3) структуру после каждой операции термической обработки; 4) механические свойства в готовом изделии.
Можно ли применять углеродистую сталь обыкновенного качества для изготовления валов требуемого сечения и прочности?
№ 4. Коленчатые валы диаметром 80 мм, работающие при повышенных напряжениях, изготавливают на одном заводе из качественной углеродистой стали, а на другом — из легированной стали.
Какую сталь следует применять для этой цели? Указать ее химический состав и марку.
Рекомендовать режим закалки и отпуска и сопоставить механические свойства, которые могут обеспечить углеродистая качественная и легированная стали выбранных марок для вала указанного диаметра.
№ 5. Выбрать сталь для изготовления тяжело нагруженных коленчатых валов диаметром 60 мм: предел прочности должен быть не ниже 750 МПа.
Рекомендовать состав и марку стали, режим термической обработки, структуру и механические свойства после закалки и после отпуска.
ЗАДАЧИ ПО ИНСТРУМЕНТАЛЬНЫМ
СТАЛЯМ И СПЛАВАМ
№ 6. Стойкость сверл и фрез, изготовленных из быстрорежущей стали умеренной теплостойкости марки Р12 и обрабатывавших конструкционные стали твердостью НВ 180—200, была удовлетворительной.
Однако стойкость этих сверл резко снизилась при обработке жаропрочной аустенитной стали.
Рекомендовать быстрорежущую сталь повышенной теплостойкости, пригодную для производительного резания жаропрочных сталей, указать ее марку и химический состав, термическую обработку и микроструктуру в готовом инструменте.
Сопоставить теплостойкость стали Р12 и выбранной стали.
Решение задачи № 6
Режущие инструменты для производительного резания изготовляют из быстрорежущих сталей, так как эти стали обладают теплостойкостью. Они сохраняют мартенситную структуру и высокую твердость при повышенном нагреве (500—650° С), возникающем в режущей кромке.
Однако стойкость инструментов из быстрорежущих сталей, подвергавшихся оптимальной термической обработке, определяется не только их химическим составом, структурой и режимом резания, но сильно зависит от свойств обрабатываемого материала.
При резании сталей и сплавов с аустенитной структурой (нержавеющих, жаропрочных и др.), получающих все более широкое применение в промышленности, стойкость инструментов и предельная скорость резания могут сильно снижаться по сравнению с получаемыми при резании обычных конструкционных сталей и чугунов с относительно невысокой твердостью (до НВ 220—250). Это связано главным образом с тем, что теплопроводность аустенитных сплавов пониженная. Вследствие этого тепло, выделяющееся при резании, лишь в небольшой степени поглощается сходящей стружкой и деталью и в основном воспринимается режущей кромкой. Кроме того,
эти сплавы сильно упрочняются под режущей кромкой в процессе резания, из-за чего заметно возрастают усилия резания.
Для резания подобных материалов, называемых труднообрабатываемыми, мало пригодны быстрорежущие стали умеренной теплостойкости, сохраняющие высокую твердость (HRC 60) и мартенситную структуру после нагрева не выше 615—620°С. Для обработки аустенитных сплавов необходимо выбирать быстрорежущие стали повышенной теплостойкости, а именно кобальтовые. Кобальт способствует выделению при отпуске наряду с карбидами также и частиц интерметаллидов, более стойких против коагуляции, и затрудняет процессы диффузии при температурах нагрева режущей кромки. Кобальтовые стали сохраняют твердость HRC 60 после более высокого нагрева: до 640—645° С. Кроме того, кобальт заметно (на 30—40%) повышает теплопроводность быстрорежущей стали, а следовательно, снижает температуры режущей кромки из-за лучшего отвода тепла в тело инструмента. Наконец, стали с кобальтом имеют более высокую твердость (до HRC 68 у стали Р8МЗК6С).
Для сверл и фрез, применяемых для резания аустенитных сплавов, рекомендуются кобальтовые стали марок Р12Ф4К5 или Р8МЗК6С. Термическая обработка кобальтовых сталей принципиально не отличается от обработки других быстрорежущих сталей. Она следующая.
Инструменты закаливают с очень высоких температур (1240— 1250° С для стали Р12Ф4К5 и 1210—1220° С для стали Р8МЗК6С), что необходимо для растворения большего количества карбидов и насыщения аустенита (мартенсита) легирующими элементами: вольфрамом, молибденом, ванадием и хромом. Еще более высокий нагрев, дополнительно усиливающий перевод карбидов в раствор, недопустим: он вызывает рост зерна, что снижает прочность и вязкость. Структура стали после закалки: мартенсит, остаточный аустенит (15—30%) и избыточные карбиды, не растворяющиеся при нагреве и задерживавшие рост зерна. Твердость HRC 60— 62.
Затем инструменты отпускают при 550—560° С (3 раза по 60 мин). Отпуска вызывает: а) выделение дисперсных карбидов и интерметаллидов из мартенсита (дисперсионное твердение), что повышает твердость до HRC 66—69; б) превращает мягкую составляющую — остаточный аустенит в мартенсит; в) снимает напряжения, вызываемые мартенситным превращением.
После отпуска инструменты шлифуют, а затем подвергают цианированию, чаще всего жидкому в смеси NaCN (50%) и Na2C03 (50%) с выдержкой 15—30 мин (в зависимости от сечения инструмента).
Твердость цианированного слоя на глубину 0,02—0,03 мм достигает HRC 69—70; немного (на 10° С) возрастает и теплостойкость. При нагреве для цианирования снимаются также напряжения, вызванные шлифованием. Цианирование повышает стойкость инструментов на 50—80%.
После цианирования целесообразен кратковременный нагрев при 450—500° С в атмосфере пара и с охлаждением в масле; поверхность инструмента приобретает тогда синий цвет и несколько лучшую стойкость против воздушной коррозии.
№ 7. Выбрать сталь для червячных фрез, обрабатывающих конструкционные стали твердостью НВ 220—240.
Объяснить причины, по которым для этого назначения нецелесообразно использовать углеродистую инструментальную сталь У12 с высокой твердостью (HRC 63—64).
Рекомендовать режим термической обработки фрез из выбранной быстрорежущей стали, приняв, что фрезы изготовлены из проката диаметром 40 мм.
№ 8. Завод должен изготовить долбяки, обрабатывающие с динамическими нагрузками конструкционные стали с твердостью НВ 200—230.
Выбрать марку быстрорежущей стали, наиболее пригодной для этого назначения, рекомендовать режим термической обработки и указать структуру и свойства (для долбяков наружным диаметром 60 мм).
№ 9. Завод изготовлял протяжки из высоковольфрамовой стали Р18.
Указать, можно ли использовать для протяжек менее легированную, а следовательно, более экономичную быстрорежущую сталь.
Выбрать марку стали для протяжек, обрабатывающих конструкционные стали с твердостью до НВ 250, указать ее термическую обработку, структуру и свойства для случаев, когда протяжки изготовляют из проката диаметром 40 и 85 мм.
ЗАДАЧИ ПО цветным металлам И СПЛАВАМ
№ 10. Многие изделия изготавливают из латуни вытяжкой из листа в холодном состоянии. Иногда в изделиях обнаруживаются трещины, возникающие без приложения внешних нагрузок (так называемое «сезонное растрескивание»). На рис. 1 показана деталь после глубокой вытяжки и после растрескивания при вылеживании.
Рис.
1. Растрескивание латунной детали после
глубокой вытяжки и вылеживания
Объяснить сущность этого явления и указать способы его предубеждения.
Подобрать марку латуни, не подверженной сезонному растрескиванию. Кроме того, описать структуру, технологические свойства α и α + β’-латуней.
Решение задачи № 10
Латуни в зависимости от содержания цинка и структуры можно разделить на три класса:
1. α-латуни ……. До 39,5% Zn
2. α + β’-латуни ….. От 39,5 до 45,7% Zn
3. β’-латуни ……. От 45,7 до 51% Zn
Увеличение содержания цинка изменяет структуру и свойства латуни (рис. 2).
Увеличение содержания цинка до определенного предела повышает пластичность и прочность. Пластичность достигает максимальных значений при 30—32% Zn, а прочность — при 40%. При дальнейшем увеличении содержания цинка прочность и пластичность снижаются.
Это изменение свойств определяется свойствами соответствующих фаз, образующихся при введении цинка.
α-фаза представляет твердый раствор типа замещения, пластичность и прочность которой возрастают по мере увеличения содержания цинка.
β’-фаза — твердый раствор на базе электронного соединения с центрированной кубической решеткой и упорядоченным расположением атомов. Эта фаза отличается повышенной хрупкостью и твердостью; поэтому образование β-фазы снижает вязкость и повышает твердость.
Рис. 2. Механические свойства латуни в зависимости от содержания цинка:
а — литая латунь; б — катаная и отожженная латунь
При нагреве выше 450° С β’-фаза превращается в неупорядоченный твердый раствор β, отличающийся большей пластичностью, чем β’-фаза. Из диаграммы состояния видно, что α + β’-латуни приобретают при таком нагреве однородную структуру β-твердого раствора, а следовательно, и большую пластичность.
Эти свойства фаз определяют технологический прогресс изготовления изделий из различных сортов латуни, а также их назначение.
Изделия из α-латуни изготавливают главным образом холодной или горячей деформацией; обработка резанием не дает достаточно чистой поверхности. Изделия из α + β’-латуни изготавливают горячей (прессование, штамповка) или холодной деформацией (но без вытяжки) или обработкой резанием.
В результате последующего отжига прочность сплава понижается, но пластичность возрастает (рис. 3).
Холодная деформация латуни создает в изделии остаточные напряжения. Они возникают и в результате местной холодной деформации (при изгибе деталей, чеканке, развальцовке и т. п.).
Рис. 3. Механические свойства латуни Л68 в зависимости:
а — от степени деформации; б — от температуры отжига
При вылеживании или эксплуатации в латунных изделиях иногда возникают трещины. «Сезонное растрескивание» наблюдается главные образом в латунях с содержанием более 20% Zn и отчетливо обнаруживается, например, в полых изделиях, прутках и т. д. Сезонное растрескивание усиливается в химически активных средах, особенно в парах аммиака, ртутных солях, ртути, мыльной воде и т. д. Образование трещин является результатом совместного действия остаточных напряжений, созданных холодной деформацией (наиболее опасны растягивающие напряжения), и химически активных сред.
Для предохранения от сезонного растрескивания нужен отпуск с нагревом до 200—300° С; это снимает большую часть остаточных напряжений и незначительно снижает прочность.
Но в условиях изготовления и монтажа конструкций с применением развальцовки, гибки и т. д. не всегда возможно избежать возникновения местных, даже незначительных деформаций, а, следовательно, и сезонного растрескивания. В таких случаях применяют более дорогие (и имеющие меньшую прочность), но не склонные к сезонному растрескиванию латуни Л96 и Л90. Латуни Л96 и Л90 обладают высокой теплопроводностью.
Латуни можно заменить алюминиевой бронзой, не склонной к сезонному растрескиванию и обладающей аналогичными значениями прочности и пластичности.
№ 11. Гребные винты морских пароходов имеют сложную форму и очень массивны, например масса винта современного крупного океанского теплохода достигает 30—50 т.
Наметить схему технологии изготовления винта, учитывая его форму. Исходя из этой схемы и условий работы винта в морской воде, подобрать состав сплава и указать его структуру и механические свойства.
№ 12. Некоторые детали арматуры турбин, котлов гидронасосов и т. п., работающие во влажной атмосфере и изготавливаемые массовыми партиями литьем, имеют сложную форму. В процессе литья должна быть обеспечена максимальная точность размеров.
Указать состав применяемого для этой цели цветного сплава, его структуру и механические свойства; привести способ литья, позволяющий создать требуемую высокую точность с минимальной последующей механической обработкой.
Привести химический состав стали для форм, применяемых для литья выбранного сплава, и указать режим термической обработки, а также структуру стали в готовом изделии.
№ 13. Многие детали приборов и оборудования, подверженные действию морской воды, изготавливают из цветного сплава путем холодной деформации в несколько операций.
Подобрать сплав, стойкий против действия морской воды, и привести его химический состав.
Указать режим промежуточной термической обработки выбранного сплава и привести его механические свойства после деформации и термической обработки. Сравнить состав стали, стойкой против действия морской воды;
привести режим ее термической обработки, механические свойства и структуру.
№ 14. Трубки в паросиловых установках должны быть стойки против коррозии.
Подобрать марку сплава на медной основе, пригодного для изготовления трубок и не содержащего дорогих элементов; привести состав выбранного сплава.
Указать способ изготовления трубок и сравнить механические свойства выбранного сплава, получаемые после окончательной обработки, с механическими свойствами стали, стойкой против коррозии в тех же средах.
studfile.net
Сталь Ст3: марки, характеристики, химический состав
Сталь представляет собой материал, в котором основными элементами становятся железо и углерод, а другие вещества включаются в состав для изменения эксплуатационных качеств или контролируются в определенном диапазоне. Довольно больше распространение получила сталь 3. Она применяется для производства самых различных заготовок. Сталь Ст3 многим известна по трубам, которые применяются при создании систем теплоснабжения. Характеристики стали и ее особенности, к примеру, химический состав определяют не только широкое распространение металла, но и определенные особенности термической обработки.


Химический состав
Каждая категория стали характеризуется своим определенным химическим составом. Он во многом определяет область применения создаваемых заготовок и сложности, которые возникают при термической обработке.
Химический состав стали Ст3 делает ее одним из самых распространенных материалов, которые можно встретить на рынке. Без этого металла сложно себе представить современные строительные работы.
Ключевыми моментами, которые касаются химического состава, назовем следующее:
- Как ранее было отмечено, основными химическими элементами являются железо и углерод. Первый элемент имеет концентрацию 97%, углерода всего 0,14-0,22%. Именно углерод определяет показатель твердости и некоторые другие физико-химические свойства структуры.
- В состав структуры включается относительно небольшое количество легирующих элементов. Основными элементами стали хром и никель, концентрация которых составляет 0,3%. В этой же концентрации в состав включается медь.


Химический состав
При большом количестве разновидностей сталей у рассматриваемой жестко контролируется концентрация вредных примесей, которыми являются фосфор и сера. Кроме этого, в состав в большой концентрации входит азот, на который приходится около 0,1 массы.
Физические и механические свойства
Сталь Ст3, характеристики которой будут рассмотрены подробно, применяется в качестве основы при изготовлении просто огромного количества различных заготовок. Это можно связать с уникальными физическими и механическими свойствами. Механические свойства стали Ст3, которые контролируются при выпуске заготовок, следующие:
- Временное сопротивление.
- Предел текучести.
- Степень изгиба под воздействием большого усилия.
- Относительное удлинение.
- Ударная вязкость при определенной температуре.
Наиболее важные технические характеристики углеродистой стали 3 следующие:
- Поверхность имеет твердость 131 МПа.
- Плотность стали неоднородная, вес также может варьироваться в большом диапазоне.
- Свариваемость не характеризуется какими-либо ограничениями.
- К отпускной хрупкости структура не склонна.


Стальные уголки
Рассматриваемые свойства стали 3 определяют ее широкое распространение именно в сфере строительства. Большое распространение получил и различный прокат, который применяется при механической обработке.
Расшифровка марок Ст3
Провести расшифровку любой марки можно в соответствии с установленными стандартами и нормативной документации. Обозначение стали по ГОСТ позволяет при расшифровке марок определить основные качества. ГОСТ 380 определяет наличие следующих разновидностей металла:
- Сталь Ст3сп.
- Сталь Ст3пс.
- Сталь Ст3кп.
Стоит учитывать, что индексы должны применяться при любой маркировке.


Свойства различных марок Ст3
Марка материала может расшифровываться следующим образом:
- СТ – обозначение, которое указывает на обыкновенное качество углеродистой стали. Примером назовем Ст3сп5.
- 3 – цифра, являющаяся условным номером марки сплава. В зависимости от концентрации углерода могут применяться цифры в пределе о 0 до 6.
- Г – в некоторых случаях может применяться подобный символ для обозначения марганца. Определенный тип стали, к примеру, Ст3гпс имеет в составе марганец 0,8%.
- Сп – степень раскисления материала. При рассмотрении Ст3пс5 можно сказать, что структура полуспокойная, но при этом степень раскисления достаточно высокая. Обозначение «пс» применяется для полуспокойных, «кп» — кипящих сплавов.


Швеллер СТ3ПС5
Расшифровывается Ст3кп2 подобным образом относительно недавно. Ранее использовались другие стандарты при маркировке. Кроме этого, ранее деление металла проводилось на несколько различных групп.
Скачать ГОСТ 380-2005
Применение стали Ст3
Рассматривая различные марки стали нужно учитывать тот момент, что они классифицируются по степени раскисления. Этот химический процесс предусматривает удаление с состава кислорода. Слишком большая концентрация кислорода определяет снижение физических и механических свойств.
Классификация проводится следующим образом:
- Спокойная характеризуется тем, что в состав входит от 0,16 до 0,3% кремния.
- Полуспокойная имеет средний показатель концентрации рассматриваемого элемента.
- Кипящая отличается по химическому составу от спокойной тем, что в составе содержится кремния не менее 0,05%.
Маркируется материал Ст3 соответствующим образом. Для проведения химического процесса могут использоваться различные вещества.
Стоит учитывать, что спокойная обходится намного дороже других вариантов исполнения. Это можно связать со следующими моментами:
- Структура однородная, за счет чего повышается степень защиты материала от воздействия окружающей среды.
- В состав входит небольшое количество кислорода, что и определяет высокие эксплуатационные качества.
При использовании спокойной стали могут изготавливать следующие изделия:
- Прокат листового и фасонного типа.
- Арматура и детали, которые можно применять для создания трубопровода. Для транспортировки теплоносителя или газа, другой среды могут применятся различные трубы. Для того чтобы они выдерживали высокую нагрузку и воздействие окружающей среды при изготовлении должны применять материалы, обладающие прочностью и твердостью. Кроме этого, уделяется внимание и себестоимости, так как слишком дорогие сплавы могут быть менее практичными в применении. Сталь 3 подходит в большей степени для изготовления подобных изделий.
- Основные и второстепенные элементы, применяемые при изготовлении подвесных конструкций и железнодорожных элементов. В железнодорожной отрасли наиболее востребованы металлы, которые имеют невысокую стоимость и высокие эксплуатационные качества. За счет больших размеров подвесных конструкций цена одного квадратного метра также имеет большое значение.


Стальная арматура
Полуспокойная разновидность стали, применение которой также весьма широкое, в составе имеет около одного процента кислорода. За счет этого характеристики твердости и пластичности выражены в меньшей степени. При применении стали 3 могут изготавливаться:
- Трубы. Подобный материал сегодня получил самое широкое распространение. Трубы применяются при создании отопительной системы, в качестве несущих элементов. Стоит учитывать, что трубы могут иметь различный диаметр и толщину создаваемых стенок. Рассматриваемый сплав обладает относительно невысокой коррозионной стойкостью, поэтому нужно проводить защиту поверхности от воздействия повышенной влажности.
- Листовой прокат также применяется крайне часто, особенно при изготовлении корпусных изделий или обшивке несущих конструкций. Толщина может варьировать в большом диапазоне. Прокат листовой может применяться при холодной гибке или штамповке. Эти два процесса характеризуются высокой производительностью. Именно поэтому рассматриваемый сплав получил самое широкое распространение.
- Квадраты и уголки часто применяются для получения несущих конструкций. Они характеризуются высокой прочностью, так как грани существенно повышают жесткость и могут распределять нагрузку. Уголки и квадраты характеризуются большим количеством параметров: толщина листа, угол расположения плоскостей, длина и форма поперечного сечения. Область применения – изготовление несущих конструкций и усиление уже существующих конструкций.
- Различные шестигранники. Они также получили широкое распространение, могут применяться в самых различных отраслях промышленности.


Лист стальной Ст3 горячекатаный
Кипящие сплавы получили широкое распространение по причине доступности. По стоимости они самые доступные, при этом получаемая структура характеризуется высокой степенью обрабатываемости. Кроме этого, сплав хорошо поддается термической обработке, однако эксплуатационные качества по причине высокой концентрации кислорода снижены.
В заключение отметим, что многие аналоги стали 3 обладают соответствующими эксплуатационными характеристиками. Зарубежные производители применяют собственные стандартны при маркировке. При этом концентрация вредных примесей выдерживается в определенном диапазоне. Применение самых современных технологий позволяет снизить количество фосфора и серы в составе, за счет материал становится более прочным и менее хрупким. В некоторых случаях проводится добавление легирующих элементов.
Если вы нашли ошибку, пожалуйста, выделите фрагмент текста и нажмите Ctrl+Enter.
stankiexpert.ru
определение, классификация, химический состав и применение
Как часто мы слышим слово «сталь». И произносят его не только профессионалы в области металлургического производства, но и обыватели. Без стали не обходится ни одна прочная конструкция. По сути, когда мы говорим о чем-то металлическом, то подразумеваем изделие из стали. Узнаем, из чего она состоит, и как ее классифицируют.
Определение
Сталь – это самый, пожалуй, популярный сплав, основой которого являются железо и углерод. Причем доля последнего колеблется от 0,1 до 2,14 %, а первый не может быть ниже 45 %. Простота производства и доступность сырья имеют определяющее значение при распространении этого металла на все сферы деятельности человека.
Основные характеристики материала меняются в зависимости от его химического состава. Определение стали, как сплава, состоящего из двух компонентов, железа и углерода, нельзя назвать полным. В него может входить, например, хром — для придания жаропрочности, а никель, чтобы обеспечить устойчивость к коррозии.
Обязательные компоненты материала способствуют появлению дополнительных преимуществ. Так, железо делает сплав ковким и легко деформируемым при определенных условиях, а углерод – прочность и твердость одновременно с хрупкостью. Именно поэтому его доля так мала в общей массе стали. Определение способа производства сплава привело к содержанию в нем марганца в количестве 1 % и кремния – 0,4 %. Существует целый ряд примесей, которые появляются при плавлении металла и от которых пытаются избавиться. Наряду с фосфором и серой, кислород и азот также ухудшают свойства материала, делая его менее прочным и изменяя пластичность.
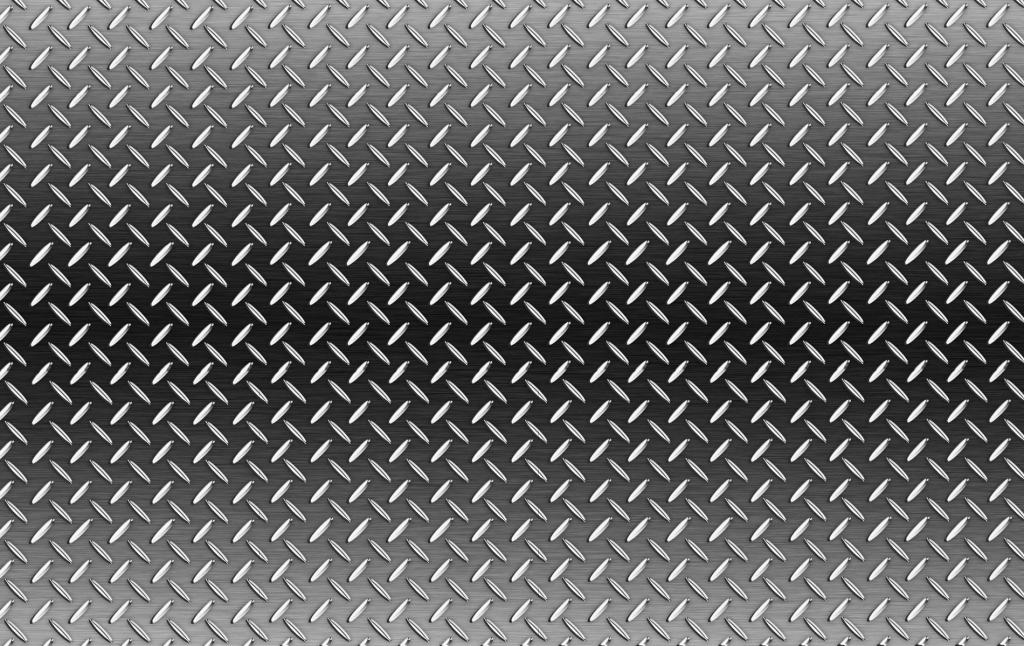
Классификация
Определение стали как металла с определенным набором характеристик, конечно, не вызывает сомнений. Однако именно ее состав позволяет классифицировать материал по нескольким направлениям. Так, например, различают металлы по следующим признакам:
- по химическому;
- по структурному;
- по качеству;
- по назначению;
- по степени раскисления;
- по твердости;
- по свариваемости стали.
Определение стали, маркировка и все ее характеристики будут описаны далее.
Маркировка
К сожалению, не существует мирового обозначения сталей, что значительно затрудняет торговые операции между странами. В России определена буквенно-цифровая система. Буквами обозначают название элементов и способ раскисления, а цифрами – их количество.
Химический состав
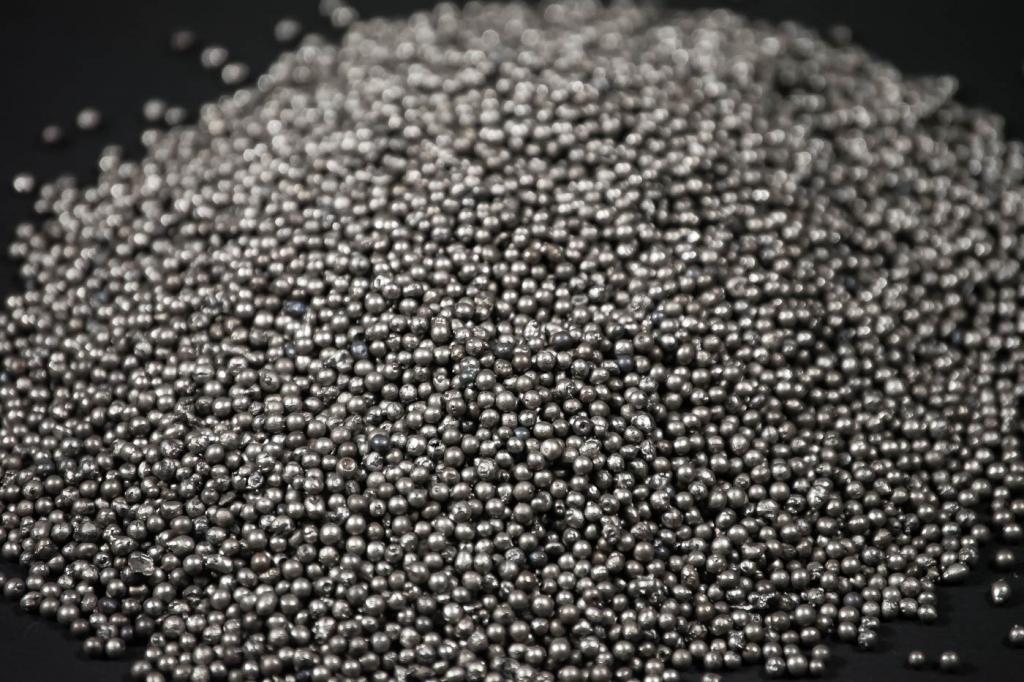
Существует два способа деления стали по химическому составу. Определение, которое дают современные учебники, позволяет различать углеродистый и легированный материал.
Первый признак определяет сталь как малоуглеродистую, среднеуглеродистую и высокоуглеродистую, а второй – низколегированную, среднелегированную и высоколегированную. Малоуглеродистым называют металл, который может включать согласно ГОСТу 3080-2005, помимо железа, следующие составляющие:
- Углерод – до 0,2 %. Он способствует термическому упрочнению, за счет которого временное сопротивление и твердость повышается в два раза.
- Марганец в количестве до 0,8 % активно вступает с кислородом в химическую связь и не допускает образование оксида железа. Металл лучше выдерживает динамические нагрузки и более податлив термическому упрочнению.
- Кремний – до 0,35 %. С помощью него становятся лучше механические характеристики, такие как вязкость, прочность, свариваемость.
По ГОСТу определение стали в качестве малоуглеродистой дают металлу, который содержит, кроме полезных, целый ряд вредных примесей в следующем количестве. Это:
- Фосфор – до 0,08 % отвечает за появление хладноломкости, ухудшает выносливость и прочность. Снижает ударную вязкость металла.
- Сера – до 0,06 %. Она усложняет обработку металла давлением, увеличивает отпускную хрупкость.
- Азот. Снижает технологические и прочностные свойства сплава.
- Кислород. Снижает прочность и препятствует обработке инструментов при резке.
Следует отметить, что низко- или малоуглеродистые стали отличаются особой мягкостью и пластичностью. Они хорошо деформируются как в горячем, так и в холодном состоянии.
Определение стали среднеуглеродистой так же, как и ее состав, конечно, отличаются от материала, описанного выше. И самым большим различием является количество углерода, которое колеблется от 0,2 до 0,45 %. Такой металл имеет небольшую вязкость и пластичность наряду с отличными свойствами по прочности. Из среднеуглеродистой стали обычно изготавливают детали, применяемые при обычных силовых нагрузках.
Если же содержание углерода составляет свыше 0,5 %, то такая сталь называется высокоуглеродистой. Она имеет повышенную твердость, сниженную вязкость, пластичность, используется при штамповке инструмента и деталей методом горячего и холодного деформирования.
Помимо выявления имеющегося в стали углерода, определение характеристик материала возможно через находящиеся в ней дополнительные примеси. Если в металл, кроме обычных элементов, целенаправленно вводят хром, никель, медь, ванадий, титан, азот в химически связанном состоянии, то его называют легированным. Такие добавки снижают риск хрупкого разрушения, увеличивают коррозионную стойкость и прочность. Их количество и обозначает степень легирования стали:
- низколегированная – имеет до 2,5 % легирующих добавок;
- среднелегированная – от 2,5 до 10 %;
- высоколегированная – до 50 %.
Что это значит? Например, повышение каких-либо свойств стали обеспечиваться следующим образом:
- Добавление хрома. Позитивно действует на механические характеристики уже в количестве 2 % от общего объема.
- Введение никеля от 1 до 5 % увеличивает температурный запас вязкости. И снижает хладноломкость.
- Марганец работает так же, как и никель, хотя значительно дешевле. Однако способствует повышению чувствительности металла к перегреву.
- Вольфрам — карбидобразующая добавка, обеспечивающая высокую твердость. Поскольку препятствует росту зерна при нагреве.
- Молибден – дорогостоящая добавка. Которая повышает теплостойкость быстрорежущих сталей.
- Кремний. Увеличивает кислотостойкость, упругость, окалиностойкость.
- Титан. Может способствовать образованию мелкозернистой структуру, если сочетается с хромом и марганцем.
- Медь. Повышает антикоррозионные свойства.
- Алюминий. Увеличивает жаростойкость, окалийность, ударную вязкость.
Структура
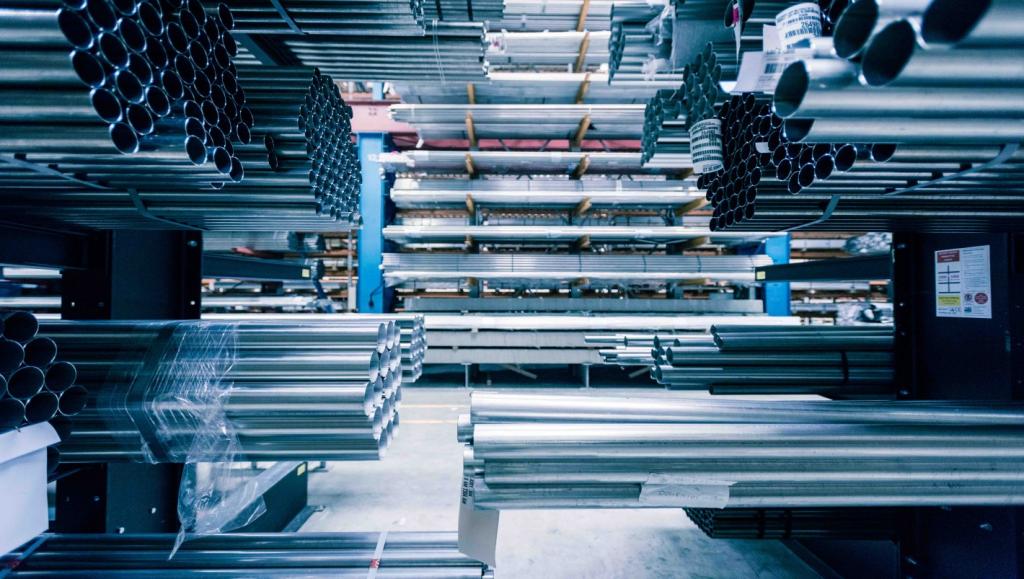
Определение состава стали было бы неполным без изучения ее структуры. Однако этот признак непостоянен, и может зависеть от целого ряда факторов, таких как: режим термообработки, скорость охлаждения, степень легирования. Согласно правилам структуру стали следует определять после отжига или нормализации. После отжига металл разделяют на:
- доэвтектоидную структуру – с избыточным ферритом;
- эвтектоидную, которая состоит из перлита;
- заэвтектоидную – со вторичными карбидами;
- ледебуритную – с первичными карбидами;
- аустенитную – с гранецентрированной кристаллической решеткой;
- ферритную – с кубической объемоцентрированной решеткой.
Определение класса стали возможно после нормализации. Под ней понимают вид термической обработки, включающий в себя нагрев, выдержку и последующее охлаждение. Здесь различают перлитный, аустенитный и ферритный классы.
Качество
Определение типов стало по качеству возможным по четырем направлениям. Это:
- Обыкновенного качества – это стали с содержанием углерода до 0,6 %, которые выплавляют в мартеновских печах или в конвертерах с использованием кислорода. Они считаются наиболее дешевыми и уступают по характеристикам металлам других групп. Примером таких сталей являются Ст0, Ст3сп, Ст5кп.
- Качественные. Яркими представителями этого типа являются стали Ст08кп, Ст10пс, Ст20. Выплавляются они с применением тех же печей, но с более высокими требованиями к шихте и процессам производства.
- Высококачественные стали плавят в электропечах, что гарантирует увеличение чистоты материала по неметаллическим включениям, то есть улучшение механических свойств. К таким материалам относят Ст20А, Ст15Х2МА.
- Особовысококачественные — изготавливают по методу специальной металлургии. Их подвергают электрошлаковому переплаву, который обеспечивает очистку от сульфидов и оксидов. К сталям этого типа относят Ст18ХГ-Ш, Ст20ХГНТР-Ш.
Конструкционные стали
Это, пожалуй, самый простой и понятный для обывателя признак. Различают конструкционные, инструментальные и специального назначения стали. Конструкционные принято разделять на:
- Строительные – это углеродистые стали обыкновенного качества и представители низколегированного ряда. К ним предъявляется несколько требований, основное из которых – свариваемость на достаточно высоком уровне. Примером служат СтС255, СтС345Т, СтС390К, СтС440Д.
- Из цементируемых делают изделия, которые работают в условиях поверхностного износа и параллельно испытывают динамические нагрузки. К ним относят малоуглеродистые стали Ст15, Ст20, Ст25 и некоторые легированные: Ст15Х, Ст20Х, Ст15ХФ, Ст20ХН, Ст12ХНЗА, Ст18Х2Н4ВА, Ст18Х2Н4МА, Ст18ХГТ, Ст20ХГР, Ст30ХГТ.
- Для холодной штамповки используют прокат листвой из качественных низкоуглеродистых образцов. Таких как Ст08Ю, Ст08пс, Ст08кп.
- Улучшаемые стали, которые подвергаются улучшению в процессе закалки и высокого отпуска. Это среднеуглеродистые (Ст35, Ст40, Ст45, Ст50), хромистые (Ст40Х, Ст45Х, Ст50Х, Ст30ХРА, Ст40ХР) стали, а также хромокремниемарганцевые, хромоникельмолибденовые и хромоникелевые.
- Рессорно-пружинные имеют упругие свойства и сохраняют их длительное время, так как имеют высокую степень сопротивляемости к усталости и разрушению. Это углеродистые представители Ст65, Ст70 и стали легированные (Ст60С2, Ст50ХГС, Ст60С2ХФА, Ст55ХГР).
- Высокопрочные образцы – те, которые имеют прочность в два раза большую, чем иные конструкционные стали, достигаемую термической обработкой и химическим составом. В основной массе это легированные среднеуглеродистые стали, например, Ст30ХГСН2А, Ст40ХН2МА, Ст30ХГСА, Ст38ХН3МА, СтОЗН18К9М5Т, Ст04ХИН9М2Д2ТЮ.
- Шарикоподшипниковые стали отличаются особой выносливостью, высокой степенью износоустойчивости и прочности. К ним обязательно предъявляются требования по отсутствию разного рода включений. К этим образцам относятся высокоуглеродистые стали с содержанием хрома в составе (СтШХ9, СтШХ15).
- Автоматные стали определение имеют следующее. Это образцы для использования при изготовлении неответственных изделий, таких как болты, гайки, винты. Такие запасные части обычно обрабатываются резанием. Поэтому основной задачей является повышение обрабатываемости деталей, чего добиваются введением в материал теллура, селена, серы и свинца. Такие добавки способствуют образованию при обработке ломкой и короткой стружки и уменьшению трения. Основные представители автоматных сталей обозначаются так: СтА12, СтА20, СтА30, СтАС11, СтАС40.
- К коррозионностойким относят легированные стали с содержанием хрома около 12 %, поскольку он образует оксидную пленку на поверхности, препятствующую возникновению коррозии. Представителями этих сплавов являются Ст12Х13, Ст20Х17Н2, Ст20Х13, Ст30Х13, Ст95Х18, Ст15Х28, Ст12Х18НЮТ,
- Износостойкие образцы применяют в изделиях, которые работают при абразивном трении, ударах и сильном давлении. Примером могут служить детали железнодорожных путей, дробильных и гусеничных машин, такая как Ст110Г13Л.
- Жаропрочные стали могут работать при высоком нагреве. Их используют при изготовлении труб, газо- и паротурбинных запчастей. Это в основном высоколегированные малоуглеродистые образцы, имеющие обязательно в составе никель, которые могут содержать добавки в виде молибдена, нобия, титана, вольфрама, бора. Примером могут являться Ст15ХМ, Ст25Х2М1Ф, Ст20ХЗМВФ, Ст40ХЮС2М, Ст12Х18Н9Т, СтХН62МВКЮ.
- Жаростойкие отличаются особой стойкостью против химических разрушений в воздухе, газовых и печных, окислительных и науглероживающих средах, но проявляют ползучесть при серьезных нагрузках. Представителями этого типа являются Ст15Х5, Ст15Х6СМ, Ст40Х9С2, Ст20Х20Н14С2.
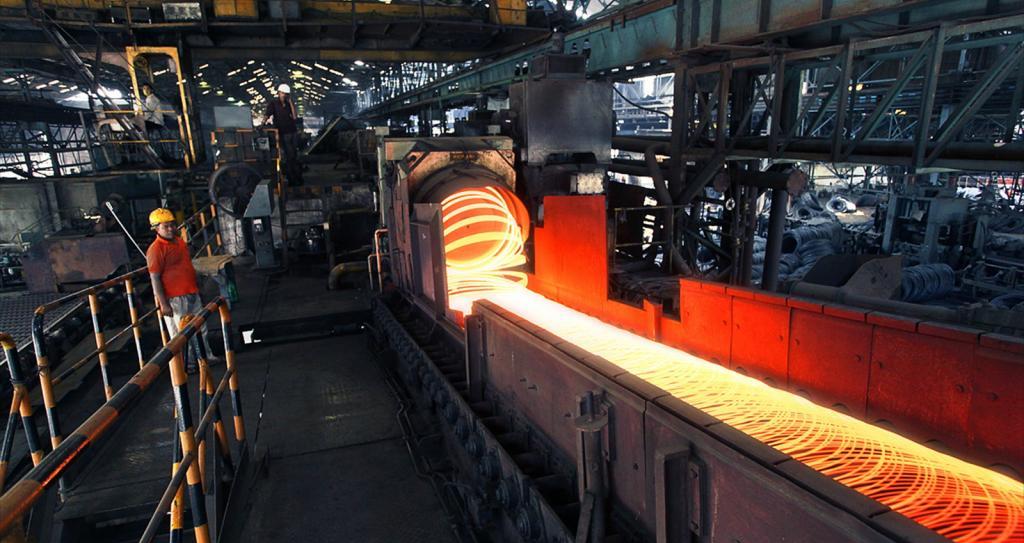
Стали инструментального назначения
В этой группе сплавы делят на штамповые, для режущих и измерительных инструментов. Стали для штампов бывают двух видов.
- Материал для холодного деформирования должен иметь высокую степень твердости, прочности, износостойкости, теплостойкости. Но иметь достаточную вязкость (СтХ12Ф1, СтХ12М, СтХ6ВФ, Ст6Х5ВМФС).
- Материал для горячего деформирования отличается хорошей прочностью и вязкостью. Наряду с износостойкостью и окалиностойкостью (Ст5ХНМ, Ст5ХНВ, Ст4ХЗВМФ, Ст4Х5В2ФС).
Стали для измерительных инструментов, кроме износостойкости и твердости, должны отличаться постоянством размеров и легко шлифоваться. Из этих сплавов изготавливаются калибры, скобы, шаблоны, линейки, шкалы, плитки. Примером могут быть сплавы СтУ8, Ст12Х1, СтХВГ, СтХ12Ф1.
Определение групп сталей для режущих инструментов осуществляется достаточно легко. Такие сплавы должны обладать режущей способностью и высокой твердостью продолжительное время, даже если подвергаются нагреву. К ним относят углеродистые и легированные инструментальные, а также быстрорежущие стали. Здесь можно назвать следующих ярких представителей: СтУ7, СтУ13А, Ст9ХС, СтХВГ, СтР6М5, СтРЮК5Ф5.
Раскисление сплава
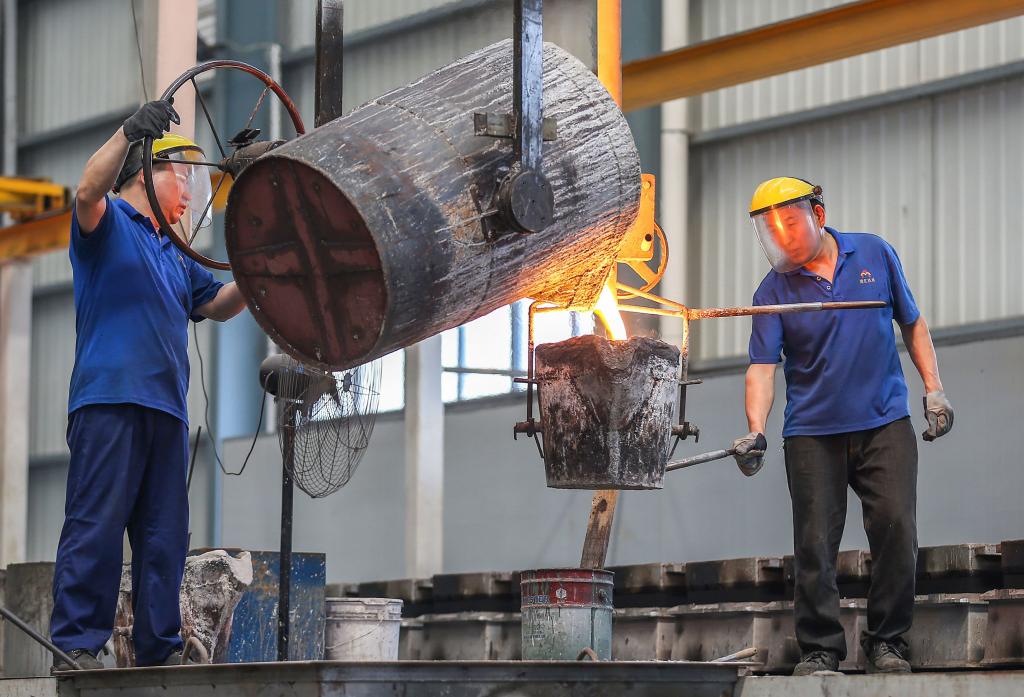
Определение стали по степени раскисления подразумевает три ее вида: спокойная, полуспокойная и кипящая. Само же понятие обозначает удаление кислорода из жидкого сплава.
У спокойной стали при затвердевании газы почти не выделяются. Так происходит из-за полного удаления кислорода и образования сверху слитка усадочной раковины, которую затем обрезают.
У полуспокойной стали газы выделяются частично, то есть больше, чем в спокойных, но меньше, чем в кипящих. Здесь отсутствует раковина, как в предыдущем случае, но вверху образуются пузыри.
Кипящие сплавы выделяют большое количество газа при затвердевании, а в поперечном сечении достаточно просто заметить разницу химического состава между верхним и нижним слоями.
Твердость
Это понятие обозначает способность материала сопротивляться более твердому, проникающему в него. Определение твердости стало возможно с использованием трех методов: Л. Бринеля, М. Роквелла, О. Викерса.
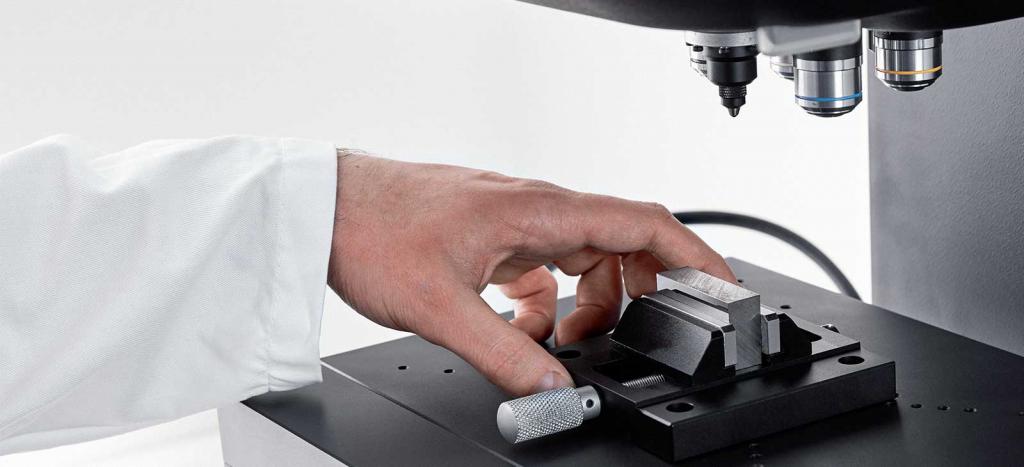
Согласно способу Бринеля закаленный стальной шарик вдавливают в отшлифованную поверхность образца. Изучая диаметр отпечатка, определяют твердость.
Метод определения твердости стали по Роквеллу. Он основан на подсчете глубины проникновения наконечника в виде алмазного конуса с углом в 120 градусов.
По Викерсу в испытываемый образец вдавливается алмазная четырехгранная пирамида. С углом 136 градусов у противоположных граней.
Можно ли определить марку стали без химического анализа? Специалисты в области металловедения способны узнать марку стали по искре. Определение составляющих металла возможно при его обработке. Так, например:
- Сталь ХВГ имеет темно-малиновые искры с желто-красными крапинками и пучками. На концах разветвленных нитей появляются ярко-красные звездочки с желтыми крупками в середине.
- Сталь Р18 также определяется по темно-малиновым искрам с желтыми и красными пучками в начале, однако нити прямые и не имеют разветвлений. На концах пучков имеются искры с одной или двумя светло-желтыми крупинками.
- Стали марок ХГ, Х, ШХ15, ШХ9 имеют желтые искры со светлыми звездочками. И красными крупинками на разветвлениях.
- Сталь У12Ф отличается светло-желтыми искрами с густыми и крупными звездами. С несколькими красно-желтыми пучками.
- Стали 15 и 20 имеют светлые желтые искры, много разветвлений и звезд. Но мало пучков.
Определение стали по искре является достаточно точным методом для специалистов. Однако обыватели не могут дать характеристику металлу, изучив только цвет искры.
Свариваемость
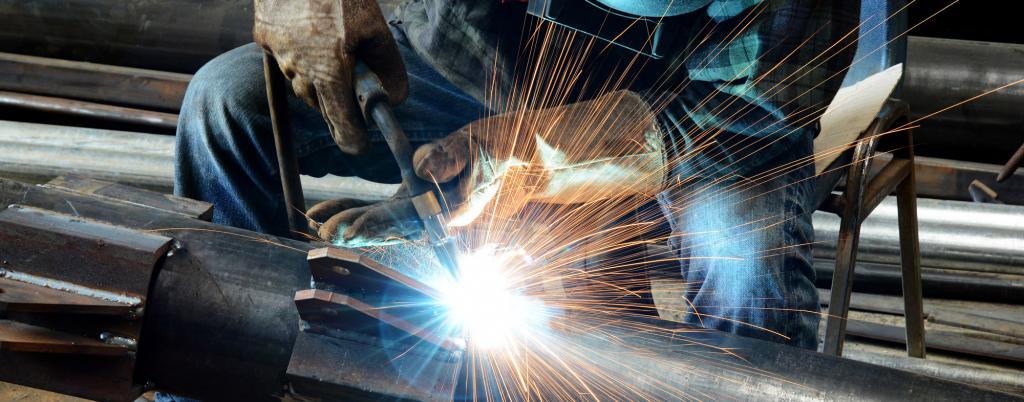
Свойство металлов образовывать соединение при определенном воздействии называется свариваемостью сталей. Определение данного показателя возможно после того, как будет выявлено содержание железа и углерода.
Считается, что хорошо соединяются посредством сварки низкоуглеродистые стали. Когда содержание углерода превышает 0,45 %, свариваемость ухудшается и становится наиболее плохой при большом содержании углерода. Это происходит и потому, что повышается неоднородность материала, а на границах зерен выделяются сульфидные включения, которые приводят к образованию трещин и увеличению внутреннего напряжения.
Также действуют и легирующие компоненты, ухудшая соединение. Самыми неблагоприятными для сварки называют такие химические элементы как хром, молибден, марганец, кремний, ванадий, фосфор.
Однако соблюдение технологии при работе с низколегированными сталями обеспечивает хороший процент свариваемости без применения специальных мероприятий. Определение свариваемости возможно после оценки ряда важных качеств материала, в числе которых:
- Скорость охлаждения.
- Химический состав.
- Вид первичной кристаллизации и структурных изменений при сварке.
- Возможность металла образовывать трещины.
- Склонность материала к возникновению закалочных формирований.
fb.ru
Что же добавляют в сталь?
Сегодня хочу осветить химические элементы, входящие в состав стали и придающие ей какие-либо полезные качества.
ОБНОВЛЕНО! Внизу статьи представлены пробные варианты таблицы по составу и маркам стали. Остальные в процессе сборки и будут добавлены позже.
Итак, вот перечень часто используемых химических элементов (после скобок указано обозначение элемента в маркировке стали):
азот ( N ) — А | марганец ( Mn ) — Г |
Теперь разберем подробнее влияние тех или иных элементов на вещество, в нашем случае сталь. Химический состав сталей (таблица).
Углерод — главный элемент, определяющий свойства стали. Именно благодаря углероду сталь способна принимать закалку. От количества углерода зависит твёрдость и прочность стали для ножей, хотя он же повышает склонность стали к коррозии. Относительно стали для ножей, нас интересуют стали с количеством углерода не меньше 0.6%. Именно с этой отметки сталь может принимать закалку на нормальную твёрдость. Правда производители часто используют стали и с количеством углерода 0.4%-0.6%, как правило, на недорогих простеньких ножах, на кухонных ножах.
Хром — следующий по распространённости в сталях элемент. Хром помогает сплаву сопротивляться коррозии и делает её нержавеющей. Официально сталь считается «нержавеющей» если хрома в ней не меньше 14%. Помимо своего главного свойства Хром негативно влияет на прочность стали.
Молибден — используется как легирующая добавка, повышающая жаропрочность и коррозионную стойкость стали. Молибден усиливает действие хрома в сплаве, улучшает прокаливаемость, делает состав более равномерным. По сути, улучшает почти все свойства сплава. Молибден обязательный элемент в быстрорежущих сталях. Стали с добавкой молибдена используются для изготовления деталей работающих в агрессивных средах и при высокой температуре. То есть в химической промышленности, в деталях реактивных двигателей. Нож из лопатки самолётной турбины уже стал притчей. Те стали, из применяемых в производстве ножей, в составе которых имеется этот элемент, зарекомендовали себя с наилучшей стороны. Пример-сталь 154CM она же ATS-34 с содержанием молибдена 4% по идее она и предназначалась для тех самых лопаток турбин.
Ванадий — замечательный элемент, способный улучшать свойства многих сплавов. Улучшает прочность и значительно повышает износостойкость стали. Его добавляют во всё те же быстрорежущие и инструментальные стали. Для нас это означает, что сталь для ножа будет дольше держать заточку при резе картона, войлока, канатов и других подобных материалов. Но нож будет тяжелее точиться. Пример-стали CPM S30V, CPM S90V и подобные им.
Вольфрам — металл с самой высокой температурой плавления из всех металлов. Используется во множестве всевозможных приборов и отраслей, от лампочек до ядерных реакторов. Вольфрам, неотъемлемый элемент в составе быстрорежущих сталей. Помимо устойчивости к температурам, сталь для ножа получает свойства, положительно влияющие на твёрдость и износостойкость.
Кобальт — ещё один металл с множеством применений, от корма для коров до космических кораблей. В некоторых количествах кобальт добавляется в быстрорежущие стали и твёрдые сплавы. Из сталей, применяемых в ножах, кобальт содержат стали VG-10 и N690 в количестве около 1.5%.
Азот — применяют в сталях как заменитель углерода и никеля. Азот повышает стойкость к коррозии и износостойкость стали для ножа. И позволяет стали с очень низким содержанием углерода принимать закалку. Например японская сталь Н1 в которой всего лишь 0.15% углерода, но 0.1% Азота позволяют закалять её на 58HRC и делают её практически абсолютно нержавеющей.
Никель — так же повышает коррозионную стойкость стали и способен несколько повысить прочность. Много никеля присутствует во всё той же стали Н1.
Кремний — необходимый в производстве сталей элемент. Он удаляет из металла кислород. Ну и заодно несколько повышает прочность и коррозионную стойкость.
Сера – это совсем не полезный элемент, она снижает механические свойства стали и уменьшает стойкость стали к коррозии. Поэтому серы в сталях обычно очень мало, лишь то, что не удалось удалить из стали в процессе её производства. Однако сера может быть добавлена, чтобы повысить обрабатываемость каких-нибудь жутко износостойких сталей.
Фосфор — вредная примесь, в стали ему не место, а особенно в стали для ножа, ибо он повышает хрупкость и снижает механические свойства стали. Фосфор стараются удалить из стали.
Марганец — как полезный и нужный элемент применяется на стадии выплавки стали, способен повышать твёрдость стали. Из сталей со значительным содержанием марганца делают всякие брутальные и монстрообразные вещи — рельсы, танки, сейфы.
Титан — может добавляться в сплавы для повышения прочности, стойкости к коррозии и температурам. В ножевых сталях титан, как добавка в принципе не актуален, так как количества его там ничтожные.
Ниобий — повышает коррозионную стойкость и износостойкость стали. Ниобий в сталях (или стали с ниобием) жуткая экзотика, но его можно найти в сплаве CPM S110V.
Алюминий — повышает жаростойкость и стойкость к окалине.
Медь — увеличивает антикоррозионные свойства, она вводится главным образом в строительную сталь.
Церий — повышает прочность и особенно пластичность.
Цирконий — оказывает особое влияние на величину и рост зерна в стали , измельчает зерно и позволяет получать сталь с заранее заданной зернистостью.
Лантан — уменьшают пористость, способствуют уменьшению содержания серы в стали, улучшают качество поверхности, измельчают зерно.
Цезий — способствуют уменьшению содержания серы в стали , улучшают качество поверхности, измельчают зерно.
Неодим — уменьшают пористость, способствуют уменьшению содержания серы в стали.
Кстати, вот интересная информация по применению никелевых катодов и анодов при никелировании никелевые аноды
Далее приведу наиболее удобную форму представления подробного химического состава основных марок отечественной и зарубежной стали. Нажимаем на картинку и получаем увеличенное изображение. Картинки пронумерованы в соответствии с очередностью представления в общей таблице.
Таблица 1
Таблица 2
Таблица 3
Таблица 4
Обновлено! По Вашим просьбам я начал формирование сводной таблицы по маркам стали. На данный момент представляю Вам несколько образцов штамповой инструментальной стали. Для удобного использования данных таблиц — скачиваем их. В последствии обязательно сделаю один общий архив.
- Х12МФ
- Х6ВФ
- 6ХВГ
- 5ХНМ
spiculo.ru